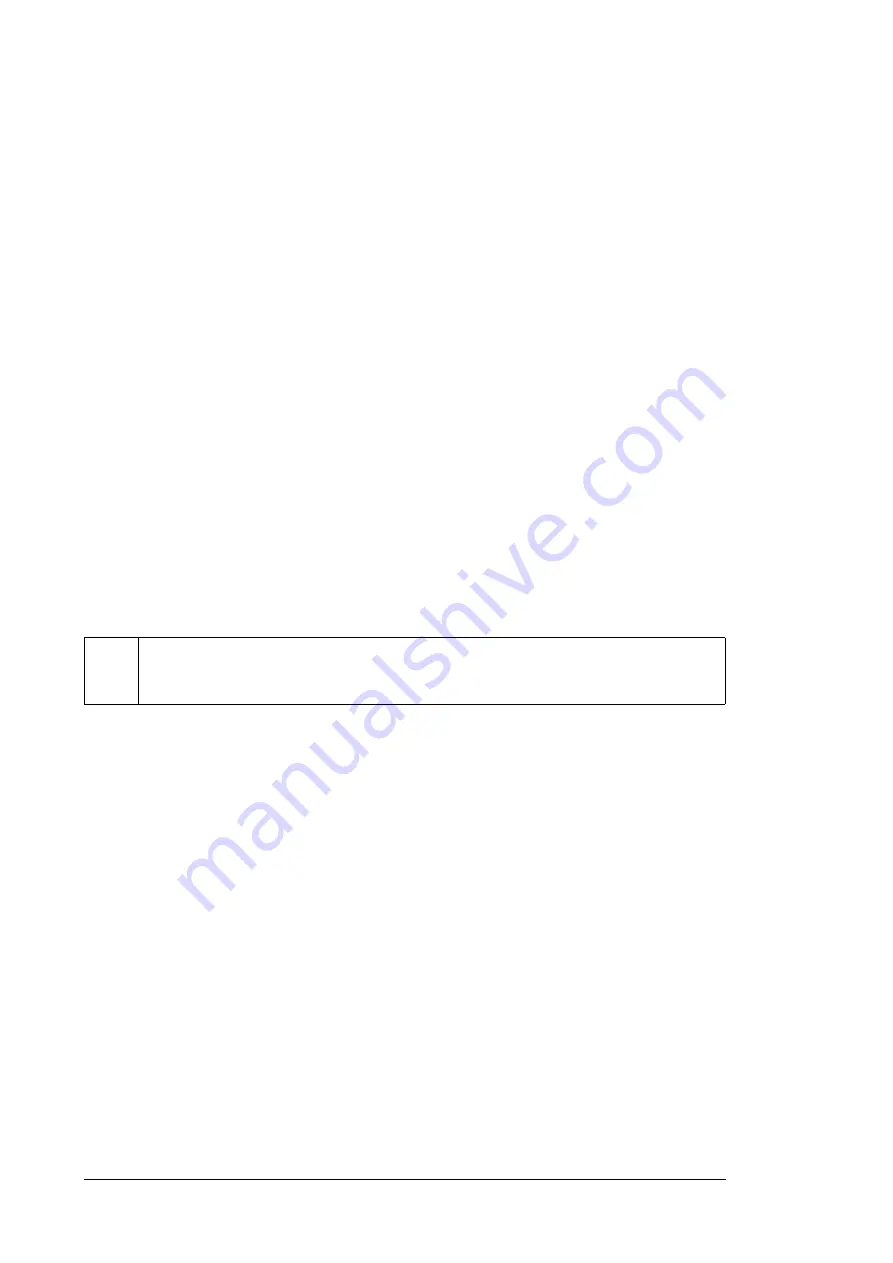
50 Guidelines for planning the electrical installation
Protecting the motor insulation and bearings
The drive employs modern IGBT inverter technology. Regardless of frequency, the drive
output comprises pulses of approximately the drive DC bus voltage with a very short rise
time. The pulse voltage can almost double at the motor terminals, depending on the
attenuation and reflection properties of the motor cable and the terminals. This can cause
additional stress on the motor and motor cable insulation.
Modern variable speed drives with their fast rising voltage pulses and high switching
frequencies can generate current pulses that flow through the motor bearings. This can
gradually erode the bearing races and rolling elements.
Optional du/dt filters protect motor insulation system and reduce bearing currents.
Optional common mode filters mainly reduce bearing currents. Insulated N-end (non-drive
end) bearings protect the motor bearings.
Examining the compatibility of the motor and drive
Use an asynchronous AC induction motor, permanent magnet synchronous motor, AC
induction servomotor or ABB synchronous reluctance motor (SynRM motor) with the drive.
Several induction motors can be connected to the drive at a time.
Select the motor size and drive type from to the rating tables in chapter
basis of the AC line voltage and motor load. Use the DriveSize PC tool if you need to tune
the selection more in detail.
Make sure that the motor withstands the maximum peak voltage in the motor terminals.
This voltage can typically be twice the DC link voltage (
U
DC
) of the drive:
Note
: The voltage peaks at the motor terminals are relative to the supply voltage of the
drive, not the drive output voltage.
Note
: Consult the motor manufacturer before using a motor whose nominal voltage differs
from the AC line voltage connected to the drive input.
U
DC
1.35 · 1.25 · 415 V DC (when supply voltage is 380 to 415 V AC)
1.35 · 1.25 · 500 V DC (when supply voltage is 440 to 500 V AC) or
Содержание ACS580-07-0495A-4
Страница 1: ...ABB general purpose drives Hardware manual ACS580 07 drives 250 to 500 kW ...
Страница 4: ......
Страница 8: ...4 Update notice ...
Страница 16: ...12 ...
Страница 24: ...20 Safety instructions ...
Страница 42: ...38 Operation principle and hardware description ...
Страница 74: ...70 Electrical installation PE PE 8 PE 13 11 7 8 12 13 ...
Страница 82: ...78 Electrical installation ...
Страница 102: ...98 Fault tracing ...
Страница 114: ...110 Maintenance R10 and R11 4 5 2 7 6 3 8 ...
Страница 115: ...Maintenance 111 R10 and R11 9 10 ...
Страница 116: ...112 Maintenance R10 and R11 11 ...
Страница 117: ...Maintenance 113 R10 and R11 12b 12a ...
Страница 118: ...114 Maintenance R10 and R11 R10 and R11 17 14 13 R11 15 16 ...
Страница 126: ...122 Technical data Input and motor cable terminal dimensions of frame R10 Bottom entry and exit ...
Страница 127: ...Technical data 123 Input and motor cable terminal dimensions of frame R11 Bottom entry and exit ...
Страница 134: ...130 Technical data ...
Страница 137: ...Dimension drawings 133 13 Dimension drawings Example dimension drawings are shown below ...
Страница 138: ...134 Dimension drawings Frames R10 and R11 IP42 ...
Страница 139: ...Dimension drawings 135 Frames R10 and R11 IP54 option B055 ...
Страница 140: ...136 Dimension drawings ...
Страница 152: ...148 Safe torque off function ...
Страница 174: ...Contact us www abb com drives www abb com drivespartners 3AXD50000032622 Rev A EN 2016 03 16 ...