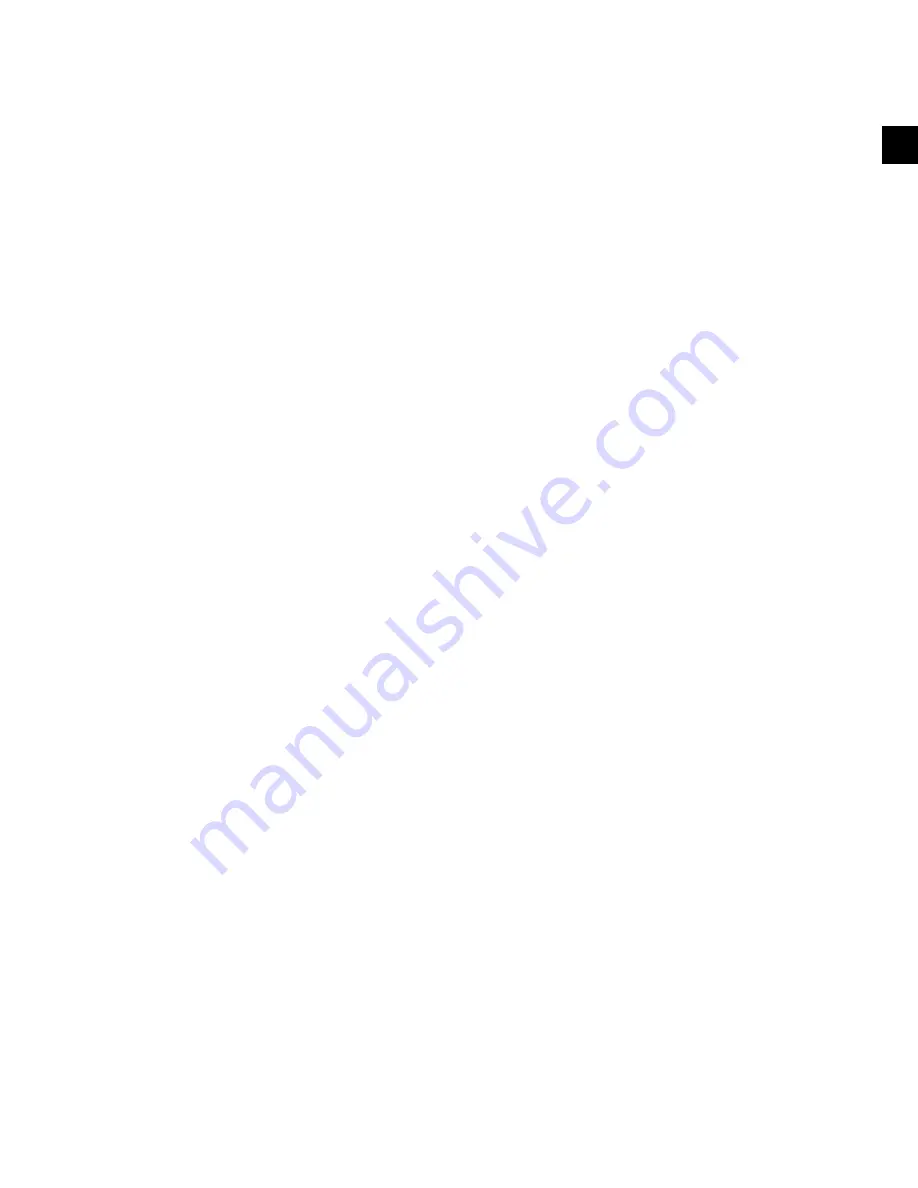
JOHNSON CONTROLS
11
FORM 150.73-NM2
ISSUE DATE: 09/07/2020
1
INTRODUCTION
The 70-130 Ton (245 - 475 kW) YLUA Condensing
Unit Models are shipped complete from the factory
ready for field installation.
The unit is pressure-tested, evacuated and given a ni-
trogen holding charge and includes an initial oil charge
(R-410A refrigerant supplied by others). After assem-
bly, an operational test is performed to assure that each
control device operates correctly.
The unit structure is heavy-gauge, galvanized steel.
This galvanized steel is coated with baked-on powder
paint, which, when subjected to ASTM B117 1000
hour, salt spray testing, yields a minimum ASTM 1654
rating of “6”. Units are designed in accordance with
NFPA 70 (National Elec tric Code), ASHRAE/ANSI 15
Safety code for mechanical refrigeration, and are cETL
listed. All units are produced at an ISO 9000-registered
facility.
COMPRESSORS
The condensing unit has suction-gas cooled, hermet-
ic, scroll com pressors. The compressors incorporate
a compliant scroll design in both the axial and radial
direction. All rotating parts of the compressors are
statically and dynamically balanced. A large internal
volume and oil reservoir pro vides greater liquid toler-
ance. Compressor crankcase heaters are also included
for extra protection against liquid migration.
CONDENSER
Coils
– Fin and tube condenser coils of seamless, inter-
nally-enhanced, high-condensing-coefficient, corro-
sion resistant copper tubes are arranged in staggered
rows, mechanically expanded into aluminum fins. Inte-
gral subcooling is included. The design working pres-
sure of the coil is 650 psig (45 barg).
