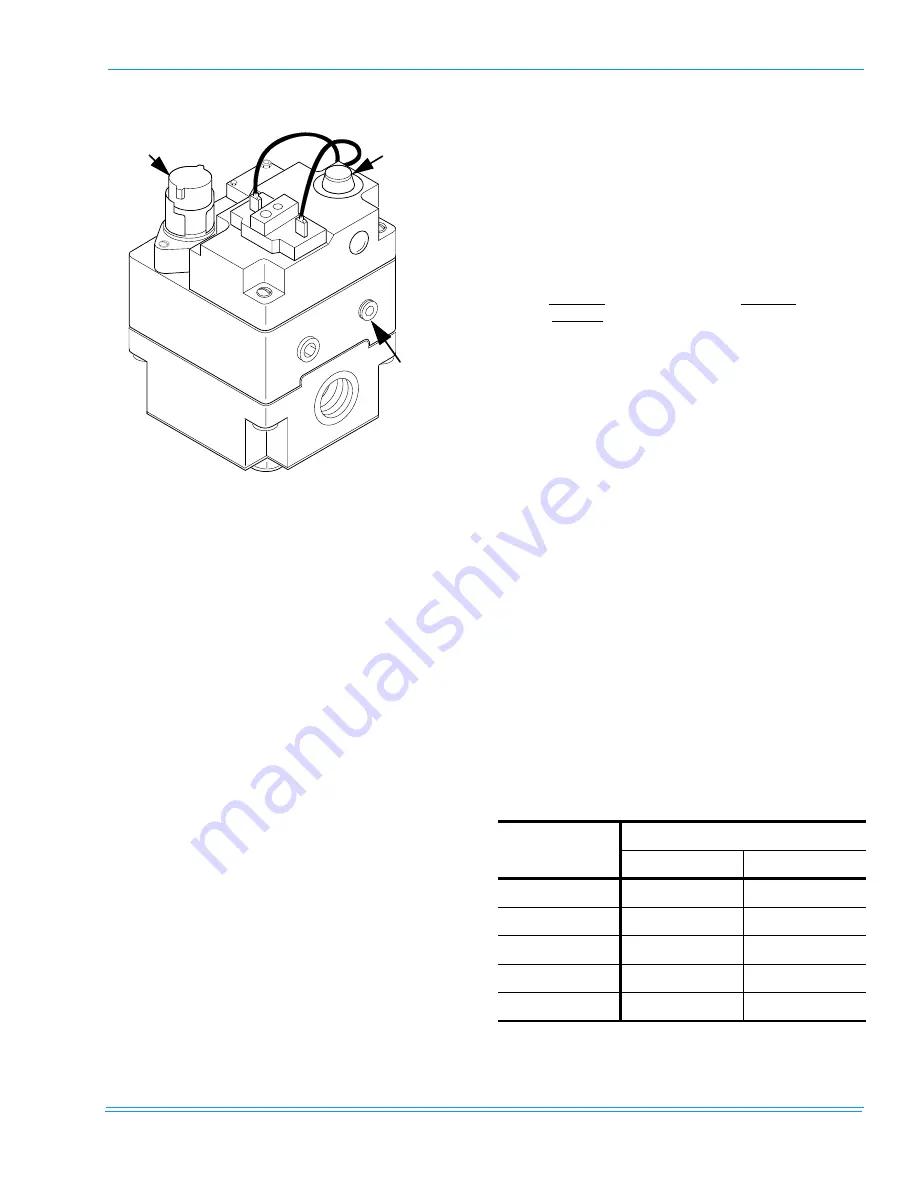
102777-YIM-E-0206
Unitary Products Group
69
BURNER INSTRUCTIONS
To check or change burners, pilot or orifices, CLOSE MAIN
MANUAL SHUT-OFF VALVE AND SHUT OFF ALL POWER
TO THE UNIT.
1.
Remove the screws holding either end of the manifold to
the burner supports.
2.
