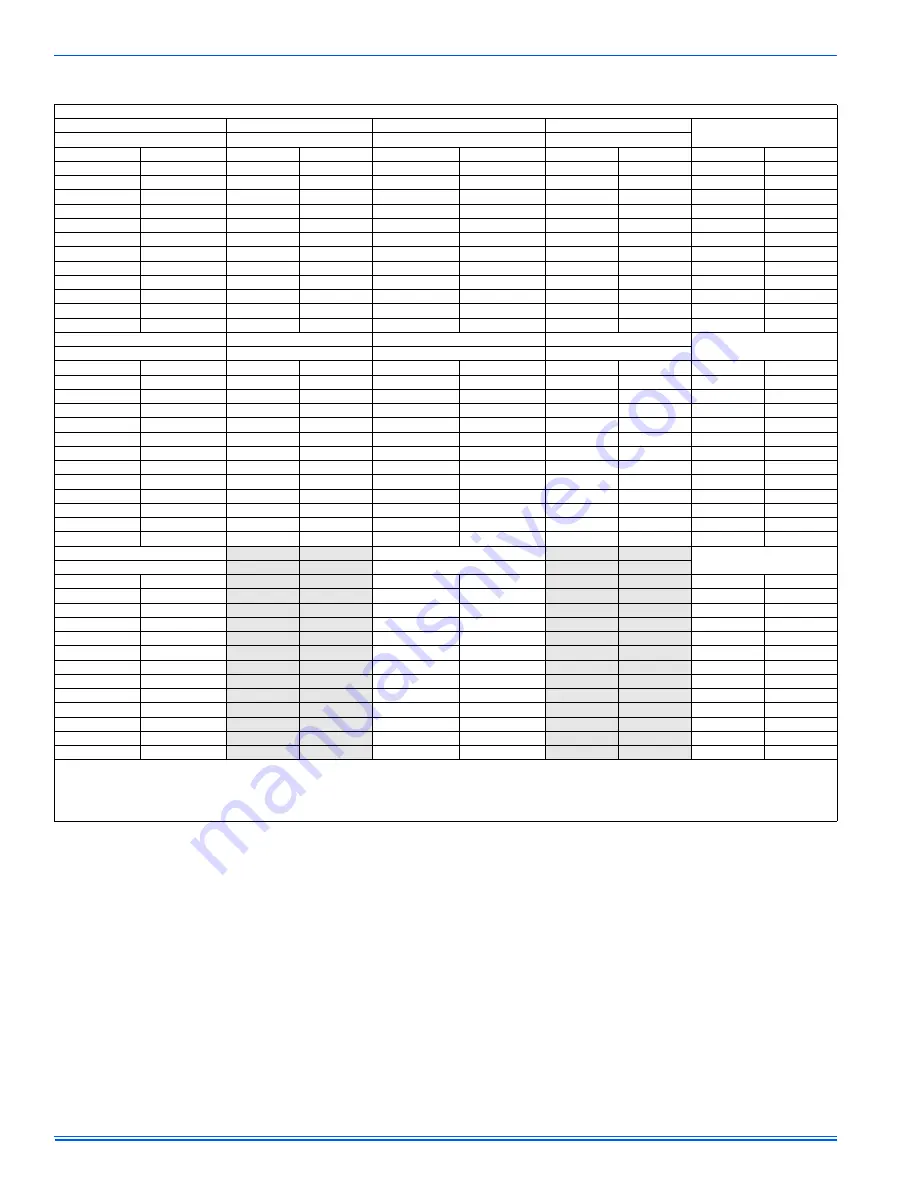
292278-UIM-A-0108
28
Unitary Products Group
NOTES:
1. Airflow expressed in standard cubic feet per minute (CFM) and in cubic meters per minute (m
3
/min).
2. Return air is through side opposite motor (left side).
3. In order to stay within the velocity rating the filters, airflows above 1800 CFM (50.97 m
3
/min) require either return from two sides or one side plus bottom.
4. Motor voltage at 115V.
FILTER PERFORMANCE
The airflow capacity data published in Table 16 represents blower per-
formance WITHOUT filters. To determine the approximate blower per-
formance of the system, apply the filter drop value for the filter being
used or select an appropriate value from the Table 17.
