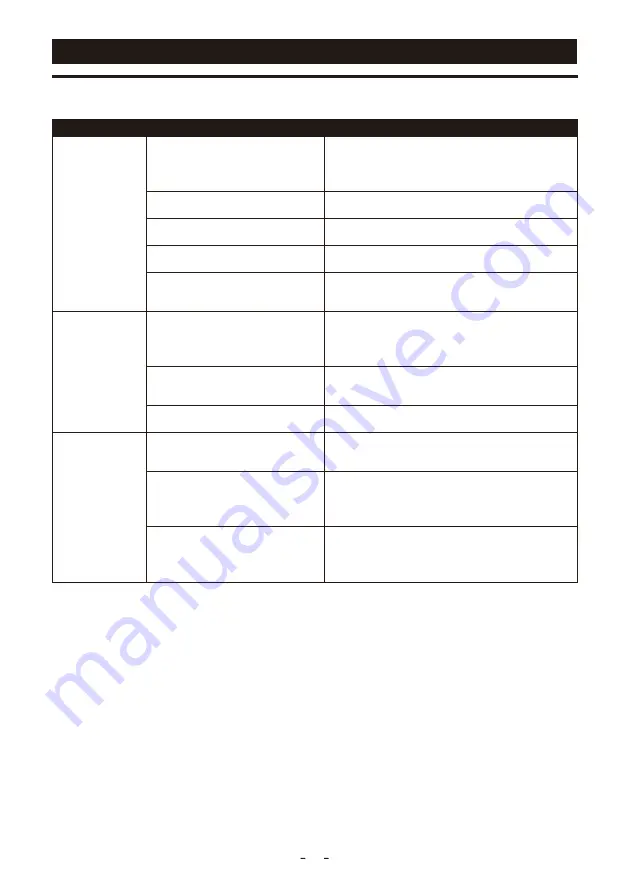
Check & secure work clamp.
Poor work clamp connection.
No gas, incorrect gas flow.
Check the gas is connected and cylinder valve open, check
hoses, gas valve and torch are not restricted. Set the gas
flow between 20-30 cfh flow rate.
PROBLEM
POSSIBLE CAUSE
COURSE OF ACTION
HF TIG doesn't initi-
ate an arc:
TROUBLESHOOTING
TIG WELDING ISSUES
Check all connectors and tighten.
Loose connection.
Connect the work clamp directly to the work piece wher-
ever possible.
Earth clamp not connected to work.
Grind to ctean Tungsten.
Contaninated Tungsten.
Tungsten burning
away quickly.
Incorrect Gas/Inadequate gas flow.
Check the gas cylinder contains pure Argon gas and is
connected and the torch gas valve is open. Set the gas
flow between 20-30cfh flow rate.
Make sure the torch back cap is fitted so that the o-ring is
inside the torch body.
Back cap not fitted correctly.
Check and change the tungsten type if necessary.
Incorrect tungsten being used.
Contaminated tung-
sten.
Touching the filler wire to the tungsten.
Keep the filler wire from touching the tungsten during
welding, feed the filler wire into the leading edge of the
weld pool in front of the tungsten.
Keep tungsten from contacting weld puddle. Raise the
torch so that the tungsten is off of the work piece 1/8-1/4.
Touching tungsten into the weld pool.
Check that correct type of tungsten is being used. Too
much current for the tungsten size so reduce the amps or
change to a larger tungsten.
Tungsten melting into the weld pool.
48
Summary of Contents for CT2050
Page 55: ...15 WIRING DIAGRAM 52 ...
Page 56: ...www YesWelder com V2 01 ...