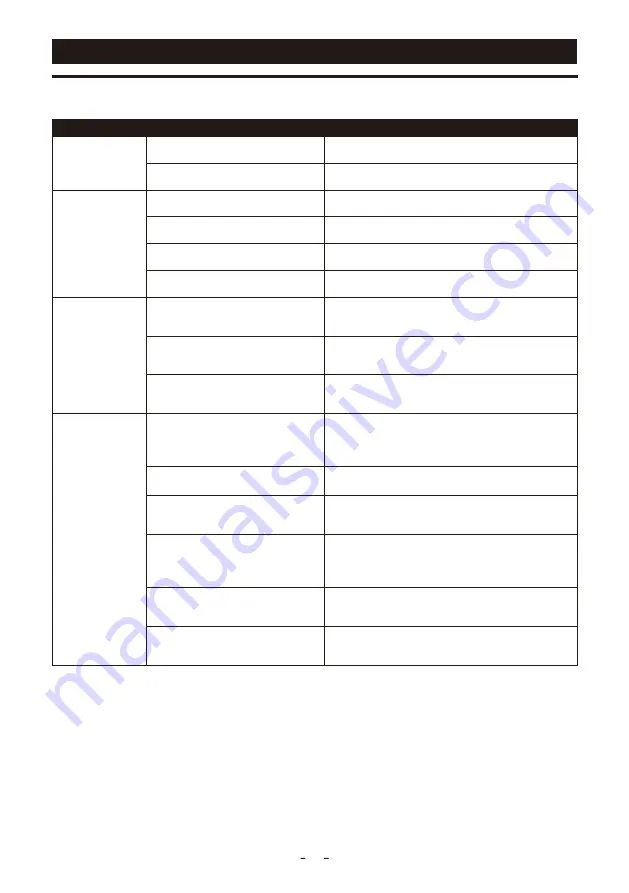
Increase Start current.
Start current is too low.
Poor work clamp connection.
Check and secure work connection.
PROBLEM
POSSIBLE CAUSE
COURSE OF ACTION
Poor starting.
TROUBLESHOOTING
TIG WELDING ISSUES
Grind to clean electrode.
Tungsten electrode may be contaminated.
Check connection.
Leaks in gas line or torch connection.
Black area along
weld bead.
Clean work piece.
Oily or organic contamination on work
Replace the gas tank.
Gas tank is near empty.
Remove materials like paint, grease, oil, and dirt, including
mill scale from base metal.
Contaminated base metal.
Tungsten is contaminated.
Unstable Arc.
Remove 25/64" of contaminated tungsten and re-grind the
tungsten.
Arc length too long.
Lower torch so that the tungsten is off of the work piece
5/64"-13/64"(2-5mm).
Arc wanders.
Tungsten incorrect or in poor condition.
Check that correct type of tungsten is being used. Remove
tungsten 3/4" from the weld end and re-sharpen the
tungsten.
Insufficient gas shielding.
Check and set the gas flow between 20-30cfh flow rate.
Contaminated gas or leaks in gas line,
torch, or connections.
Check gas line & connections.
Poorly prepared tungsten.
Recommend tungsten grind angles range from 15 to 60 de-
grees based on the type of metal, joint design and penetra-
tion you desire. Standard is 30 degrees.
Contaminated base metal.
Remove contaminating materials like paint, grease, oil, and
dirt, including mill scale from base metal.
Contaminated/Incorrect filler.
Check the filler wire and remove all grease, oil, or moisture
from filler metal.
47
Summary of Contents for CT2050
Page 55: ...15 WIRING DIAGRAM 52 ...
Page 56: ...www YesWelder com V2 01 ...