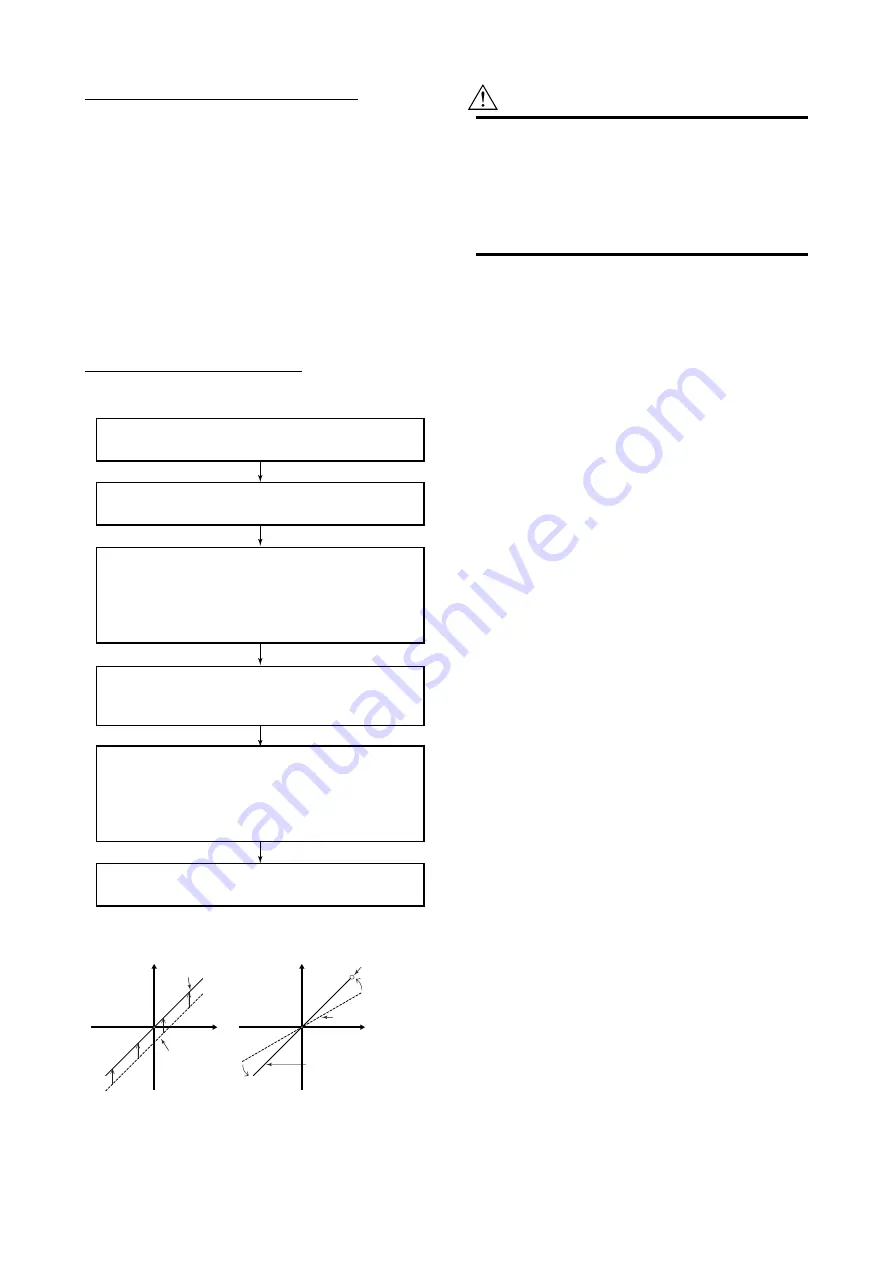
IM 01C25R03-01E
6-3
6. EXPLANATION OF BASIC ITEMS
Zero-point adjustment by the external screw.
With pressure being exerted on the point where the
adjustment is to be made, zero adjustment needs to be
performed. To do this, adjust the calculated value by
turning the external Zero-point adjustment screw, so
that it agrees with the actual input pressure (true
value). The output value increases when the screw is
rotated to the right. It decreases when the screw is
rotated to the left. The adjustment width is small when
the rotation speed is low and large when fast.
When performing zero-point adjustment by the external
screw, EXTERNAL_ZERO_TRIM needs to be set to
“Enable.”
Procedure for automatic adjustment
The procedure for automatic adjustment is as follows:
F0602.EPS
(1) Change the Block mode
Set MODE_BLK to O/S.
(2) Enter zero% pressure
Apply the actual zero% pressure to EJX910A.
(6) Change the operation mode
Set MODE_BLK to AUTO for normal operation.
(3) Perform zero adjustment
When the value of the applied pressure is written to
CAL_POINT_LO, EJX calculates the amount of
adjustment for zero adjustment. The calculated amount
of adjustment is incorporated into CAL_DEVIATION_LO.
(5) Performance of span adjustment
When the value of the applied pressure is written to
CAL_POINT_HI, EJX910A calculates the amount of
adjustment for span adjustment. The calculated amount
of adjustment is incorporated into CAL_DEVIATION_HI.
(4) Input pressure for span adjustment
For span adjustment, apply the actual 100% pressure to
EJX910A.
F0603.EPS
0
0
Calculated Value
Calculated Value
Span adjustment point
After zero adjustment
After zero adjustment
After zero/span
adjustment
Input pressure
Input pressure
Before zero
adjustment
CAUTION
Span adjustment is a function for adjusting the
gradient with respect to the point of zero adjust-
ment. If that point is not zero, the gradient of
input and output values cannot be accurately
adjusted. Perform span adjustment after zero
adjustment is completed.
Diagnosis of adjustment results:
When the amount of zero adjustment or span adjust-
ment exceeds any of the following adjustment limits,
“AL50: Adjustment range error for differential pres-
sure” is displayed.
The conditions for zero/span adjustment are as follows:
<1> The point of zero adjustment is within
±
10%
of the capsule range.
<2> The amount of zero adjustment is within
±
10%
of the capsule range.
<3> The point of span adjustment is within the
capsule range.
<4> The input and output gradients after span
adjustment are within
±
10% of the gradient at
factory setting.
6.3.4 Functions Relating to Static Pres-
sure
Reference to static pressure value:
In SECONDARY_VALUE and TERTIARY_VALUE,
it is possible to refer to the H-side static pressure value
and the L-side static pressure value, respectively. The
update period of these values is 200 msec. The
pressure unit is selected by XD_SCALE.unit in the AI
block, in which SECONDARY_VALUE and
TERTIARY_VALUE are selected. The status is
normally Good-Non Specific. However, in the case of
a sensor failure or out of measurement range, it turns
to Bad or Uncertain. For specifics, refer to Table 8.9.
Setting of signal damping for static pressure:
SP_VALUE_FTIME is parameter that set signal
damping for static pressure signals. The unit of the
signal damping is second.
Determination of the range limit of static pressure
signal:
When the static pressure signal exceeds the maximum
working pressure (MWP) of the capsule, set the status
of PRIMARY_VALUE to Uncertain-Subnormal. Also,
set the status of SECONDARY_VALUE and
TERTIARY_VALUE to Uncertain-Sensor Conversion
not Accurate. The status under normal conditions is
Good-Non Specific.