NOTE:
The filter pressure drop values in Table 17 are typical values for
the type of filter listed and should only be used as a guideline. Actual
pressure drop ratings for each filter type vary between filter manufactur-
ers.
TABLE 16:
Air Flow Data
HIGH / LOW SPEED COOLING AND HEAT PUMP CFM
60,000 INPUT - 3 Ton
80,000 INPUT - 3 Ton
60,000 INPUT - 3 Ton
80,000 INPUT - 3 Ton
JUMPER SETTINGS
CFM
CFM
m³/min
m³/min
High
Low
High
Low
High
Low
High
Low
COOL Tap
ADJ Tap
1330
900
1310
890
37.7
25.5
37.1
25.2
A
B
1130
800
1100
740
32.0
22.7
31.2
21.0
B
B
1220
850
1220
830
34.6
24.1
34.6
23.5
A
A
1040
730
1000
670
29.4
20.7
28.3
19.0
B
A
1120
770
1090
720
31.7
21.8
30.9
20.4
A
C
920
650
900
610
26.1
18.4
25.5
17.3
C
B
950
660
880
610
26.9
18.7
24.1
17.3
B
C
740
540
680
510
21.0
15.3
19.3
14.4
D
B
860
610
810
580
24.4
17.3
22.9
16.4
C
A
690
540
630
500
19.5
15.3
17.8
14.2
D
A
790
570
730
530
22.4
16.1
20.7
15.0
C
C
630
530
590
500
17.8
15.0
16.7
14.2
D
C
80,000/100,000 INPUT - 4 Ton
100,000 INPUT - 5 Ton
80,000/100,000 INPUT - 4 Ton
100,000 INPUT - 5 Ton
JUMPER SETTINGS
CFM
CFM
m³/min
m³/min
High
Low
High
Low
High
Low
High
Low
COOL Tap
ADJ Tap
1660
1110
2210
1480
47.0
31.4
62.6
41.9
A
B
1550
1050
1780
1180
43.9
29.7
50.4
33.4
B
B
1610
1070
2040
1350
45.6
30.3
57.8
38.2
A
A
1440
960
1620
1050
40.8
27.2
45.9
29.7
B
A
1470
990
1840
1250
41.6
28.0
52.1
35.4
A
C
1370
920
1560
1010
38.8
26.1
44.2
28.6
C
B
1290
850
1470
940
36.5
24.1
41.6
26.6
B
C
1130
790
1370
890
32.0
22.4
38.8
25.2
D
B
1230
850
1460
930
34.8
24.1
41.3
26.3
C
A
1050
720
1250
790
29.7
20.4
35.4
22.4
D
A
1110
760
1310
810
31.4
21.5
37.1
22.9
C
C
950
660
1090
690
26.9
18.7
30.9
19.5
D
C
120,000 INPUT - 5 Ton
120,000 INPUT - 5 Ton
JUMPER SETTINGS
CFM
m³/min
High
Low
High
Low
COOL Tap
ADJ Tap
2280
1510
64.6
42.8
A
B
1860
1190
52.7
33.7
B
B
2090
1370
59.2
38.8
A
A
1630
1060
46.2
30.0
B
A
1880
1250
53.2
35.4
A
C
1620
1030
45.9
29.2
C
B
1500
960
42.5
27.2
B
C
1410
880
39.9
24.9
D
B
1490
920
42.2
26.1
C
A
1290
790
36.5
22.4
D
A
1360
840
38.5
23.8
C
C
1140
690
32.3
19.5
D
C
All CFM’s are shown at 0.5” w.c. external static pressure.These units have variable speed motors that automatically adjust to provide constant CFM from 0.0” to 0.6” w.c. static
pressure. From 0.6” to 1.0” static pressure, CFM is reduced by 2% per 0.1” increase in static. Operation on duct systems with greater than 1.0” w.c. external static pressure is not
recommended.
NOTE: At some settings, LOW COOL airflow may be lower that what is required to operate an airflow switch on certain models of electronic air cleaners. Consult the instructions
for the electronic air cleaner for further details.