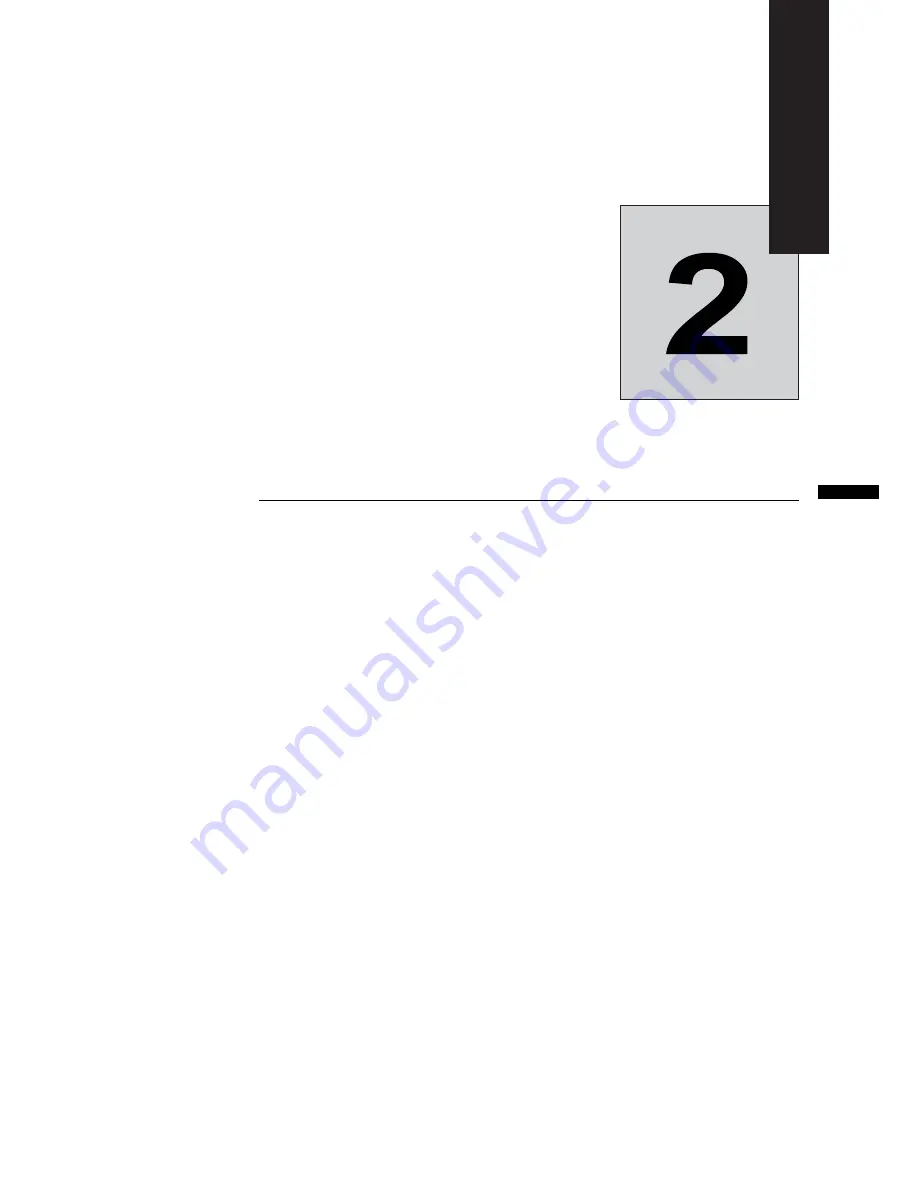
2
Wiring
This chapter describes wiring terminals, main circuit terminal connections, main circuit termi-
nal wiring specifications, control circuit terminals, and control circuit wiring specifications.
Connections to Peripheral Devices..............................2-2
Connection Diagram ....................................................2-3
Terminal Block Configuration .......................................2-5
Wiring Main Circuit Terminals ......................................2-6
Wiring Control Circuit Terminals ................................2-19
Wiring Check .............................................................2-27
Installing and Wiring Option Cards ............................2-28
http://nicontrols.com
Summary of Contents for Varispeed L7
Page 3: ...http nicontrols com...
Page 55: ...2 30 http nicontrols com...
Page 129: ...4 62 http nicontrols com...
Page 197: ...5 68 http nicontrols com...
Page 219: ...6 22 http nicontrols com...
Page 243: ...9 14 http nicontrols com...