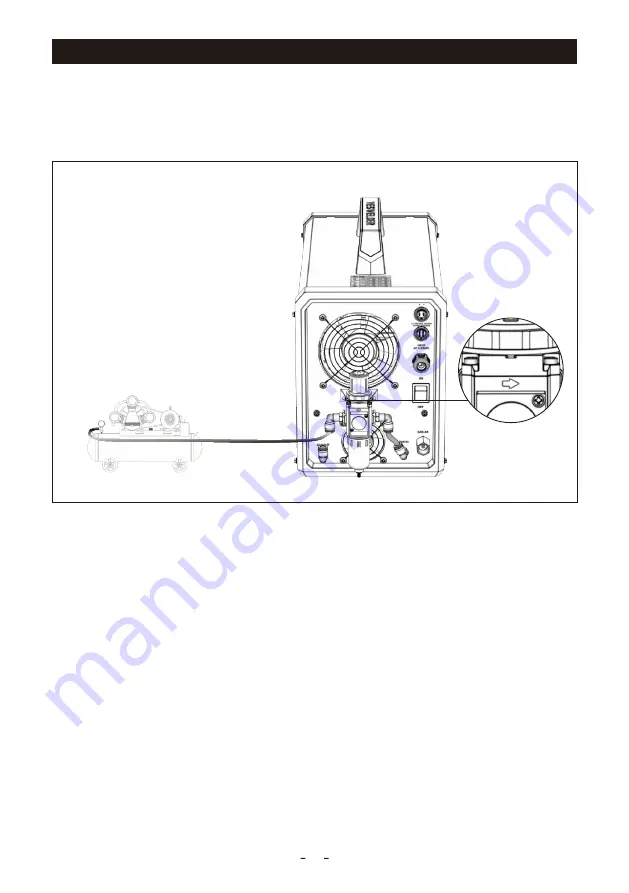
Air routing way
Installation for Air Pressure Compressor Filter Regulator
YesWelder CT2050 could support plasma cutting with built-in compressor air and plasma cutting with outer air from an external com-
pressor.
The built-in compressor makes it easy to take on various outdoor projects, and making life for welders on the road that much easier.
It’s able to start cutting without an extra air compressor.
Access to an external air compressor makes cutting more powerful and with better quality.
29
Summary of Contents for CT2050
Page 55: ...15 WIRING DIAGRAM 52 ...
Page 56: ...www YesWelder com V2 01 ...