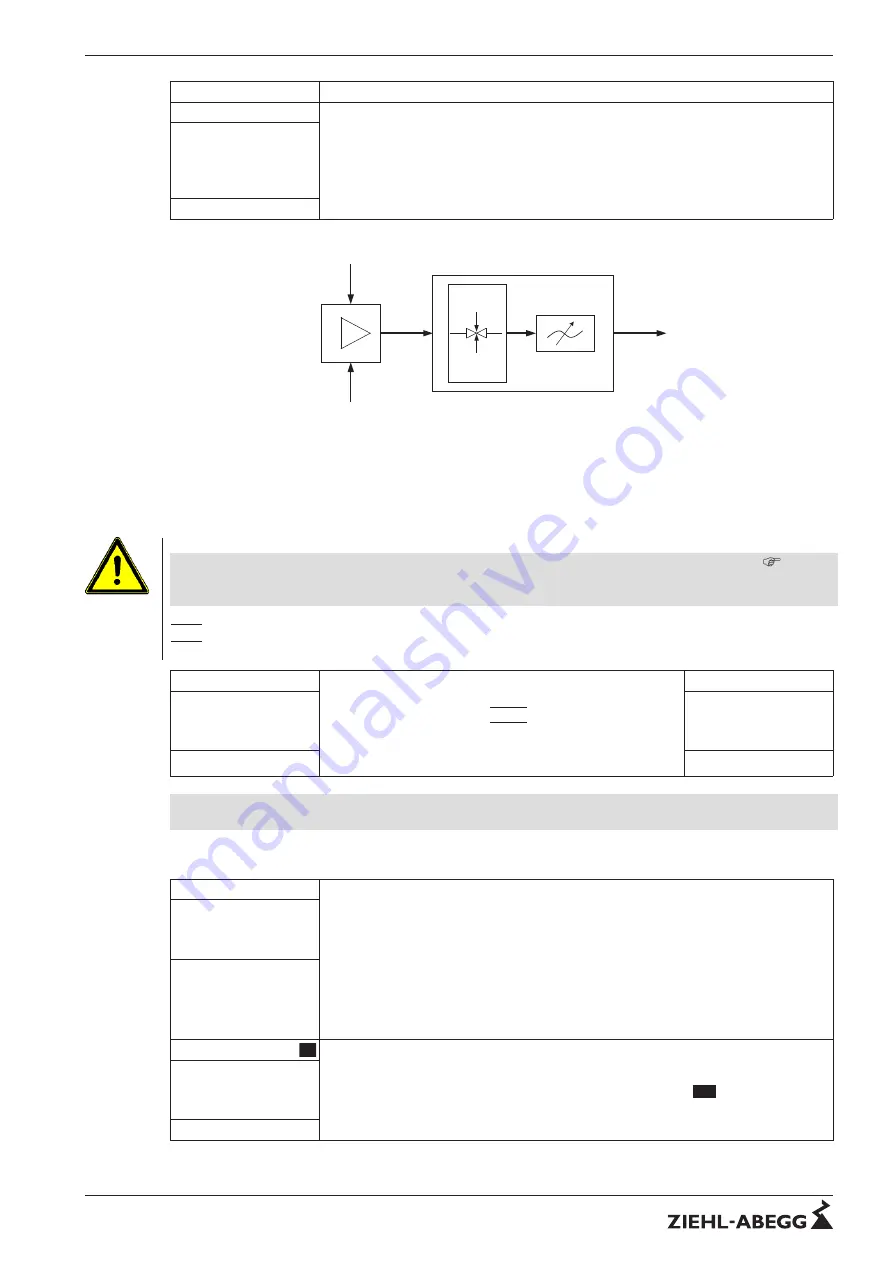
Motor Setup
Rampdown time
Time setting in which the automatic controller output from 100 % to 0 % reduces.
Setting range: 0...250 sec.
Factory setting: 10 / 20 / 30 / 40 sec. (depending on device type)
40 sec
Rampdown time
0 .. 100 %
3
4
1
2
09.05.2007
v_hochlaufzeit_ruecklaufzeit.vsd
1
external Signal
2
Setting
3
Rampup time
4
Rampdown time
9.8.5
Setting Rolling direct.
Attention!
The directionof rotation of the motor must be checked during initial commissioning (
arrow).
We will not under any circumstances provide a guarantee for damage due to incorrect motor
direction of rotation!
When connected in accordance with the connection diagram, the standard rotary direction
“
RIGHT
”
=
|
CW
|
results under factory settings. A change of direction is feasible by exchanging the phase
sequence in the motor connection or through reprogramming.
Motor Setup
Rolling direct.
By selecting the parameter
“
Rotat. Direction
”
the rotation
direction can be changed to
|
CCW
|
for
“
LEFT HAND
”
direc-
tion of rotation.
Pressing the
Enter
key causes the value that has been set to
be accepted.
Motor Setup
CW
Rolling direct.
CCW
Rolling direct.
If the rotary direction is reversed with an available modulation, it is initially reduced to
“
0
”
(discon-
nected) and subsequently increased back to the default value.
9.8.6
Setting Current limit
Motor Setup
Current limit
As an additional safety function the device has a current limit, this can be adapted if
necessary.
The setting refers to the motor rated current of the device (100 % = setting: MotorRa-
tedCurr.).
On exceeding the percentage value set here, the modulation is reduced until the set
current is set again. This prevents overloading of the motor.
Setting range: 100...200 %
Factory setting: 160 %
160 %
Current limit
Info
OL
The active current limit is indicated in the display by the symbol
OL
23.4
°
C
E1 Actual
Operating Instructions
Fcontrol
–
model series FKDM25/32AM-C
Programming
L-BAL-E214-GB 1446 Index 002
Part.-No.
70/99