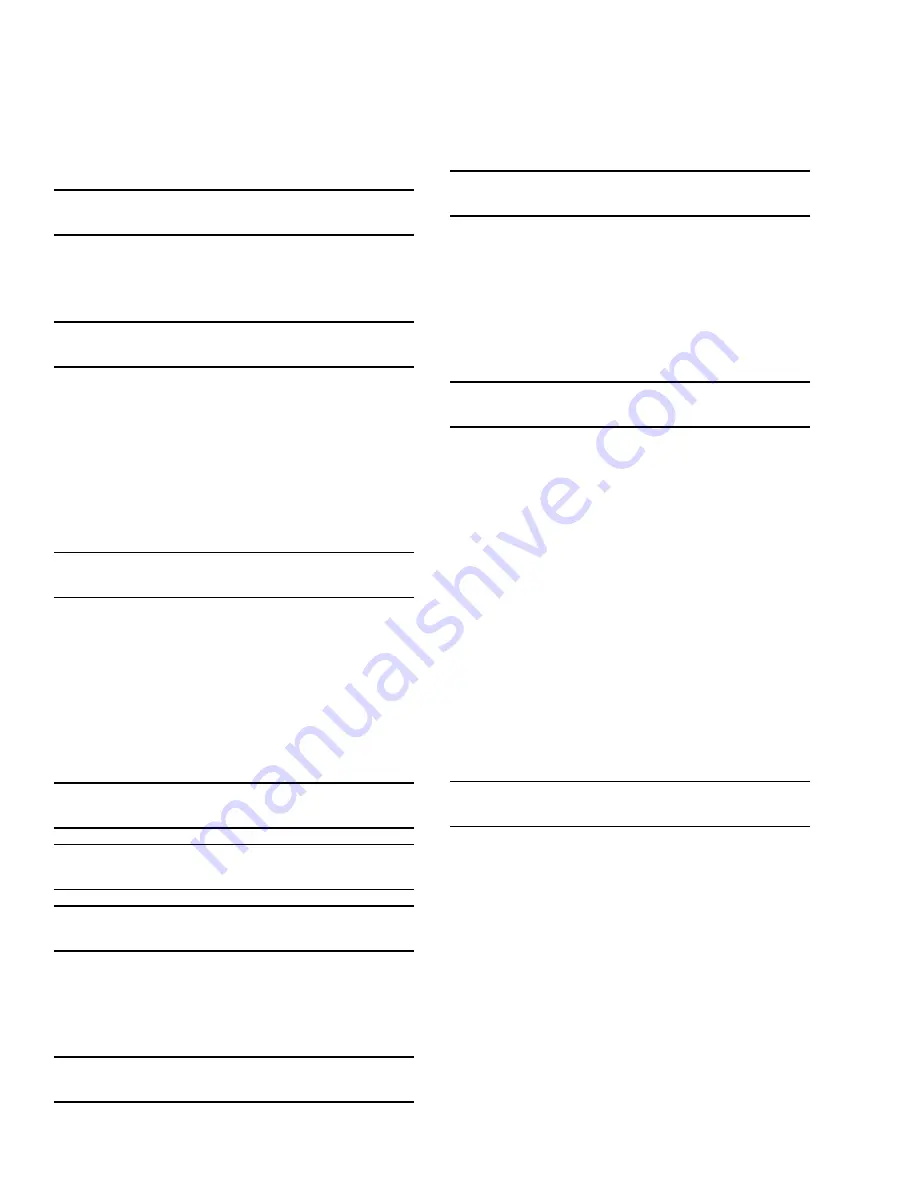
32
JOHNSON CONTROLS
FORM 150.68-ICOM1
ISSUE DATE: 10/15/2020
Units without a hydro kit. The flow switch –XTBC1
terminals 13 & 14 is open and the unit will not run or if
running, stops. A stop due to the flow switch opening is
recorded in history as a UNIT FAULT: FLOW SWITCH
OPEN, but no remote alarm is given.
SYS X SYS SWITCH OFF
The system switch under OPTIONS is turned off. The
system will not be allowed to run until the switch is
turned back on.
