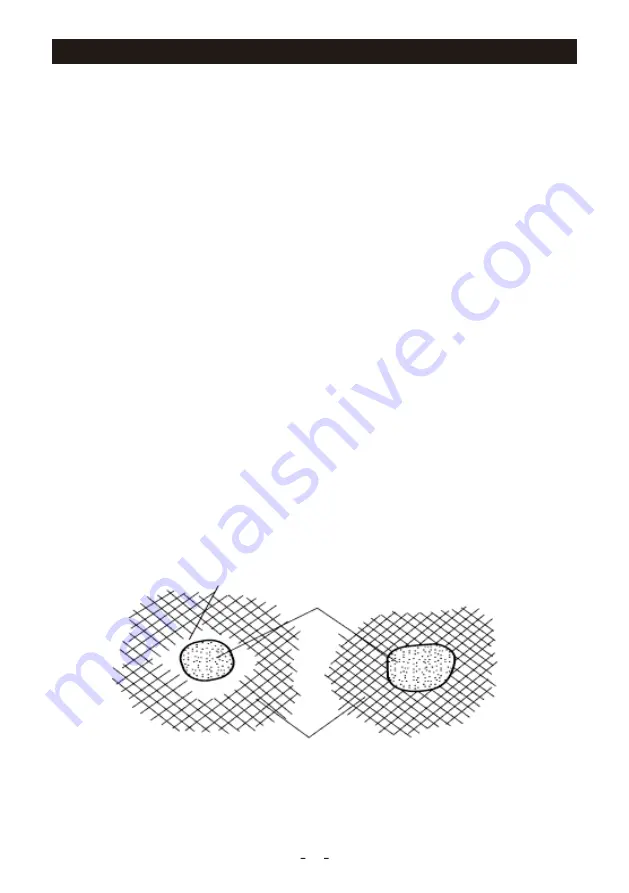
BASIC KNOWLEDGE OF WELDING
1. Preweld cleaning
GTAW Process
Clean the electrode and the zone near the weld joint of the workpiece, and remove impurities such as oil pollution and the oxidized
film on the surface of the metal before carrying out argon arc welding to ensure good quality of weld bead. The methods for preweld
cleaning are: mechanical cleaning, chemical cleaning and chemical & mechanical cleaning.
A. Mechanical cleaning: This method is simple with good effect, and it is suitable for large-sized workpiece. Generally, remove the
oxidized film by grinding with a small-diameter stainless steel wire brush or by shoveling with a scraper to make the welding position
appearing with metal luster, and then clean the weld joint zone with organic solvent for eliminating oil pollution.
B. Chemical cleaning: Chemical cleaning is commonly used for cleaning the filling electrode and small-sized workpiece. Compared
with mechanical cleaning, this method has such characteristics as high cleaning efficiency, uniform and stable quality and long dura-
tion of clean state. The chemical solutions and processes used in chemical cleaning should be chosen according to the welding ma-
terials and welding requirements.
C. Chemical & mechanical cleaning: Use chemical cleaning method when cleaning firstly, and clean the welding position with me-
chanical cleaning method before welding. This combined cleaning method is suitable for the high quality welding.
2. Protective effect of gas
Argon is ideal protective gas. The boiling point of argon is -186
, which is between that of helium and oxygen. Argon is a byprod-
°C
uct when the oxygen installation gets oxygen by fractionating the liquid air. Bottled argon is used for welding in our country. The fill-
ing pressure is 15MPa under room temperature, and the cylinder is painted gray and marked with “Ar”. The chemical composition re-
quirements of pure argon are: Ar≥99.99%; He≤0.01%; O2≤0.0015%; H2≤0.0005%; C≤0.001%; H2O≤30mg/m3.
Welding arc can be better protected and the consumption of shield gas can be reduced in flat position welding. As inert gas, argon
does not react with metal chemically even under high temperature. Thus, the alloying elements will not be oxidized or burned out,
and problems caused accordingly will be avoided. Meanwhile, argon is insoluble in liquid metal, so air holes can be avoided. Argon
is a kind of monatomic gas, existing in atomic state, without molecular decomposition and atomic endotherm under high tempera-
ture. Besides, the specific heat capacity and heat conductivity is low, so the arc heat is not easy to lose. Accordingly, the welding
arc can burn stably and heat can be concentrated, which is advantageous to welding.
The disadvantage of argon is that its ionization potential is high. When the arc space is fully filled with argon, arc is hard to ignite.
However, arc will become stable once it is successfully ignited.
The gas protective effect of argon can be affected by various process factors during welding. Therefore, special attention should be
paid to the effective protection of argon in GTAW to avoid interference and damage. Otherwise, satisfactory welding quality is hard
to obtain.
Welding process factors such as gas flow, shape and diameter of nozzle, distance between nozzle and workpiece, welding speed
and weld joint form may affect the gas protective effect, so all these should be fully considered and chosen correctly.
The gas protective effect can be judged by welding spot testing method through measuring the size of the effective gas protective
area. For example, keep all welding process factors fixed when carrying out spot welding on aluminum plate with AC manual TIG,
maintain the torch in the fixed position after arc is ignited, and cut off the power after the 5~10s, there will be a molten welding spot
left on the aluminum plate. Due to the cathode cleaning action against the area around the welding spot, the oxidized film on the sur-
face of the aluminum plate is eliminated, and a gray area with metallic luster appears. As shown in 26, this area is called effective ar-
gon protective area. The greater the diameter of the effective gas protective area, the better is the gas protective effect.
Fig 26 Effective protective area of argon
40
Effective gas protective area
Molten area
Oxidized area
(a) Good protective effect
(b) Poor protective effect
Summary of Contents for CT2050
Page 55: ...15 WIRING DIAGRAM 52 ...
Page 56: ...www YesWelder com V2 01 ...