Open the union fitting in the gas supply line just
upstream of the unit gas valves and downstream from
the main manual shut-off valve.
3.
Disconnect wiring to the gas valves and spark ignitors.
Remove the manifold-burner gas valve assemblies by
pulling back.
4.
Remove the heat shield on top of the manifold support.
Burners are now accessible for service.
Reverse the above procedure to replace the assemblies.
Make sure that burners are level and seat at the rear of the
gas orifice.
ADJUSTMENT OF TEMPERATURE RISE
The temperature rise (or temperature difference between the
return air and the heated air from the furnace) must lie within
the range shown on the CGA/ETL rating plate and the data in
Table 3.
After the temperature rise has been determined, the CFM can
be calculated as follows:
After about 20 minutes of operation, determine the furnace
temperature rise. Take readings of both the return air and the
heated air in the ducts (about six feet from the furnace) where
they will not be affected by radiant heat. Increase the blower
CFM to decrease the temperature rise; decrease the blower
CFM to increase the rise. Refer to Table 30 for supply air
blower motor and drive data. Minimum allowable CFM is
6,000 CFM. Limit will open below this rating.
CHECKING GAS INPUT
NATURAL GAS
1.
Turn off all other gas appliances connected to the gas
meter.
2.
With the furnace turned on, measure the time needed for
one revolution of the hand on the smallest dial on the
meter. A typical gas meter usually has a 1/2 or a 1 cubic
foot test dial.
3.
Using the number of seconds for each revolution and the
size of the test dial increment, find the cubic feet of gas
consumed per hour from Table 41.
If the actual input is not within 5% of the furnace rating (with
allowance being made for the permissible range of the regu-
lator setting), replace the orifice spuds with spuds of the
proper size.
NOTE:
To find the Btu input, multiply the number of cubic
feet of gas consumed per hour by the Btu content of
the gas in your particular locality (contact your gas
company for this information - it varies widely from
city to city).
FIGURE 27 - TYPICAL GAS VALVE
Manual
Shutoff
Regulator
Cap
Outlet
Pressure
Tap
TABLE 41: GAS RATE - CUBIC FEET PER HOUR
Seconds for One
Rev.
Size of Test Dial
1/2 cu. Ft.
1 cu. Ft.
2
900
1800
4
450
900
6
300
600
8
225
450
10
180
360
CFM
Btuh
0.8
×
1.08
F Degrees Temp Rise
×
--------------------------------------------------------------------------
=
Summary of Contents for MILLENNIUM Y22
Page 47: ...102777 YIM E 0206 Unitary Products Group 47 FIGURE 20 ALTITUDE TEMPERATURE CONVERSION FACTOR ...
Page 50: ...102777 YIM E 0206 50 Unitary Products Group FIGURE 21 FAN PERFORMANCE 25 TON ...
Page 53: ...102777 YIM E 0206 Unitary Products Group 53 FIGURE 22 FAN PERFORMANCE 30 TON ...
Page 56: ...102777 YIM E 0206 56 Unitary Products Group FIGURE 23 FAN PERFORMANCE 40 TON ...
Page 126: ...102777 YIM E 0206 126 Unitary Products Group FIGURE 52 TYPICAL CONTROL WIRING ...
Page 127: ...102777 YIM E 0206 Unitary Products Group 127 FIGURE 53 LEGEND ...
Page 128: ...102777 YIM E 0206 128 Unitary Products Group FIGURE 54 TYPICAL 25 TON POWER WIRING ...
Page 129: ...102777 YIM E 0206 Unitary Products Group 129 FIGURE 55 TYPICAL 30 40 TON POWER WIRING ...
Page 130: ...102777 YIM E 0206 130 Unitary Products Group FIGURE 56 TYPICAL GAS HEAT WIRING ...
Page 134: ...102777 YIM E 0206 134 Unitary Products Group FIGURE 58 25 TON CHARGING CURVE ...
Page 139: ...102777 YIM E 0206 Unitary Products Group 139 ...