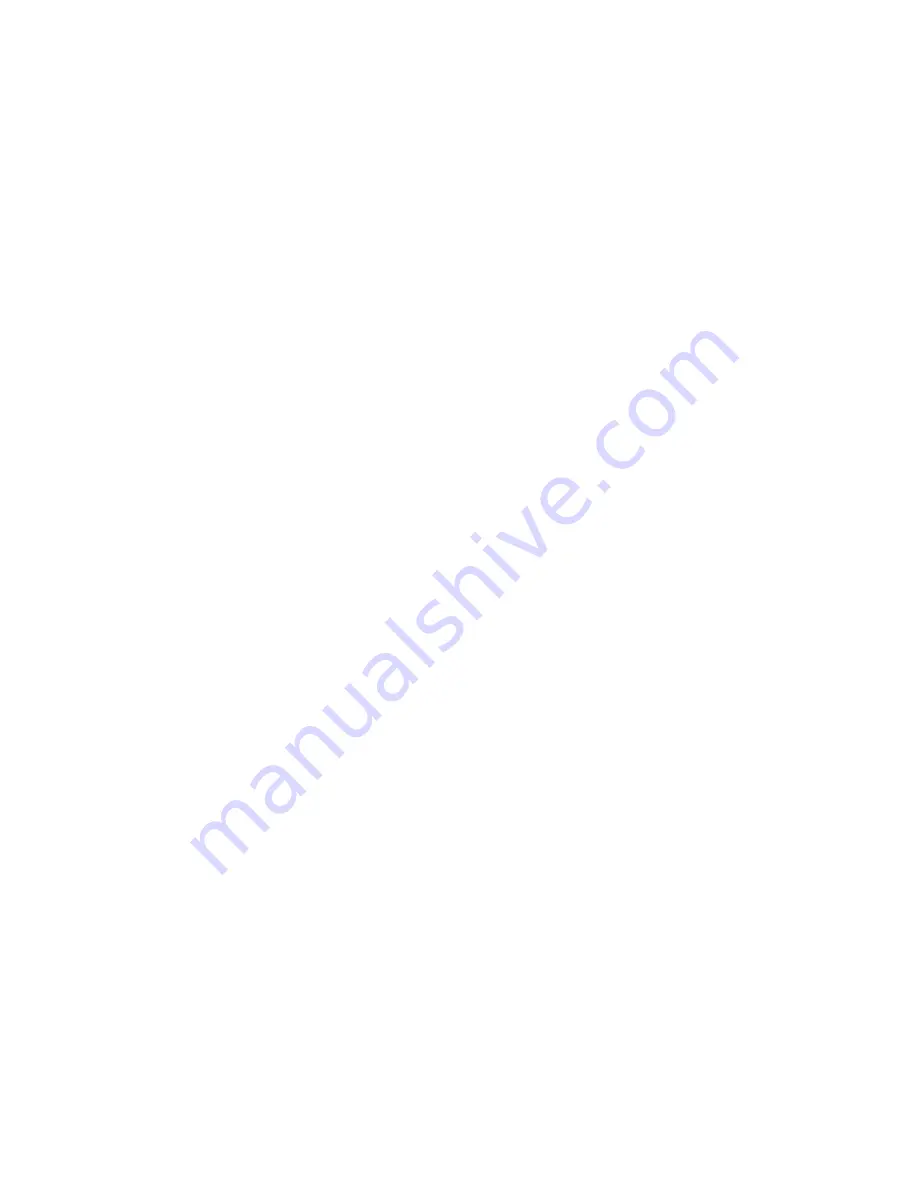
21
JOHNSON CONTROLS
FORM 150.68-ICOM1
ISSUE DATE: 10/15/2020
The heat exchanger(s) must not be exposed to flushing
velocities or debris released during flushing. It is
recommended that a suitably sized bypass and valve
arrangement be installed to allow flushing of the
pipework system. The bypass can be used during
maintenance to isolate the heat exchanger(s) without
disrupting flow to other units.
Thermometer and pressure gauge connections should
be provided on the inlet and outlet connections of each
heat exchanger.
Drain and air vent connections should be provided at all
low and high points in the pipework to permit drainage
of the system, and to vent any air in the pipes.
