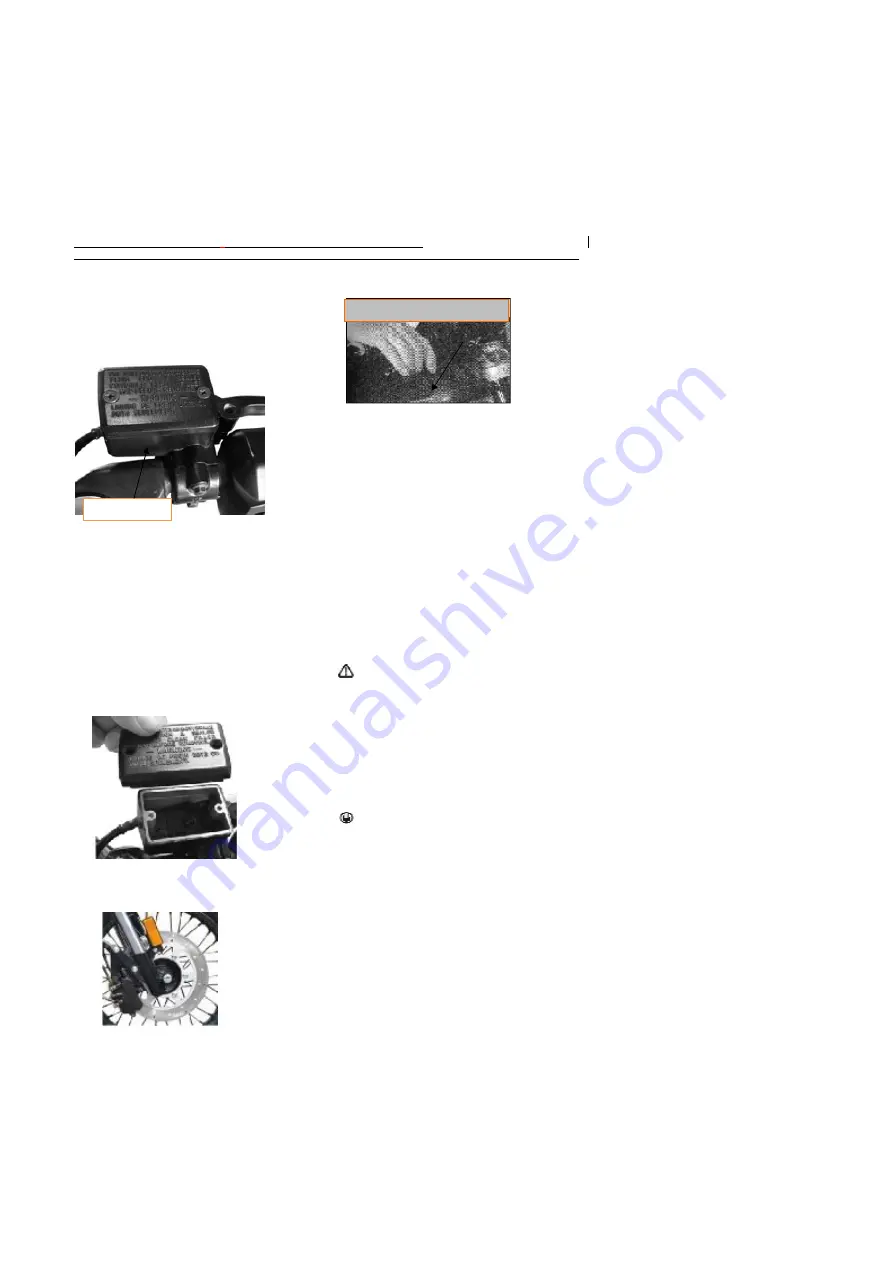
YG125-30B
Maintenance Manual
Inspection and adjustment
32
I If the brake fluid in both the front cylinders is drained,
bleed air from the deflating valve of the brake caliper with
a vacuum pump, and then refill brake fluid into the
cylinder.
Brake fluid vacuum filling method:
This method is only applicable to refilling brake fluid for
new vehicles or when the brake fluid in the cylinder is
drained.
1.
Bleed air from the deflating valve of the vacuum
pump
’
s caliper
2.
Open the cover of brake cylinder cover and refill
brake fluid.
3.
Actuate the brake handle, exhaust the air in the dead
corner of the brake caliper.
4.
5.
When the vacuum pump has fully exhausted the air
inside the brake caliper, after the brake fluid is
pumped out, firmly nip the handle or completely push
down quickly screw the deflating valve bolt, with the
torque being 7-9 N.m.
6.
Mount the brake cylinder cover with the sealing
gasket flattened, and replace with new sealing
gasket as required.
7.
After refilling, check the oil cup, hydraulic brake hose
and all connecting pieces for leakage.
Notice
1
The brake fluid shall be DOT 4 non-petroleum
base brake fluid.
The brake fluid can
’
t be mixed with other
2
Impurities; otherwise the braking performance
shall be reduced due to chemical change.
Caution
The brake fluid is strongly corrosive, never splash it
onto the surfaces of sprays painted or plastic pieces;
in case it splashes into the eyes or on the skin,
immediately flush with large amounts of fresh water
and see a doctor.
Brake piece checking
Operating brake, if the wears limit line of the brake shoe
Actuate the front brake handle
Min. scale line
Summary of Contents for YG125-30B
Page 99: ...YG125 30B Maintenance Manual Frame and exhaust system 106 10 Frame and exhaust system...
Page 130: ...YG125 30B Maintenance Manual Illumination signal system 136 Circuit schematic drawing...
Page 141: ...YG125 30B Maintenance Manual Engine management system 147 Circuit schematic drawing...
Page 151: ...YG125 30B Maintenance Manual Electrical System Diagram 157 19 Electrical System Diagram...