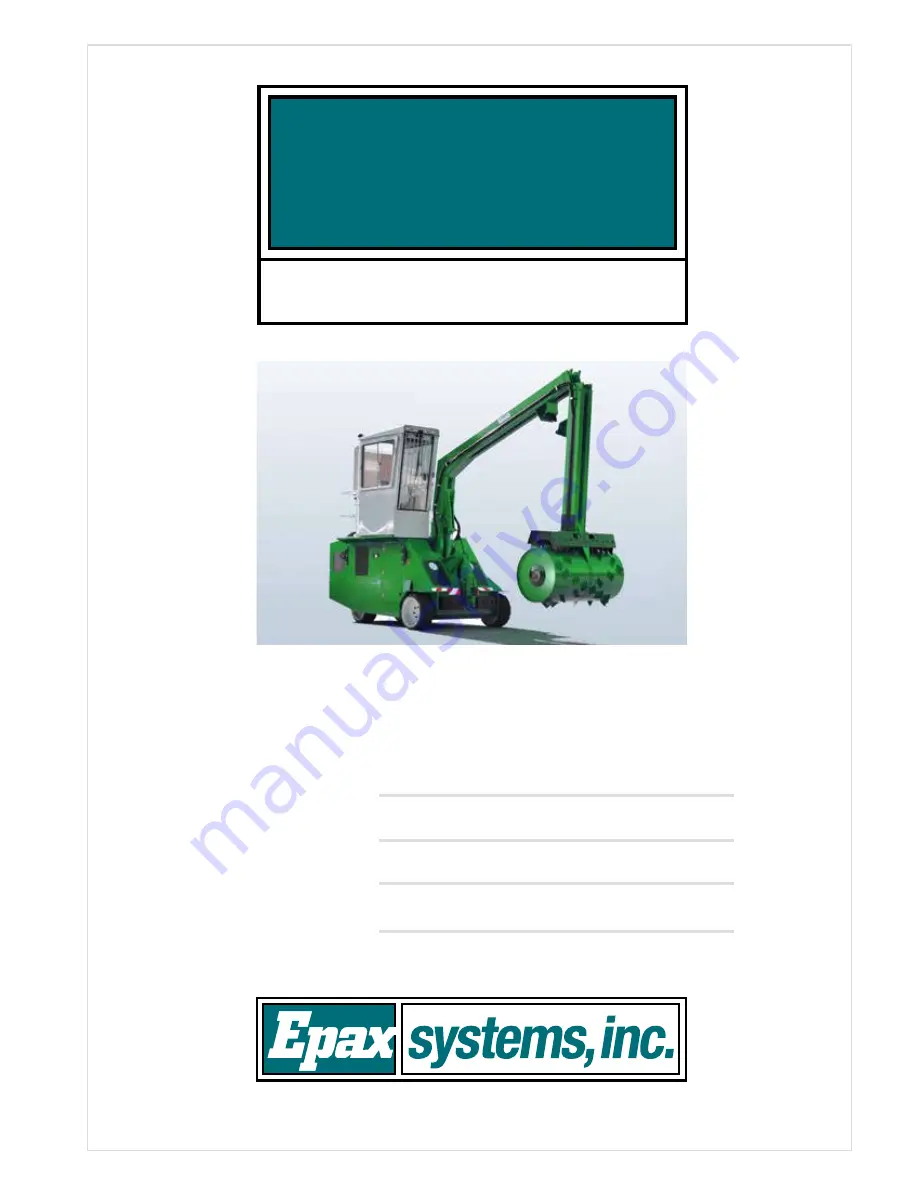
RPM 7700 - VII
174 18
FO-09-39 V
ersion 01
Machine type
Serial no.
Year of manufacture
Operating manual no.
14641 Arminta Street • Panorama City, CA 91402 • Toll Free: 800.220.6776
Telephone: 818.994.2870 • Fax: 818.994.4032 • [email protected] • www.Epaxsystems.com
Original operating manual
Ropax
™
JUMBO MOBILE COMPACTOR
Summary of Contents for ROPAX RPM 7700 VII
Page 63: ...63 11 01 Figure standard design actual design may differ...
Page 76: ......