Liquid systems at risk of freezing, due to low ambient
temperatures, should be protected using insulation and
heater tape and/or a suitable glycol solution. The liquid
pumps must also be used to ensure liquid is circulated
when the ambient temperature approaches freezing
point. Insulation should also be installed around the heat
exchanger nozzles.
Heater tape under the insulation is recommended,
supplied independently and controlled by an ambient
temperature thermostat set to switch on at approximately
4ºF above the freezing temperature of the chilled liquid.
The heat exchanger is protected by a heater mat placed
under the insulation, which are powered from the unit
control system power supply. During cold weather when
there is a risk of freezing, chiller power should be left
switched ON to provide the freeze protection function
unless the liquid systems have been drained.
PIPEWORK ARRANGEMENT
The following are suggested pipework arrangements for
single unit installations. For multiple unit installations,
each unit should be piped as shown. These are
recommendations of the Building Services Research
Association.
INSTALLATION OF VIBRATION ISOLATORS
An optional set of vibration isolators can be supplied
loose with each unit.
PIPEWORK CONNECTION
The following piping recommendations are intended
to ensure satisfactory operation of the unit. Failure to
follow these recommendations could cause damage
to the unit, or loss of performance, and may void the
warranty.
A flow switch must be installed in the customer pipework
at the outlet of the heat exchanger as shown in the
arrangement diagrams, and wired back to the control
panel using screened cable. This is to prevent damage to
the heat exchanger caused by inadequate liquid flow. To
prevent turbulent flow, there must be straight pipework
either side of the flow switch equal in length to at least
5 times the diameter of the pipe.
The flow switches used must have gold plated contacts
for low voltage/current operation.
Alternatively, a differential pressure switch fitted across
an orifice plate may be used, preferably of the high/low
limit type.
The liquid pumps installed in the pipework systems
should discharge directly into the unit heat exchanger
sections of the system. The pumps require an auto-starter
(by others) to be wired to the control panel.
Pipework and fittings must be separately supported to
prevent any loading on the heat exchanger(s). Flexible
connections are recommended which will also minimize
transmission of vibrations to the building. Flexible
connections must be used if the unit is mounted on anti-
vibration mounts as some movement of the unit can be
expected in normal operation.
Pipework and fittings directly next to the heat
exchanger(s) should be readily demountable to allow
for cleaning prior to operation, and to facilitate visual
inspection of the exchanger nozzles.
Each heat exchanger must be protected by a strainer,
preferably of 20 mesh, fitted as close as possible to the
liquid inlet connection, and provided with a means of
local isolation.
Summary of Contents for YLPA 0115SE
Page 4: ...4 JOHNSON CONTROLS FORM 150 68 ICOM1 ISSUE DATE 10 15 2020 Page Left Intentionally Blank ...
Page 10: ...10 JOHNSON CONTROLS FORM 150 68 ICOM1 ISSUE DATE 10 15 2020 Page Left Intentionally Blank ...
Page 16: ...16 JOHNSON CONTROLS FORM 150 68 ICOM1 ISSUE DATE 10 15 2020 Page Left Intentionally Blank ...
Page 26: ...26 JOHNSON CONTROLS FORM 150 68 ICOM1 ISSUE DATE 10 15 2020 Page Left Intentionally Blank ...
Page 30: ...30 JOHNSON CONTROLS FORM 150 68 ICOM1 ISSUE DATE 10 15 2020 Page Left Intentionally Blank ...
Page 72: ...72 JOHNSON CONTROLS FORM 150 68 ICOM1 ISSUE DATE 10 15 2020 Page Left Intentionally Blank ...
Page 79: ...79 JOHNSON CONTROLS FORM 150 68 ICOM1 ISSUE DATE 10 15 2020 YLPA P I Diagram ...
Page 86: ...86 JOHNSON CONTROLS FORM 150 68 ICOM1 ISSUE DATE 10 15 2020 Page Left Intentionally Blank ...
Page 88: ...88 JOHNSON CONTROLS FORM 150 68 ICOM1 ISSUE DATE 10 15 2020 Page Left Intentionally Blank ...