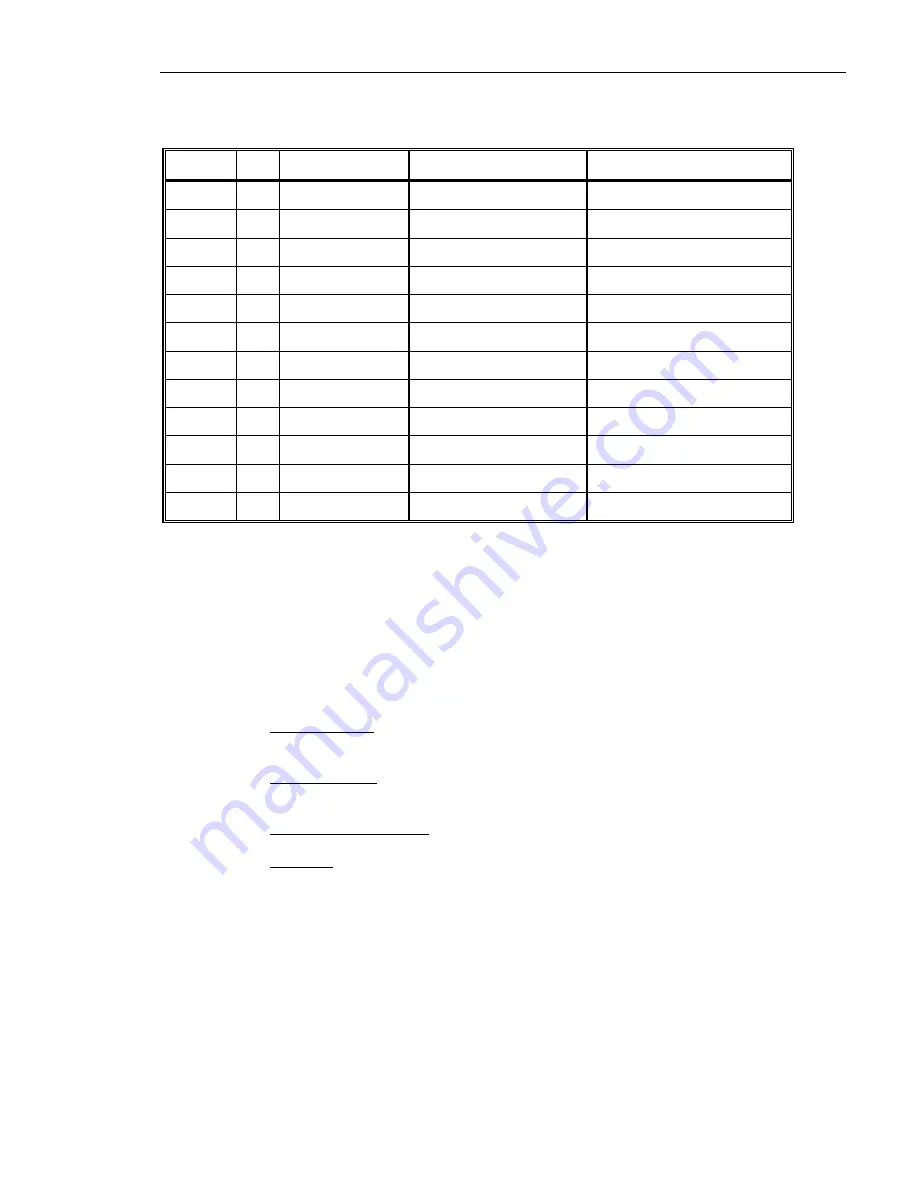
FUNCTIONAL DESCRIPTION
IV-15
I/O Signal Summary
Pin No. I/O
Signal Name
Definition
Comments
5
I/O
B1 +
Battery Charge Pin
1
I
B1 SENS +
Battery Sense
Battery #1 detection signal.
9
I/O
B1 -
Battery Return
6
I/O
B2 +
Battery Charge Pin
2
I
B2 SENS +
Battery Sense
Battery #2 detection signal.
10
I/O
B2 -
Battery Return
7
I/O
B3 +
Battery Charge Pin
3
I
B3 SENS +
Battery Sense
Battery #3 detection signal.
11
I/O
B3 -
Battery Return
8
I/O
B4 +
Battery Charge Pin
4
I
B4 SENS +
Battery Sense
Battery #4 detection signal.
12
I/O
B4 -
Battery Return
Diagnostics
The following sections describe several types of diagnostics that will be performed by the
system to insure product safety and simplify assembly and test requirements.
Power Up
As AC power is applied, the controller will perform a series of internal tests to determine if
the electronics are functional. The following tests are performed ;
•
Timer Accuracy. Verify that the internal clock/timing function has not shifted
fundamental frequency.
•
Memory Validity. Verify that all of the embedded processor's internal memory
locations (RAM and ROM) are functional.
•
Power Supply Accuracy. Verify that the logic power supply is within tolerance
•
LED Test. Turn the four LED's on for a short period.
If any of the first three functional tests fail, the controller will revert to the Fault mode (see
Fault Mode section). It will be left to the user to verify that the LED's are functional.
Summary of Contents for Base Powercharger 4x4
Page 1: ...9650 0072 01 Rev E ZOLL Base Powercharger 4x4 Service Manual...
Page 8: ...GENERAL INFORMATION I 7 SEE FILE PG7_C PM5 FOR THIS PAGE AND ALL OF THE SYMBOLS...
Page 11: ...GENERAL INFORMATION I 10...
Page 13: ...CHECKOUT PROCEDURES 9650 0072 II 2 Rev D...
Page 39: ...SCHEMATIC DRAWINGS V 2...
Page 49: ...COMPONENT LAYOUT DRAWINGS VI 2...
Page 53: ...DISASSEMBLY PROCEDURES VII 2...
Page 55: ...DISASSEMBLY PROCEDURES VII 4...
Page 57: ...DISASSEMBLY PROCEDURES VII 6...
Page 58: ...DISASSEMBLY PROCEDURES VII 7...
Page 60: ...DISASSEMBLY PROCEDURES VII 9...
Page 62: ...DISASSEMBLY PROCEDURES VII 11...
Page 63: ...DISASSEMBLY PROCEDURES VII 12...
Page 65: ...DISASSEMBLY PROCEDURES VII 14...
Page 67: ...DISASSEMBLY PROCEDURES VII 16...
Page 71: ...REPLACEMENT PARTS VIII 4...