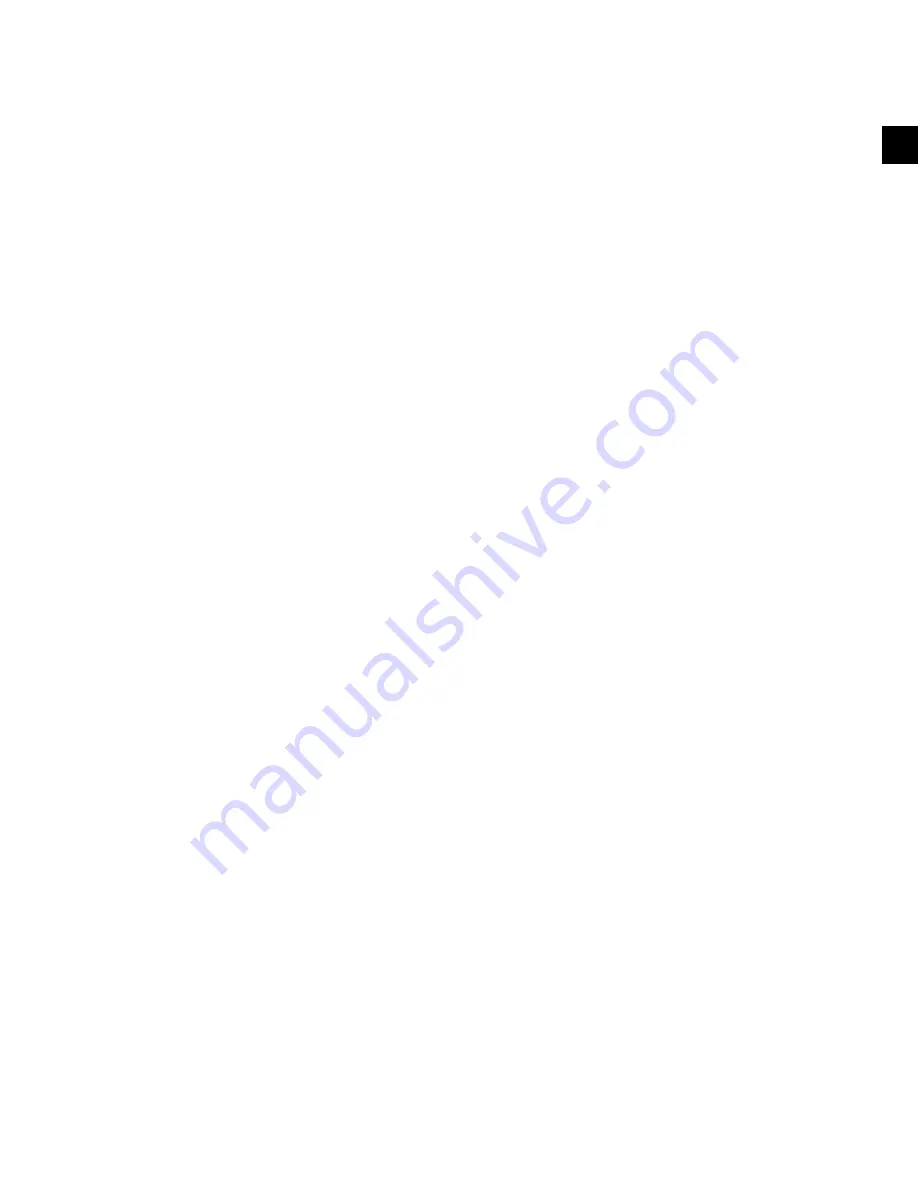
JOHNSON CONTROLS
13
SECTION 1 – GENERAL EQUIPMENT INFORMATION AND SAFETY
FORM 150.73-NM2
ISSUE DATE: 09/07/2020
1
MISUSE OF EQUIPMENT
Suitability for Application
The unit is intended for DX cooling applications and is
not suitable for purposes other than those specified in
these instructions. Any use of the equipment other than
its intended use, or operation of the equipment contrary
to the relevant procedures may result in injury to the
operator, or damage to the equipment.
The unit must not be operated outside the design pa-
rameters specified in this manual.
Structural Support
Structural support of the unit must be provided as in-
dicated in these instructions. Failure to provide proper
support may result in injury to the operator, or damage
to the equipment and/or building.
Mechanical Strength
The unit is not designed to withstand loads or stresses
from adjacent equipment, pipework or structures. Ad-
ditional components must not be mounted on the unit.
Any such extraneous loads may cause structural failure
and may result in injury to the operator, or damage to
the equipment.
General Access
There are a number of areas and features, which may
be a hazard and potentially cause injury when working
on the unit unless suitable safety precautions are taken.
It is important to ensure access to the unit is restricted
to suitably qualified persons who are familiar with the
potential hazards and precautions necessary for safe
operation and maintenance of equipment containing
high temperatures, pressures and voltages.
