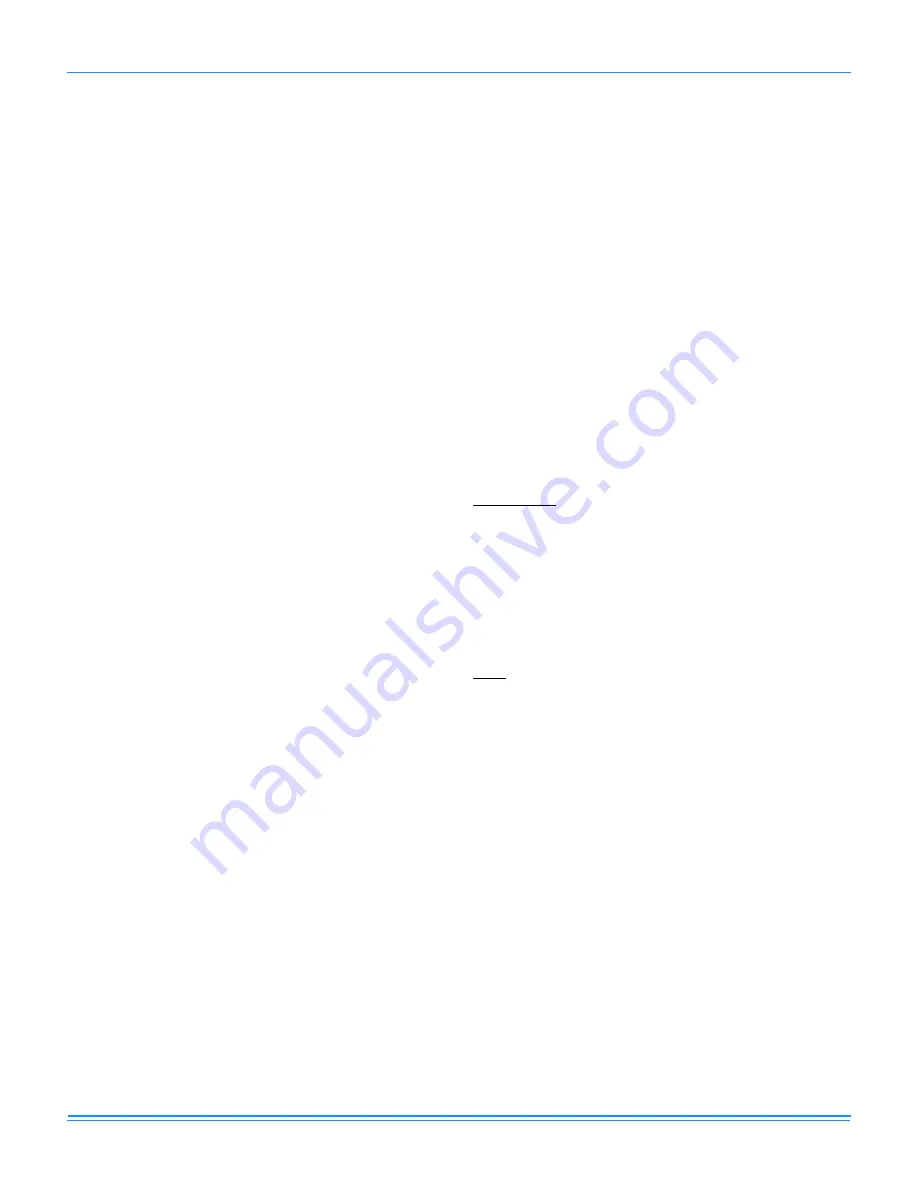
528195-YTG-I-0513
Johnson Controls Unitary Products
9
Guide Specifications
GENERAL
Units shall be manufactured by York International Unitary
Products in an ISO 9001 certified facility. YORK® Predator
®
units are convertible single packages with a common footprint
cabinet and common roof curb for all 6-1/2 through 12-1/2 ton
models. All units have two compressors with independent R-
410a refrigeration circuits to provide 2 stages of cooling. The
units were designed for light commercial applications and can
be easily installed on a roof curb, slab, or frame. All Predator
®
units are self-contained and assembled on rigid full perimeter
base rails allowing for 3-way forklift access and overhead
rigging. Every unit is completely charged with R-410a, wired,
piped, and tested at the factory to provide a quick and easy
field installation. All units are convertible between side and
down airflow. Independent economizer designs are used on
side and down discharge applications, as well as all tonnage
sizes. Predator
®
units are available in the following
configurations: heat pump and heat pump with electric heat.
