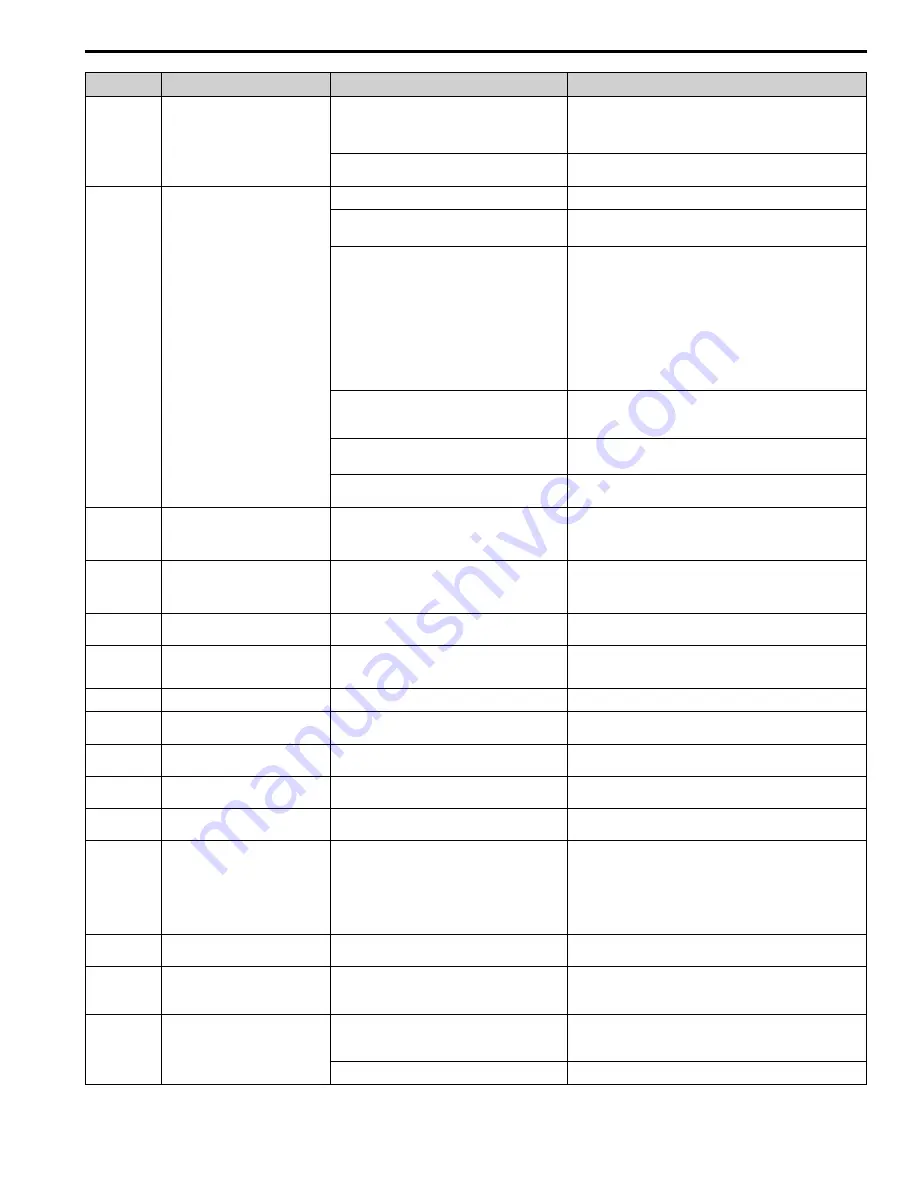
YASKAWA
TOEPC71061782C GA800 Drive Installation & Primary Operation
91
Code
Name
Causes
Possible Solutions
There is damage to the communications circuitry.
•
Do a self-diagnostics check.
•
If the problem continues, replace the control board or the drive.
Contact Yaskawa or your nearest sales representative to replace
the control board.
The termination resistor setting for MEMOBUS/
Modbus communications is incorrect.
On the last drive in a MEMOBUS/Modbus network, set DIP switch
S2 to the ON position to enable the termination resistor.
