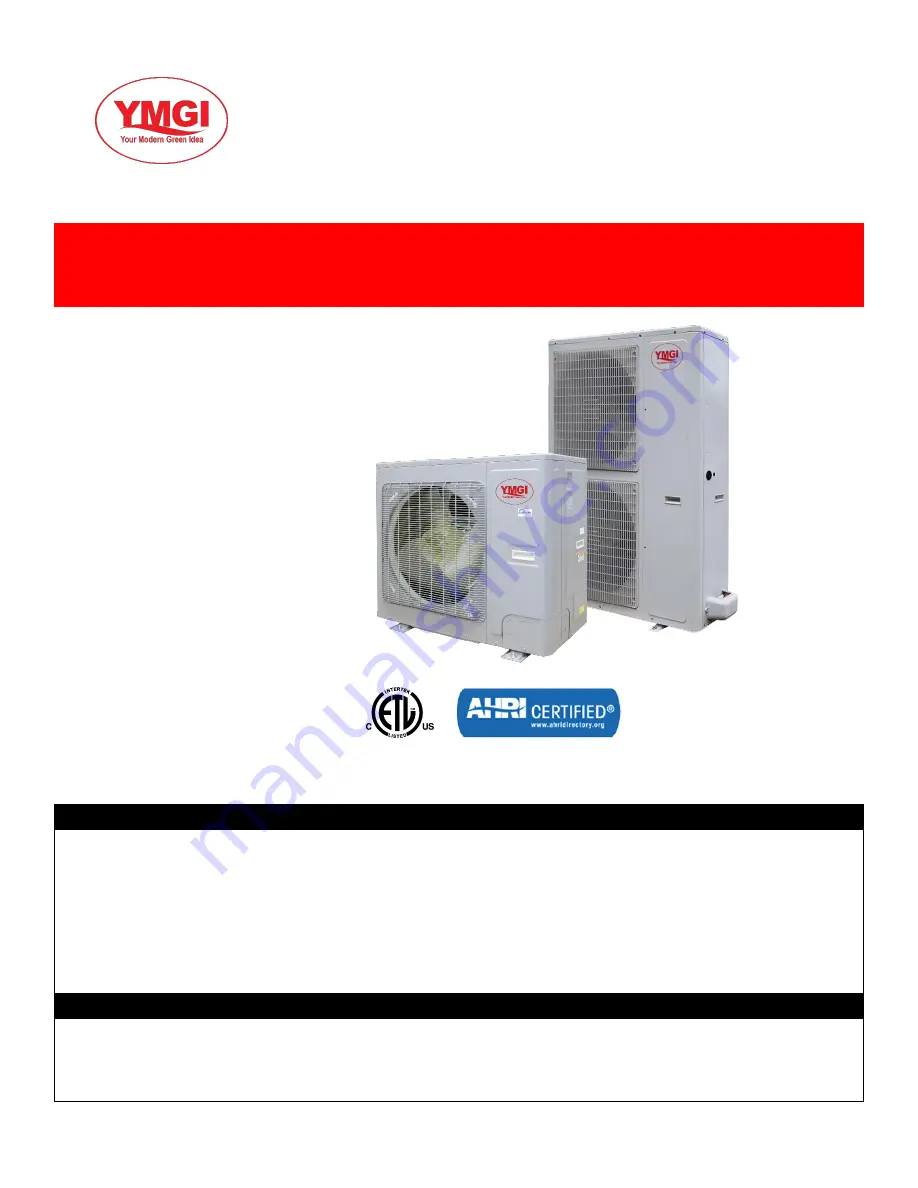
YMGI, Engineered Comfort Products for A Sustainable
and Efficient Green World!
SERVICE MANUAL
DC INVERTER SPLIT TYPE HEAT PUMP (Down to -22°F Ambient)
OUTDOOR CONDENSING UNIT
Model Numbers:
VRUO-2436HP-U2B(54)
VRUO-4860HP-U2B(54)
Thermostat-Controlled
Universal Outdoor
Condenser Works With:
1. Any Brand of American
Style Indoor Units, and
2. YMGI Indoor Unit
Universal VRUI
Thank you for choosing this YMGI product. Please read the owner’s manual carefully before installation and operation, and retain for your
records and future reference. If you need a replacement copy, please contact your local agent or visit www.ymgigroup.com to download
a current electronic version.
NOTICE
This product is designed and manufactured to be free from any defects in material and workmanship during normal use and
maintenance. Installation, operation, maintenance and repair must follow all standards and professional practices for regular cooling
and heating equipment, such as NEC, State, or Local Codes and all related documents/manuals provided by YMGI. Failure to follow
and adhere to all codes and documentation can cause damage to equipment, property even personal injury.
Installer
: Currently licensed/certified HVAC technicians only. Must Read the manual and all provided documents prior to installation.
Complete and fill out all required information on the warranty registration card.
User
: Retain this manual and all supplied documents for your records and future reference.
Servicer
: Use this manual for information concerning servicing and maintenance of this product.
SAFETY WARNING
Only qualified technicians should install and service this equipment. The installation, startup, operation and servicing of this equipment
can be hazardous and requires a HVAC professional who has been trained, licensed and certified. Installations, adjustments or any
equipment alterations done by an unqualified person could result in serious injury and even death. When working on the equipment,
observe all precautions in the provided documents, on the tags, stickers, and labels that are attached to or placed on the equipment.