Electric heaters are available as factory-installed options or
field-installed accessories.
DESCRIPTION
Units shall be factory assembled, single package (Heat Pump),
designed for outdoor installation. They shall have built in field
convertible duct connections for down discharge supply/return or
horizontal discharge supply/return and be available with factory
installed options or field installed accessories. The units shall be
factory wired, piped and charged with R-410a refrigerant and
factory tested prior to shipment. All unit wiring shall be both
numbered and color coded. The cooling performance shall be
rated in accordance with DOE and AHRI test procedures. Units
shall be CSA certified to ANSI Z21.47 and UL 1995/CAN/CSA No.
236-M90 standards.
UNIT CABINET
Unit cabinet shall be constructed of galvanized steel with
exterior surfaces coated with a non-chalking, powder paint
finish, certified at 1000 hour salt spray test per ASTM-B117
standards. Indoor blower sections shall be insulated with up to
1” thick insulation coated on the airside. Either aluminum foil
faced or elastometric rubber insulation shall be used in the
unit’s compartments and be fastened to prevent insulation from
entering the air stream. Cabinet doors shall be hinged with
toolless access for easy servicing and maintenance. Full
perimeter base rails shall be provided to assure reliable transit
of equipment, overhead rigging, fork truck access and proper
sealing on roof curb applications. Disposable 2” filters shall be
furnished and be accessible through hinged access door. Fan
performance measuring ports shall be provided on the outside
of the cabinet to allow accurate air measurements of evaporator
fan performance without removing panels or creating bypass of
the coils. Condensate pan shall be slide out design, constructed
of a non corrosive material, internally sloped and conforming to
ASHRAE 62-B9 standards. Condensate connection shall be a
minimum of ¾” I.D. female and be rigid mount connection.
INDOOR (EVAPORATOR) FAN ASSEMBLY
Fan shall be a belt drive assembly and include an adjustable
pitch motor pulley. Job site selected brake horsepower shall not
exceed the motors nameplate horsepower rating plus the ser-
vice factor. Units shall be designed to operate within the service
factor. Fan wheel shall be double inlet type with forward curve
blades, dynamically balanced to operate smoothly throughout
the entire range of operation. Airflow design shall be constant
volume. Bearings shall be sealed and permanently lubricated
for longer life and no maintenance. Entire blower assembly and
motor shall be slide out design.
OUTDOOR (CONDENSER) FAN ASSEMBLY
The outdoor fans shall be of the direct drive type, discharge air
vertically, have aluminum blades riveted to corrosion resistant
steel spider brackets and shall be dynamically balanced for
smooth operation. The outdoor fan motors shall have permanently
lubricated bearings internally protected against overload
conditions and staged independently. A cleaning window shall be
provided on two sides of the units for coil cleaning.
REFRIGERANT COMPONENTS
Compressors:
a. Shall be fully hermetic type, direct drive, internally
protected with internal high-pressure relief and over
temperature protection. The hermetic motor shall be
suction gas cooled and have a voltage range of + or –
10% of the unit nameplate voltage.
b. Shall have internal spring isolation and sound muffling to
minimize vibration and noise, and be externally isolated
on a dedicated, independent mounting.
Coils:
a. Evaporator and condenser coils shall have aluminum
plate fins mechanically bonded to seamless internally
enhanced copper tubes with all joints brazed. Special
Phenolic coating shall be available as a factory option.
b. Evaporator and condenser coils shall be of the direct
expansion, draw-thru design.
Refrigerant Circuit and Refrigerant Safety Components shall
include:
a. Independent fixed-orifice or thermally operated
expansion devices.
b. Solid core filter drier/strainer to eliminate any moisture or
foreign matter.
c. Accessible service gage connections on both suction
and discharge lines to charge, evacuate, and measure
refrigerant pressure during any necessary servicing or
troubleshooting, without losing charge.
d. The unit shall have two independent refrigerant circuits,
equally split in 50% capacity increments.