CE
Modbus Communication Error
The communications cable wiring is incorrect.
Correct wiring errors.
There is a short circuit in the communications cable
or the communications cable is not connected.
•
Repair short circuits and connect cables.
•
Replace the defective communications cable.
Electrical interference caused a communication data
error.
•
Examine the control circuit lines, main circuit lines, and ground
wiring, and decrease the effects of electrical interference.
•
Make sure that a magnetic contactor is not the source of the
electrical interference, then use a Surge Protective Device if
necessary.
•
Use only the recommended cables or other shielded line. Ground
the shield on the controller side or the drive input power side.
•
Separate the communication wiring from drive power lines, and
install a noise filter to the input side of the power supply for
communication.
•
Decrease the effects of electrical interference from the controller.
The communication protocol is not compatible.
•
Examine the values set in
H5-xx
.
•
Examine the settings on the controller side and correct the
difference in communication conditions.
The value set in
H5-09 [CE Detection Time]
is too
small for the communications cycle.
•
Change the controller software settings.
•
Increase the value set in
H5-09
.
The controller software or hardware is causing a
communication problem.
Examine the controller and remove the cause of the problem.
CP1
Comparator 1 Limit Error
The monitor value set in
H2-20 [Comparator 1
Monitor Selection]
was in the range of
H2-21
[Comparator 1 Lower Limit]
and
H2-22
[Comparator 1 Upper Limit]
.
Examine the monitor value and remove the cause of the error.
CP2
Comparator 2 Limit Error
The monitor value set in
H2-26 [Comparator 2
Monitor Selection]
was outside the range of
H2-27
[Comparator 2 Lower Limit]
and
H2-28
[Comparator 2 Upper Limit]
.
Examine the monitor value and remove the cause of the error.
CrST
Cannot Reset
The drive received a fault reset command when a Run
command was active.
Turn off the Run command then de-energize and re-energize the
drive.
CyC
MECHATROLINK
CommCycleSettingErr
The communications cycle setting of the controller is
not in the permitted range of the MECHATROLINK
interface option.
Set the communications cycle of the controller in the permitted
range of the MECHATROLINK interface option.
dEv
Speed Deviation
The load is too heavy
Decrease the load.
dnE
Drive Disabled
A terminal set for
H1-xx = 6A [Drive Enable]
turned
OFF.
Examine the operation sequence.
dWAL
DriveWorksEZ Alarm
There was an error in the DriveWorksEZ program.
Examine the DriveWorksEZ program and remove the cause of the
error. This is not a drive fault.
dWA2
DriveWorksEZ Alarm 2
There was an error in the DriveWorksEZ program.
Examine the DriveWorksEZ program and remove the cause of the
error. This is not a drive fault.
dWA3
DriveWorksEZ Alarm 3
There was an error in the DriveWorksEZ program.
Examine the DriveWorksEZ program and remove the cause of the
error. This is not a drive fault.
E5
MECHATROLINK Watchdog Timer
Err
The drive detected a watchdog circuit exception while
it received data from the controller.
Examine the MECHATROLINK cable connection. If this error
occurs frequently, examine the wiring and decrease the effects of
electrical interference as specified by these manuals:
•
MECHATROLINK-II Installation Guide (MECHATROLINK
Members Association, manual number MMATDEP011)
•
MECHATROLINK-III Installation Manual (MECHATROLINK
Members Association, publication number MMATDEP018)
EF
FWD/REV Run Command Input
Error
A forward command and a reverse command were
input at the same time for longer than 0.5 s.
Examine the forward and reverse command sequence and correct
the problem.
EF0
Option Card External Fault
The communication option card received an external
fault from the controller.
1.
Find the device that caused the external fault and remove the
cause.
2.
Clear the external fault input from the controller.
EF1
External Fault (Terminal S1)
MFDI terminal S1 caused an external fault through an
external device.
1.
Find the device that caused the external fault and remove the
cause.
2.
Clear the external fault input in the MFDI.
The wiring is incorrect.
Correctly connect the signal line to MFDI terminal S1.