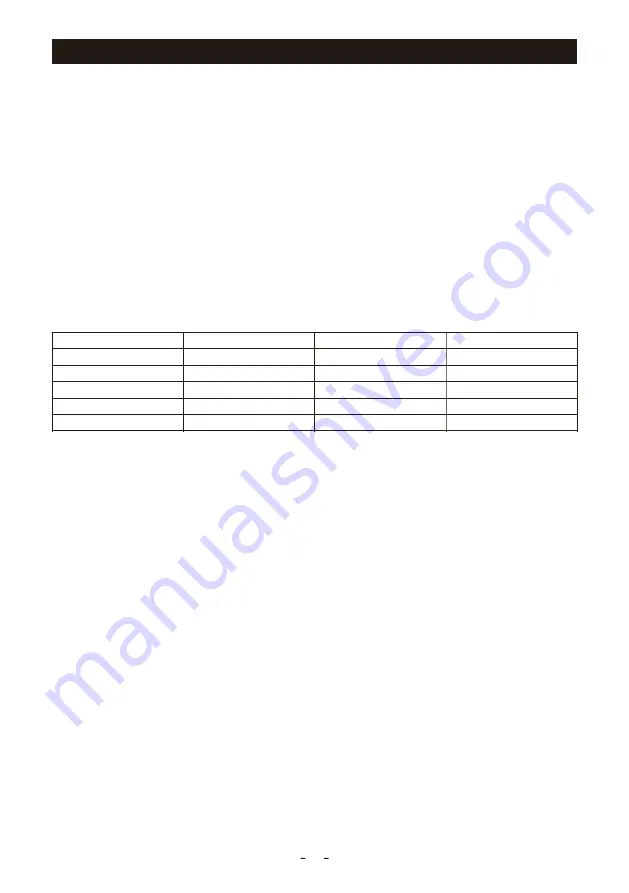
BASIC KNOWLEDGE OF WELDING
Welding Process Parameters
The gas protective effect, welding stability, and weld bead quality of GTAW have a direct relationship with the welding process pa-
rameters. Therefore, select appropriate welding process parameters to ensure high-quality weld joint.
The welding process parameters for GTAW include type and polarity of current, the diameter of tungsten electrode, welding current,
argon gas flow, welding speed, and process factors, etc.
A. The type and polarity of current for GTAW should be chosen according to the workpiece material and also the operation mode.
B. Select tungsten electrodes with proper diameter mainly according to the thickness of the workpiece. Besides, when the thickness
of the workpiece is the same, tungsten electrodes with different diameters should be chosen due to the different current types and
polarities and different allowable current ranges for the tungsten electrode. Improper tungsten diameter will lead to unstable arc, seri-
ous burn, and tungsten in the weld bead.
C. Select proper welding current after the tungsten diameter is determined. Overly high or overly low welding current will cause poor
weld bead or welding defects. For the allowable current ranges for thorium-tungsten/cerium tungsten electrodes with different diam-
eters, please refer to the table below (Table 1).
Table 1 Allowable Current Ranges for Tungsten Electrodes with Different Diameters
Tungsten Dia. (mm)
DCEN (A)
DCEP (A)
AC (A)
1.0
15~80
–
20~60
1.6
70~150
10~20
60~120
2.4
150~250
15~30
100~180
3.2
250~400
25~40
160~250
4.0
400~500
40~55
200~320
D. The argon gas flow is selected mainly according to the tungsten diameter and nozzle diameter. For a nozzle with a certain aper-
ture, the argon gas flow should be appropriate. If the gas flow is too high, the gas flow speed will increase. Thus, it is difficult to main-
tain stable laminar flow, and the welding zone can not be well protected. Meanwhile, more arc heat will be taken away, which will af-
fect the arc stability. If the gas flow is too low, the gas protective effect will be affected due to the interference of the environmental
airflow. Generally, the argon gas flow should be within 3~20L/min.
E. Under the condition of fixed tungsten diameter, welding current, and argon gas flow, overly high welding speed will make the pro-
tective gas flow deviate from the tungsten electrode and molten pool, and the gas protective effect will be affected accordingly. Be-
sides, the welding speed affects the weld bead shape significantly. Therefore, it is very important to select the appropriate welding
speed.
F. Process factors mainly refer to the shape and diameter of the nozzle, the distance between the nozzle and workpiece, stick-out
and the diameter of filling wire, etc. Although the change in these factors is not big, it has more or less influence on the welding pro-
cess and gas protective effect. Therefore, all factors should be selected according to specific welding requirements.
Generally, the nozzle diameter should be within 5~20mm, the distance between the nozzle and workpiece should not be greater
than 15mm, the stick-out should be 3~4mm, and the filling wire diameter should be selected according to the thickness of the
workpiece.
General Requirements for Argon Arc Welding
1. The control of gas: Pre-flow and post-flow are required in argon arc welding. Argon is a kind of inert gas that can be broken down
easily. Fill the space between the workpiece and the tungsten electrode with argon firstly, and then the arc can be easier to ignite.
Keep the gas flowing after welding ends, and the workpiece will not cool down too quickly. Thus, the oxidization of the workpiece
can be avoided, and a good welding effect can be ensured.
2. The manual switch control of current: When the manual switch is switched on, the current supply should be delayed for the pre-
flow time. After the manual switch is switched off and welding ends, the current supply should be cut off first and the gas flow main-
tains according to the post-flow time.
3. The generation and control of high voltage: The argon arc welding machine adopts high voltage arc ignition mode. It is required
that there should be high voltage when igniting the arc and there should be no high voltage after the arc is successfully ignited.
4. Protection from interference: The high voltage for arc ignition in argon arc welding is accompanied by high frequency, which pro-
duces serious interference to the machine circuit. Thus, good anti-interference ability is required for the circuit.
In addition, the gas protective effect can be judged by directly observing the color of the weld bead surface. Take stainless steel
welding for example. If the weld bead surface appears silvery white or golden, it indicates that the gas protective effect is good.
However, if the weld bead surface appears gray or black, it indicates that the gas protective effect is poor.
41
Summary of Contents for CT2050
Page 55: ...15 WIRING DIAGRAM 52 ...
Page 56: ...www YesWelder com V2 01 ...