Pressure Systems
The unit contains refrigerant vapor and liquid under
pressure, release of which can be a danger and cause
injury. The user should ensure that care is taken during
installation, operation and maintenance to avoid dam-
age to the pressure system. No attempt should be made
to gain access to the component parts of the pressure
system other than by suitably trained and qualified per-
sonnel.
Electrical
The unit must be grounded. No installation or main-
tenance work should be attempted on the electrical
equipment without first switching power OFF, isolat-
ing and locking-off the power supply. Servicing and
maintenance on live equipment must only be per-
formed by suitably trained and qualified personnel. No
attempt should be made to gain access to the control
panel or electrical enclosures during normal operation
of the unit.
Rotating Parts
Fan guards must be fitted at all times and not removed
unless the power supply has been isolated. If ductwork
is to be fitted, requiring the wire fan guards to be re-
moved, alternative safety measures must be taken to
protect against the risk of injury from rotating fans.
Sharp Edges
The fins on the air-cooled condenser coils have sharp
metal edges. Reasonable care should be taken when
working in contact with the coils to avoid the risk of
minor abrasions and lacerations. The use of gloves is
recommended.
Frame rails, brakes, and other components may also
have sharp edges. Reasonable care should be taken
when working in contact with any components to avoid
risk of minor abrasions and lacerations.
Refrigerants and Oils
Refrigerants and oils used in the unit are generally non-
toxic, non-flammable and non-corrosive, and pose no
special safety hazards. Use of gloves and safety glasses
is, however, recommended when working on the unit.
The build up of refrigerant vapor, from a leak for ex-
ample, does pose a risk of asphyxiation in confined or
enclosed spaces and attention should be given to good
ventilation.
High Temperature and Pressure Cleaning
High temperature and pressure cleaning methods
(e.g. steam cleaning) should not be used on any part
of the pressure system as this may cause operation of
the pressure relief device(s). Detergents and solvents,
which may cause corrosion, should also be avoided.
Emergency Shutdown
In case of emergency, the control panel is fitted with a
Unit Switch to stop the unit in an emergency. When op-
erated, it removes the low voltage 120 VAC electrical
supply from the inverter system, thus shutting down
the unit.
Summary of Contents for YLUA0248 Series
Page 4: ...JOHNSON CONTROLS 4 FORM 150 73 NM2 ISSUE DATE 09 07 2020 THIS PAGE INTENTIONALLY LEFT BLANK ...
Page 10: ...JOHNSON CONTROLS 10 FORM 150 73 NM2 ISSUE DATE 09 07 2020 THIS PAGE INTENTIONALLY LEFT BLANK ...
Page 14: ...JOHNSON CONTROLS 14 FORM 150 73 NM2 ISSUE DATE 09 07 2020 THIS PAGE INTENTIONALLY LEFT BLANK ...
Page 30: ...JOHNSON CONTROLS 30 FORM 150 73 NM2 ISSUE DATE 09 07 2020 THIS PAGE INTENTIONALLY LEFT BLANK ...
Page 44: ...JOHNSON CONTROLS 44 FORM 150 73 NM2 ISSUE DATE 09 07 2020 THIS PAGE INTENTIONALLY LEFT BLANK ...
Page 55: ...JOHNSON CONTROLS 55 SECTION 5 TECHNICAL DATA FORM 150 73 NM2 ISSUE DATE 09 07 2020 5 5 ...
Page 57: ...JOHNSON CONTROLS 57 SECTION 5 TECHNICAL DATA FORM 150 73 NM2 ISSUE DATE 09 07 2020 5 5 ...
Page 59: ...JOHNSON CONTROLS 59 SECTION 5 TECHNICAL DATA FORM 150 73 NM2 ISSUE DATE 09 07 2020 5 5 ...
Page 61: ...JOHNSON CONTROLS 61 SECTION 5 TECHNICAL DATA FORM 150 73 NM2 ISSUE DATE 09 07 2020 5 5 ...
Page 63: ...JOHNSON CONTROLS 63 SECTION 5 TECHNICAL DATA FORM 150 73 NM2 ISSUE DATE 09 07 2020 5 5 ...
Page 67: ...JOHNSON CONTROLS 67 SECTION 5 TECHNICAL DATA FORM 150 73 NM2 ISSUE DATE 09 07 2020 5 5 ...
Page 73: ...JOHNSON CONTROLS 73 SECTION 5 TECHNICAL DATA FORM 150 73 NM2 ISSUE DATE 09 07 2020 5 5 ...
Page 77: ...JOHNSON CONTROLS 77 SECTION 5 TECHNICAL DATA FORM 150 73 NM2 ISSUE DATE 09 07 2020 5 5 ...
Page 94: ...JOHNSON CONTROLS 94 FORM 150 73 NM2 ISSUE DATE 09 07 2020 THIS PAGE INTENTIONALLY LEFT BLANK ...
Page 124: ...JOHNSON CONTROLS 124 FORM 150 73 NM2 ISSUE DATE 09 07 2020 THIS PAGE INTENTIONALLY LEFT BLANK ...