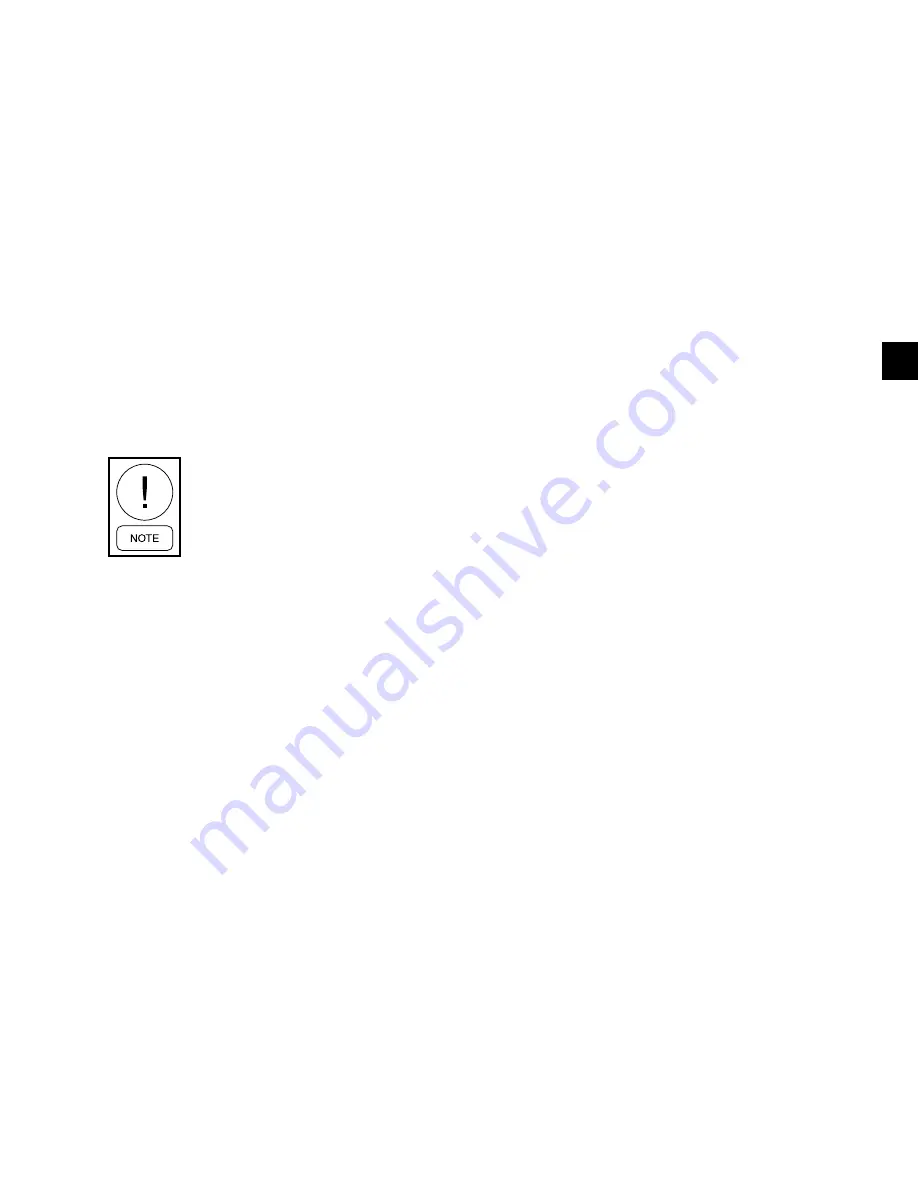
JOHNSON CONTROLS
35
SECTION 4 – INSTALLATION
FORM 150.73-NM2
ISSUE DATE: 09/07/2020
4
Copper power wiring only should be used for supply-
ing power to the unit. This is recommended to avoid
safety and reliability issues resulting from connection
failure at the power connections to the unit. Aluminum
wiring is not recommended due to thermal character-
istics that may cause loose terminations resulting from
the contraction and expansion of the wiring. Alumi-
num oxide may also build up at the termination causing
hot spots and eventual failure. If aluminum wiring is
used to supply power to the unit, AL-CU compression
fittings should be used to transition from aluminum to
copper. This transition should be done in an external
box separate to the power panel. Copper conductors
can then be run from the box to the unit.
A 120-1-60, 15 amp source must be supplied for the
control panel through a fused disconnect when a con-
trol panel transformer (optional) is not provided
(Refer
to Fig. 7).
See unit wiring diagrams for field and
power wiring connections, chilled water
pump starter contacts, alarm contacts,
compressor run status contacts, PWM
input, and load limit input. Refer to sec-
tion on UNIT OPERATION for a detailed
description of operation concerning
aforementioned contacts and inputs.
COMPRESSOR HEATERS
Compressor heaters are standard. ZP103, ZP120 &
ZP137 compressors utilize 90W heaters; ZP180 com-
pressors utilize 70W heaters; ZP235 compressors uti-
lize 120W heaters. If power is OFF more than two
hours, the crankcase heaters must be energized for 18
– 24 hours prior to restarting a compressor. This will
assure that liquid slugging and oil dilution does not
damage the compressors on start.
