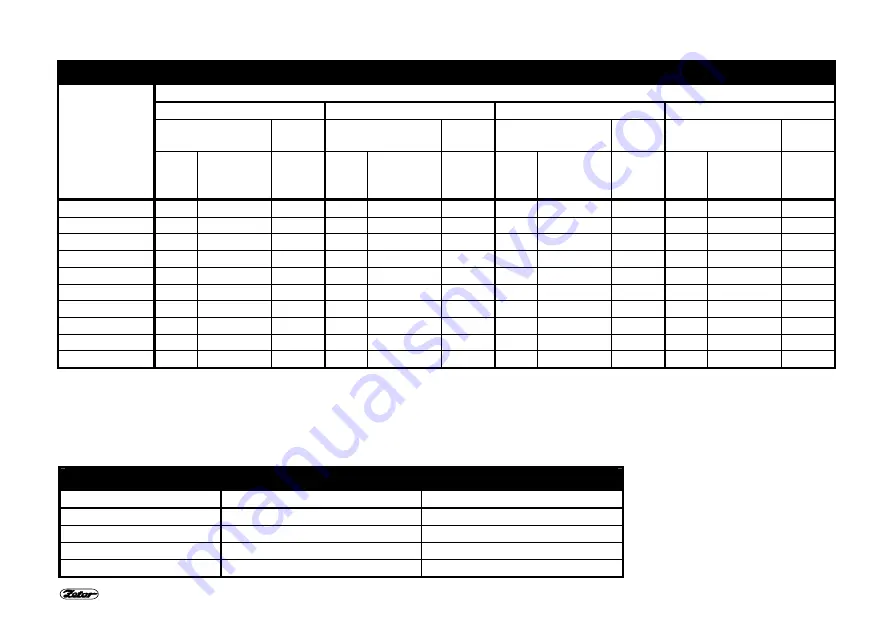
184
MAIN TECHNICAL PARAMETERS
LOAD-BEARING CAPACITIES OF THE REAR TYRES
Travelling speed
40 km.h
-1
30
km.h
-1
20
km.h
-1
8
km.h
-1
Tyre load-bearing
capacity (kg)
Tyre
load-bearing
capacity (kg)
Tyre
load-bearing
capacity (kg)
Tyre
load-bearing
capacity (kg)
Tyre dimen-
sions
Tyre
1 pc
Axle
Infla-
tion
(kPa)
Tyre
1 pc
Axle
Infla-
tion
(kPa)
Tyre
1 pc
Axle
Infla-
tion
(kPa)
Tyre
1 pc
Axle
Infla-
tion
(kPa)
16.9-34
1900
3800 170
2380
4760 170
2750
5500 170
3330
6660 170
16.9R34
2430
4860 160
2600
5200 160
2750
5500 150
3400
6800 150
18.4-34
2050
4100 140
2565
5130 140
2750
5500 120
3400
6800 130
18.4R34
2750
5500 160
2750
5500 160
2750
5500 120
3400
6800 120
16.9-38
2060
4120 170
2575
5150 160
2750
5500 150
3400
6800 160
16.9R38
2575
5150 160
2750
5500 160
2750
5500 130
3400
6800 130
18.4-38
2170
4340 140
2715
5430 140
2750
5500 110
3400
6800 110
18.4R38
2750
5500 140
2750
5500 140
2750
5500 110
3400
6800 120
480/70R38
2750
5500 150
2750
5500 150
2750
5500 110
3400
6800 110
520/70R38
2750 5500 120 2750 5500 120 2750
5500 90 3400 6800 90
The load-bearing capacity values refer to the rear-wheel track of 1725 mm.
Note:
The 480/70R38 tyre is a dimensional equivalent of the 16.9R38 tyre. The 570/70R38 tyre is a dimensional equivalent of the
18.4R38 tyre.
The specified inflation values are minimum valued adapted to the current tyre load so that the tyre deformation can remain in the
range in which all the operation requirements are met.
During operation on a hard base it is suitable with regard to slippage and abrasion of the tyre to increase the pressure by 30 kPa.
CHANGE OF THE LOAD CAPACITY OF THE REAR TYRES (%)
Travelling speed (km/h)
diagonal
radial
8
+ 40
+ 50
20
+ 20
+ 23
30
0 +
7
40
- 20
0
Summary of Contents for FORTERRA 95
Page 1: ......
Page 2: ......
Page 7: ...7 LOCATION OF SERIAL NUMBERS XH154...
Page 32: ...32 ACQUAINTANCE WITH THE TRACTOR B21a...
Page 34: ...34 ACQUAINTANCE WITH THE TRACTOR F54b...
Page 46: ...46 NOTES...
Page 64: ...64 NOTES...
Page 68: ...68 NOTES...
Page 80: ...80 NOTES...
Page 106: ...106 NOTES...
Page 120: ...120 NOTES...
Page 130: ...130 NOTES...
Page 176: ...176 NOTES...
Page 190: ...190 NOTES...
Page 197: ......