Fans
– The condenser fans are composed of corro-
sion-resistant aluminum hub and glass-fiber-reinforced
polypropylene composite blades molded into a low
noise airfoil section. They are designed for maximum
efficiency and are statically and dynamically balanced
for vibration free operation. They are directly driven by
independent motors, and positioned for vertical air dis-
charge. The fan guards are constructed of heavy-gauge,
rust-resistant, coated steel. All blades are statically and
dynamically balanced for vibration-free operation.
Motors
– The fan motors are Totally Enclosed Air-
Over, squirrel-cage type, current protected. They fea-
ture ball bearings that are double-sealed and perma-
nently lubri cated.
REFRIGERANT CIRCUIT
Two inde pendent refrigerant circuits will be furnished
on each unit. All unit piping will be copper, with brazed
joints. The liquid line will include a field connection
shutoff valve with charg ing port located on each con-
denser circuit. Suction line connections are provided
on each refrigeration circuit. A filter drier and sight
glass are shipped loose for field installation on each
refrigerant circuit.
All expansion valves, liquid line solenoid valves,
refriger ant, and refrigerant field piping are supplied by
others.
WARRANTY
Johnson Controls warrants all equipment and materials
against defects in workmanship and materials for a pe-
riod of eighteen months from date of shipment, unless
labor or extended warranty has been purchased as part
of the contract.
The warranty is limited to parts only replacement and
shipping of any faulty part, or sub-assembly, which has
failed due to poor quality or manufacturing errors. All
claims must be supported by evidence that the failure
has occurred within the warranty period, and that the
unit has been operated within the designed parameters
specified.
All warranty claims must specify the unit model, serial
number, order number and run hours/starts. Model and
serial number information is printed on the unit identi-
fication plate.
The unit warranty will be void if any modification to
the unit is carried out without prior written approval
from Johnson Controls.
For warranty purposes, the following conditions must
be satisfied:
• The initial start of the unit must be carried out by
trained personnel from an Authorized Johnson
Controls Service Center
(see Commissioning on
SECTION 1 – GENERAL EQUIPMENT INFORMATION AND SAFETY
Summary of Contents for YLUA0248 Series
Page 4: ...JOHNSON CONTROLS 4 FORM 150 73 NM2 ISSUE DATE 09 07 2020 THIS PAGE INTENTIONALLY LEFT BLANK ...
Page 10: ...JOHNSON CONTROLS 10 FORM 150 73 NM2 ISSUE DATE 09 07 2020 THIS PAGE INTENTIONALLY LEFT BLANK ...
Page 14: ...JOHNSON CONTROLS 14 FORM 150 73 NM2 ISSUE DATE 09 07 2020 THIS PAGE INTENTIONALLY LEFT BLANK ...
Page 30: ...JOHNSON CONTROLS 30 FORM 150 73 NM2 ISSUE DATE 09 07 2020 THIS PAGE INTENTIONALLY LEFT BLANK ...
Page 44: ...JOHNSON CONTROLS 44 FORM 150 73 NM2 ISSUE DATE 09 07 2020 THIS PAGE INTENTIONALLY LEFT BLANK ...
Page 55: ...JOHNSON CONTROLS 55 SECTION 5 TECHNICAL DATA FORM 150 73 NM2 ISSUE DATE 09 07 2020 5 5 ...
Page 57: ...JOHNSON CONTROLS 57 SECTION 5 TECHNICAL DATA FORM 150 73 NM2 ISSUE DATE 09 07 2020 5 5 ...
Page 59: ...JOHNSON CONTROLS 59 SECTION 5 TECHNICAL DATA FORM 150 73 NM2 ISSUE DATE 09 07 2020 5 5 ...
Page 61: ...JOHNSON CONTROLS 61 SECTION 5 TECHNICAL DATA FORM 150 73 NM2 ISSUE DATE 09 07 2020 5 5 ...
Page 63: ...JOHNSON CONTROLS 63 SECTION 5 TECHNICAL DATA FORM 150 73 NM2 ISSUE DATE 09 07 2020 5 5 ...
Page 67: ...JOHNSON CONTROLS 67 SECTION 5 TECHNICAL DATA FORM 150 73 NM2 ISSUE DATE 09 07 2020 5 5 ...
Page 73: ...JOHNSON CONTROLS 73 SECTION 5 TECHNICAL DATA FORM 150 73 NM2 ISSUE DATE 09 07 2020 5 5 ...
Page 77: ...JOHNSON CONTROLS 77 SECTION 5 TECHNICAL DATA FORM 150 73 NM2 ISSUE DATE 09 07 2020 5 5 ...
Page 94: ...JOHNSON CONTROLS 94 FORM 150 73 NM2 ISSUE DATE 09 07 2020 THIS PAGE INTENTIONALLY LEFT BLANK ...
Page 124: ...JOHNSON CONTROLS 124 FORM 150 73 NM2 ISSUE DATE 09 07 2020 THIS PAGE INTENTIONALLY LEFT BLANK ...