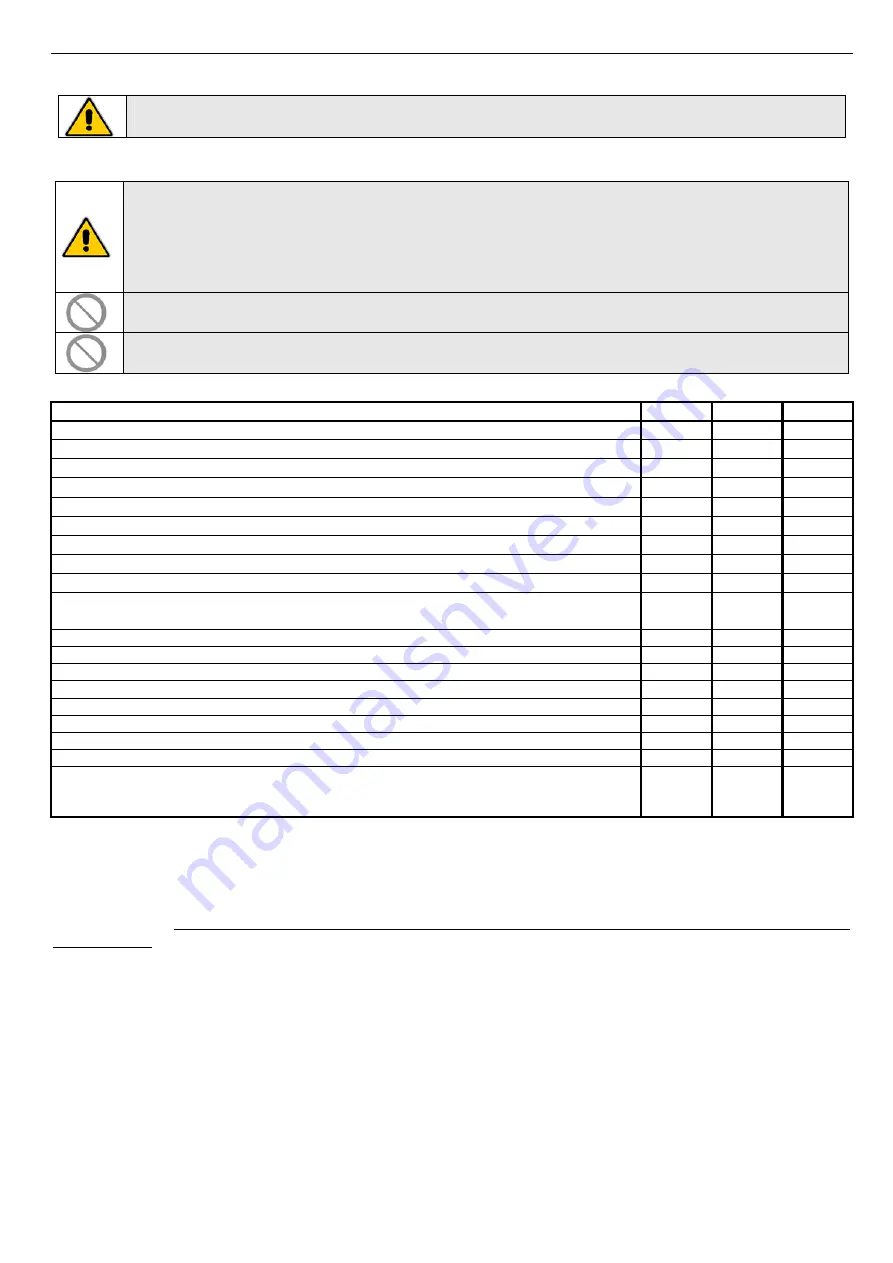
2
6
• Place
the
general
differential
circuit
breaker
to
"OFF"
position.
If
the
temperature
drops
below
0°C
there
is
serious
danger
of
frost:
add
a
mixture
of
water
and
glycol
in
the
system,
otherwise
drain
the
hydraulic
circuits
of
the
system
and
of
the
heat
pump.
11
MAINTENANCE
AND
PERIODICAL
CONTROLS
WARNING:
All
the
operations
described
in
this
chapter
HAVE
TO
BE
CARRIED
OUT
BY
TRAINED
STAFF
ONLY.
Before
any
operation
or
before
entering
the
inner
components
of
the
unit,
be
sure
that
the
power
supply
is
disconnected.
The
compressor’s
heads
and
discharge
piping
are
usually
at
high
temperature
levels.