SYS X NO COOL LOAD
This message applies to the cooling mode only. The
chilled liquid temperature is below the point (determined
by the SETPOINT and RANGE) that the microprocessor
will bring on a system or that the microprocessor has
not loaded the lead system far enough into the loading
sequence to be ready to bring the lag system on. The
lag system will display this message until the loading
sequence is ready for the lag system to start.
SYS X NO HEAT LOAD
This message applies to the heating mode only. The hot
liquid temperature is above the point (determined by
the SETPOINT and RANGE) that the microprocessor
will bring on a system or that the microprocessor has
not loaded the lead system far enough into the loading
sequence to be ready to bring the lag system on. The
lag system will display this message until the loading
sequence is ready for the lag system to start.
SYS X COOLING RUN X
SYS X HEATING RUN X
SYS X DEFROST RUN X
Indicates that the respective system is running in cooling,
or heating or defrost due to demand. The X will be
replaced with the number of compressors in that system
that are running.
SYS X AR TIMER XXX S
Shows the amount of time left on the respective systems
anti-recycle timer. This message is displayed when the
system is unable to start due to the anti-recycle timer
being active.
SYS X AC TIMER XX S
The anti-coincident timer is a software feature that
guards against 2 systems starting simultaneously.
This assures instantaneous starting current does not
become excessively high due to simultaneous starts.
The microprocessor limits the time between compressor
starts to 1 minute regardless of demand or the anti-
recycle timer being timed out.
SYS X DSCH LIMITING
Discharge pressure limiting is in effect. The limiting
pressure is a factory set limit to keep the system from
faulting on the high discharge pressure cutout due to high
load or pull down conditions. When the unload point is
reached, the microprocessor will automatically unload
the affected system by de-energizing one compressor.
The discharge pressure unload will occur when
the discharge pressure gets within 10 psig of the
programmed discharge pressure cutout. This will only
happen if the system is fully loaded and will shut only
one compressor off. Discharge limiting will prevent the
last compressor in a system from starting if the discharge
pressure is above 85% of the programmed discharge
pressure cutout. Reloading the affected system will occur
when the discharge pressure drops to 85% of the unload
pressure and 10 minutes have elapsed.
SYS X SUCT LIMITING
Suction pressure limiting is in effect. The suction
pressure limit is a control point that limits the loading
of the lag compressor in a system when the suction
pressure drops to within 15% (cooling) 20% (heating)
above the suction pressure cutout. In heating/defrost
modes the actual suction pressure cut-out value is used.
(Refer to Fault Status Messages Section for details of
actual suction pressure value calculation from discharge
pressure).The system will be allowed to load after 60
seconds and after the suction pressure rises above the
suction pressure limit point.
Summary of Contents for YLPA 0115SE
Page 4: ...4 JOHNSON CONTROLS FORM 150 68 ICOM1 ISSUE DATE 10 15 2020 Page Left Intentionally Blank ...
Page 10: ...10 JOHNSON CONTROLS FORM 150 68 ICOM1 ISSUE DATE 10 15 2020 Page Left Intentionally Blank ...
Page 16: ...16 JOHNSON CONTROLS FORM 150 68 ICOM1 ISSUE DATE 10 15 2020 Page Left Intentionally Blank ...
Page 26: ...26 JOHNSON CONTROLS FORM 150 68 ICOM1 ISSUE DATE 10 15 2020 Page Left Intentionally Blank ...
Page 30: ...30 JOHNSON CONTROLS FORM 150 68 ICOM1 ISSUE DATE 10 15 2020 Page Left Intentionally Blank ...
Page 72: ...72 JOHNSON CONTROLS FORM 150 68 ICOM1 ISSUE DATE 10 15 2020 Page Left Intentionally Blank ...
Page 79: ...79 JOHNSON CONTROLS FORM 150 68 ICOM1 ISSUE DATE 10 15 2020 YLPA P I Diagram ...
Page 86: ...86 JOHNSON CONTROLS FORM 150 68 ICOM1 ISSUE DATE 10 15 2020 Page Left Intentionally Blank ...
Page 88: ...88 JOHNSON CONTROLS FORM 150 68 ICOM1 ISSUE DATE 10 15 2020 Page Left Intentionally Blank ...