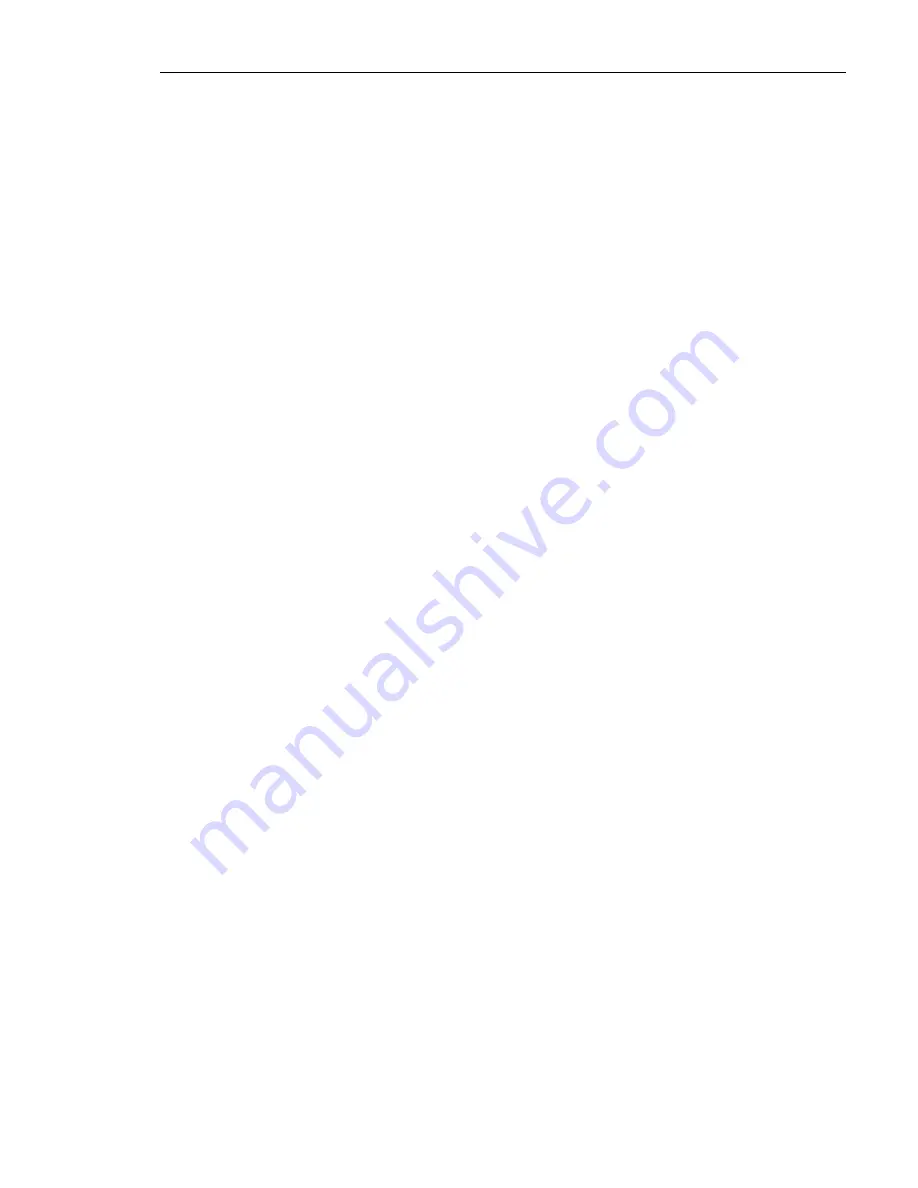
FUNCTIONAL DESCRIPTION
IV-5
Temperature Measurement Circuitry
Temperature measurement circuitry is provided in order to compensate for battery
charge and capacity test variations due to temperature. The signal generated by
voltage divider RT1 and R24 is buffered by amplifier U6B and routed to an A/D input
of each microprocessor through R135, R235, R335, and R435 for isolation. C22 and
C21 provide RF filtering. Since thermistor RT1 has a nominal value of 10K at 25
o
C,
the output voltage at room temperature will be 2.5V (midrange on the microprocessor
A/D). With an 8 bit converter on each microprocessor, the system's internal ambient
temperature can be determined within the range 0 - 70
o
C with 5% accuracy and 1
o
C
resolution.
Temperature compensation is based on ambient, not battery temperature.
Alarm Circuitry
U1A and R1, R2 and Q1 provide the control mechanism for turning the alarm (LS1) on
from the alarm ports located on each compartment microprocessor.
Battery Detection Circuitry
A set of battery detection circuits, comprised of differential amplifiers U5A U5B, U5C
and U5D and associated components, signals each microprocessor if a battery is
installed into its charging compartment. The input signal for each circuit is the battery
sense lead which enters the board, along with the battery positive and negative
terminals, via connector J1. A resistor divider (R13/R14, R15/R16, etc.,.) is used for
each battery detect op amp input to keep the working voltage range within the VCC
supply voltage. Each op amp within U5 is configured as a comparator with a 1.2V
threshold reference presented to the negative input pin.
Diodes D6 through D9 protect each amplifier from static discharge and C9, C11, C15,
and C17 are used as filter capacitors. C10, C12, C14, and C16 are RF filtering
capacitors. Each charging compartment's microprocessor observes its battery
detection signal at port P1.7 (U104.22) with a positive voltage signifying the presence
of a battery.
3. COMPARTMENT CIRCUITRY DESCRIPTION
The following section describes the electronics that are common to all four charger
compartments. A block diagram overview of compartment circuitry is attached. For
simplicity, all part designators will be referenced to the first compartment only. All of
the reference designators for the other three compartments are exact increments of
100 in relation to charging compartment 1's values. The reference designators for the
microprocessor, for example, is U104, U204, U304 and U404 for charging
compartment 1, 2, 3 and 4 respectively. All reference designators below 100 are
associated with common circuitry.
Microprocessor
Each charging compartment contains a microprocessor that controls charging,
discharging and capacity testing of the compartment's battery. The microprocessor
also monitors battery voltage, battery current, system ambient temperature and the
system power supply to determine if any fault condition has occurred. Four status
LED's and a test switch are also controlled by the microprocessor.
Summary of Contents for Base Powercharger 4x4
Page 1: ...9650 0072 01 Rev E ZOLL Base Powercharger 4x4 Service Manual...
Page 8: ...GENERAL INFORMATION I 7 SEE FILE PG7_C PM5 FOR THIS PAGE AND ALL OF THE SYMBOLS...
Page 11: ...GENERAL INFORMATION I 10...
Page 13: ...CHECKOUT PROCEDURES 9650 0072 II 2 Rev D...
Page 39: ...SCHEMATIC DRAWINGS V 2...
Page 49: ...COMPONENT LAYOUT DRAWINGS VI 2...
Page 53: ...DISASSEMBLY PROCEDURES VII 2...
Page 55: ...DISASSEMBLY PROCEDURES VII 4...
Page 57: ...DISASSEMBLY PROCEDURES VII 6...
Page 58: ...DISASSEMBLY PROCEDURES VII 7...
Page 60: ...DISASSEMBLY PROCEDURES VII 9...
Page 62: ...DISASSEMBLY PROCEDURES VII 11...
Page 63: ...DISASSEMBLY PROCEDURES VII 12...
Page 65: ...DISASSEMBLY PROCEDURES VII 14...
Page 67: ...DISASSEMBLY PROCEDURES VII 16...
Page 71: ...REPLACEMENT PARTS VIII 4...