Be
very
careful
when
operating
in
their
surroundings.
Aluminium
coil
fins
are
very
sharp
and
can
cause
serious
wounds.
Be
very
careful
when
operating
in
their
surroundings.
After
maintenance
operations,
re
‐
install
the
cover
panels,
and
fix
them
by
means
of
screws.
The
refrigerant
circuits
must
not
be
filled
with
different
gas
other
than
that
indicated
on
the
nameplate.
The
use
of
a
different
refrigerant
can
cause
severe
damage
to
the
compressor.
It’s
forbidden
to
use
oils
other
than
those
specified
in
this
manual.
The
use
of
a
different
oil
can
cause
serious
damage
to
the
compressor.
It
is
a
good
rule
to
carry
out
periodic
checks
in
order
to
verify
the
proper
operation
of
the
unit.
OPERATION
1
month
4
month
6
month
Filling
the
water
circuit.
x
Presence
of
bubbles
in
the
water
circuit.
x
Check
out
that
safety
and
control
devices
work
correctly
x
Check
out
possible
oil
leakage
from
compressor.
x
Check
out
possible
water
leakages
from
the
hydraulic
circuit.
x
Check
out
the
proper
working
of
the
flow
switches.
x
Check
out
that
the
crankcase
resistances
are
properly
supplied
and
functioning.
x
Clean
the
metallic
filters
of
the
hydraulic
circuit.
x
Clean
the
finned
coil
by
means
of
compressed
air
or
water
jet.
x
Check
out
that
all
the
terminals
on
the
electric
board
as
well
as
on
the
terminals
of
the
compressor
are
properly
fixed.
x
Tightening
of
water
connections.
x
Check
out
the
tightening
and
the
balancing
of
the
fan
blades.
x
Correct
voltage.
x
Correct
absorption.
x
Check
the
refrigerant
charge.
x
Check
the
operating
pressure,
and
superheat
and
subcooling
x
Check
of
the
efficiency
of
circulation
pump.
x
Check
the
expansion
tank.
x
If
the
unit
should
be
out
of
service
for
a
long
period,
discharge
water
from
the
piping
and
from
heat
exchanger.
This
operation
is
necessary
if,
during
seasonal
stoppages,
ambient
temperature
is
expected
to
go
down
below
the
freezing
point
of
the
employed
fluid.
x
11.1
ENVIRONMENTAL
PROTECTION
According
to
the
norms
dealing
with
the
use
of
depleting
stratospheric
ozone
substances,
it
is
forbidden
to
release
refrigerants
fluids
in
the
atmosphere.
They
have
to
be
collected
and
delivered
to
the
seller
or
to
proper
gathering
points
at
the
end
of
their
operating
life.
Refrigerant
R410A
is
mentioned
among
controlled
substances
and
for
this
reason
it
has
to
be
subjected
to
the
mentioned
norms.
A
particular
care
is
recommended
during
service
operations
in
order
to
reduce
as
much
as
possible
any
refrigerant
loss.
12
WHEN
THE
UNIT
GOES
OUT
OF
SERVICE
Once
the
unit
is
arrived
at
the
end
of
its
life
cycle
and
needs
to
be
removed
or
replaced,
the
following
operations
are
recommended:
• the
refrigerant
has
to
be
recovered
by
trained
people
and
sent
to
proper
collecting
centre;
• compressors’
lubricating
oil
has
to
be
collected
and
sent
to
proper
collecting
centre;
• the
frame
and
the
various
components,
if
not
serviceable
any
longer,
have
to
be
dismantled
and
divided
according
to
their
nature,
particularly
copper
and
aluminium,
which
are
present
in
conspicuous
quantity
in
the
unit.
These
operations
allow
easy
material
recover
and
recycling
process,
thus
reducing
the
environmental
impact.
Содержание HPE Series
Страница 21: ......
Страница 29: ...28 ...
Страница 31: ...30 16 WATER PUMP CURVES 16 1 MODELS HPE 06 09 16 2 MODELS HPE 12 15 ...
Страница 34: ...33 19 3 HPE 12 15 IN OUT 1 M ...
Страница 35: ...34 20 WIRING DIAGRAMS 20 1 MODELS HPE 06 09 ...
Страница 36: ...35 20 2 MODEL HPE 12 ...
Страница 37: ...36 20 3 MODEL HPE 15 ...
Страница 43: ...NOTE ...
Страница 44: ...NOTE ...
Страница 45: ...NOTE ...
Страница 46: ...NOTE ...
Страница 47: ......