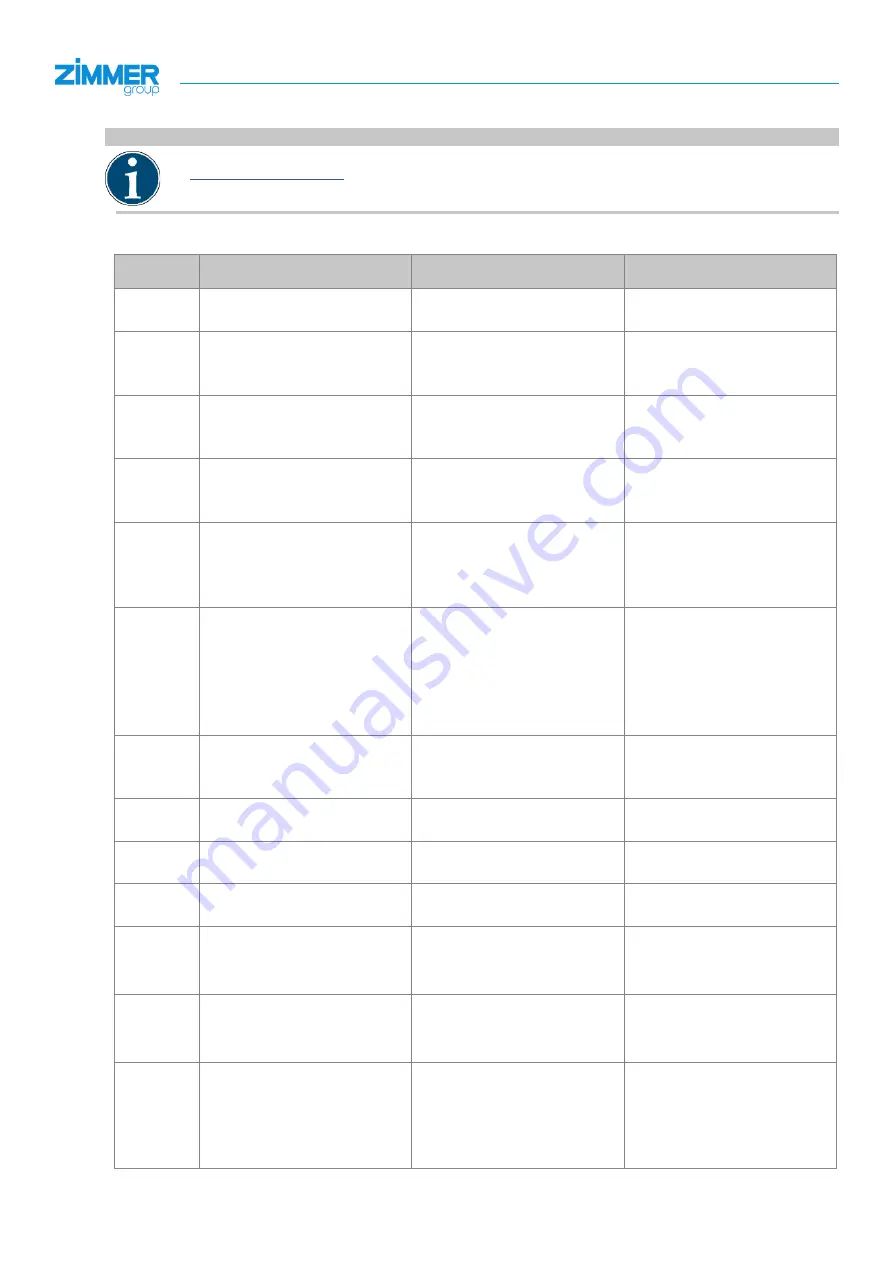
36
DDOC00416 / a
EN / 2020-08-19
Zimmer GmbH
●
Im Salmenkopf 5
●
77866 Rheinau, Germany
●
+49 7844 9138 0
●
+49 7844 9138 80
●
www.zimmer-group.com
INSTALLATION AND OPERATING INSTRUCTIONS:
2-jaw parallel gripper, electric, HRC-01/-02 series
10. Gripping force charts
INFORMATION:
You can find the gripping force charts on the technical data sheet on our website
Ö
www.zimmer-group.com
Zimmer Customer Service is available to provide you with assistance if you have any further questions.
11. Error diagnosis
Error code
Error
Possible cause
Measure
0x0000
No error
-
-
0x0001
Motor is switched off
• Motor was not activated after
power on.
• Motor was switched off.
►
Switch on motor.
►
With "DeviceMode" = 3
0x0002
Gripper performs a reference
run
• Gripper is in a reference run.
►
Wait until the reference run is
complete.
0x0003
System boots up
• The gripper is in the start
sequence.
►
Wait until the start sequence
is complete.
0x0100
Actuator voltage is too low
• The actuator voltage is not
present.
• The applied voltage is too low.
►
Check the applied voltage.
0x0101
Max. permitted temperature
exceeded
• Ambient temperature is too
high.
• Overload of the gripper.
•
Incorrect movement profile
selected.
►Provide sufficient ventilation/
cooling/connection.
►
Check the ease of movement.
►
Choose the selected move-
ment profile.
0x0102
Max. permitted temperature
undershot
• Ambient temperature is too
low.
►Provide a sufficient operating
temperature.
0x0200
IO-Link communication faulty
• -
►
-
0x0201
SPI communication faulty
• -
►
-
0x0202
CAN communication faulty
• -
►
-
0x0204
STO safety circuit interrupted
• The voltage level of the STO
safety circuit is insufficient.
►
Check the connection.
►
Switch on the STO safety
circuit.
0x0300
"ControlWord" not available
• Multiple bits were set in the
"ControlWord."
►
In the "ControlWord," only
one single bit may be set.
►
Check the "ControlWord."
0x0301
Positions not available
• Transmitted positions (Teach,
Base, Shift, WorkPosition) are
incorrect.
•
Modified process data were
not taken over.
►
Check the transmitted pro-
cess data.
►
Apply the process data via a
"Handshake."