RELIEF VALVES
Relief valves are located on both the high and low
pressure side of the piping. High side relief valve pres-
sure setting is 650 PSIG. Low side relief valve pressure
setting is 450 PSIG.
HIGH PRESSURE CUTOUT
A high pressure cutout is installed in the discharge pip-
ing of each system. The cutout opens at 585 PSIG ± 10
PSIG and closes at 440 PSIG ± 25 PSIG.
ELECTRICAL WIRING
Field Wiring
Power wiring must be provided through a fused dis-
connect switch to the unit terminals (or optional mold-
ed disconnect switch) in accordance with N.E.C. or
local code requirements. Minimum circuit ampacity
and maximum dual element fuse size are given in the
tables.
A 120-1-60, 15 amp source must be supplied for the
control panel through a fused disconnect when a con-
trol panel transformer (optional) is not provided.
See
Figure 3 on page 21 and Figure 10 on page 43.
See Figure 2 on page 20 and Figure 10 on page 43
and unit wiring diagrams for field and power wiring
connections. See SECTION 8 – UNIT OPERATION
for a detailed description of operation concerning unit
contacts and inputs.
Liquid Line Solenoid Connections
The field supplied and installed liquid line solenoid
valves should be installed at the evaporator and wired
using 18 AWG minimum wire. Electrical connections
should be made at Terminal Board CTB3. CTB3 is lo-
cated in the power panel on the left side of the power
panel.
Note that power for the solenoid coil is 120
vac
Figure 10 on page 43 and unit wiring dia-
gram.
Discharge Air Sensor
The discharge air sensor and associated connector
hardware is factory supplied but must be field installed.
Field wire must be field supplied (QUABBIN 930421-
2 or equivalent 2 conductor with shield and drain wire
- 20 AWG 300 V 60°C - polyethylene insulation UV
resistant). Field wiring is connected to pins 3, 6, and
9 of J6 on the microboard. See
and unit wiring diagram.
Zone Thermostats (Remote Start/Stop)
Field supplied thermostats or dry contacts
must be
field wired when operating the unit in Suction Pres-
sure Control Mode
.
The System 1 zone thermostat is
field wired at XTBC1 terminals 13 to 50. On two sys-
tem units, System 2 zone thermostat is field wired to
XTBC1 terminals 13 to 51. XTBC 1 terminal is located
near the bottom of the micro control panel. See
Summary of Contents for YLUA0248 Series
Page 4: ...JOHNSON CONTROLS 4 FORM 150 73 NM2 ISSUE DATE 09 07 2020 THIS PAGE INTENTIONALLY LEFT BLANK ...
Page 10: ...JOHNSON CONTROLS 10 FORM 150 73 NM2 ISSUE DATE 09 07 2020 THIS PAGE INTENTIONALLY LEFT BLANK ...
Page 14: ...JOHNSON CONTROLS 14 FORM 150 73 NM2 ISSUE DATE 09 07 2020 THIS PAGE INTENTIONALLY LEFT BLANK ...
Page 30: ...JOHNSON CONTROLS 30 FORM 150 73 NM2 ISSUE DATE 09 07 2020 THIS PAGE INTENTIONALLY LEFT BLANK ...
Page 44: ...JOHNSON CONTROLS 44 FORM 150 73 NM2 ISSUE DATE 09 07 2020 THIS PAGE INTENTIONALLY LEFT BLANK ...
Page 55: ...JOHNSON CONTROLS 55 SECTION 5 TECHNICAL DATA FORM 150 73 NM2 ISSUE DATE 09 07 2020 5 5 ...
Page 57: ...JOHNSON CONTROLS 57 SECTION 5 TECHNICAL DATA FORM 150 73 NM2 ISSUE DATE 09 07 2020 5 5 ...
Page 59: ...JOHNSON CONTROLS 59 SECTION 5 TECHNICAL DATA FORM 150 73 NM2 ISSUE DATE 09 07 2020 5 5 ...
Page 61: ...JOHNSON CONTROLS 61 SECTION 5 TECHNICAL DATA FORM 150 73 NM2 ISSUE DATE 09 07 2020 5 5 ...
Page 63: ...JOHNSON CONTROLS 63 SECTION 5 TECHNICAL DATA FORM 150 73 NM2 ISSUE DATE 09 07 2020 5 5 ...
Page 67: ...JOHNSON CONTROLS 67 SECTION 5 TECHNICAL DATA FORM 150 73 NM2 ISSUE DATE 09 07 2020 5 5 ...
Page 73: ...JOHNSON CONTROLS 73 SECTION 5 TECHNICAL DATA FORM 150 73 NM2 ISSUE DATE 09 07 2020 5 5 ...
Page 77: ...JOHNSON CONTROLS 77 SECTION 5 TECHNICAL DATA FORM 150 73 NM2 ISSUE DATE 09 07 2020 5 5 ...
Page 94: ...JOHNSON CONTROLS 94 FORM 150 73 NM2 ISSUE DATE 09 07 2020 THIS PAGE INTENTIONALLY LEFT BLANK ...
Page 124: ...JOHNSON CONTROLS 124 FORM 150 73 NM2 ISSUE DATE 09 07 2020 THIS PAGE INTENTIONALLY LEFT BLANK ...