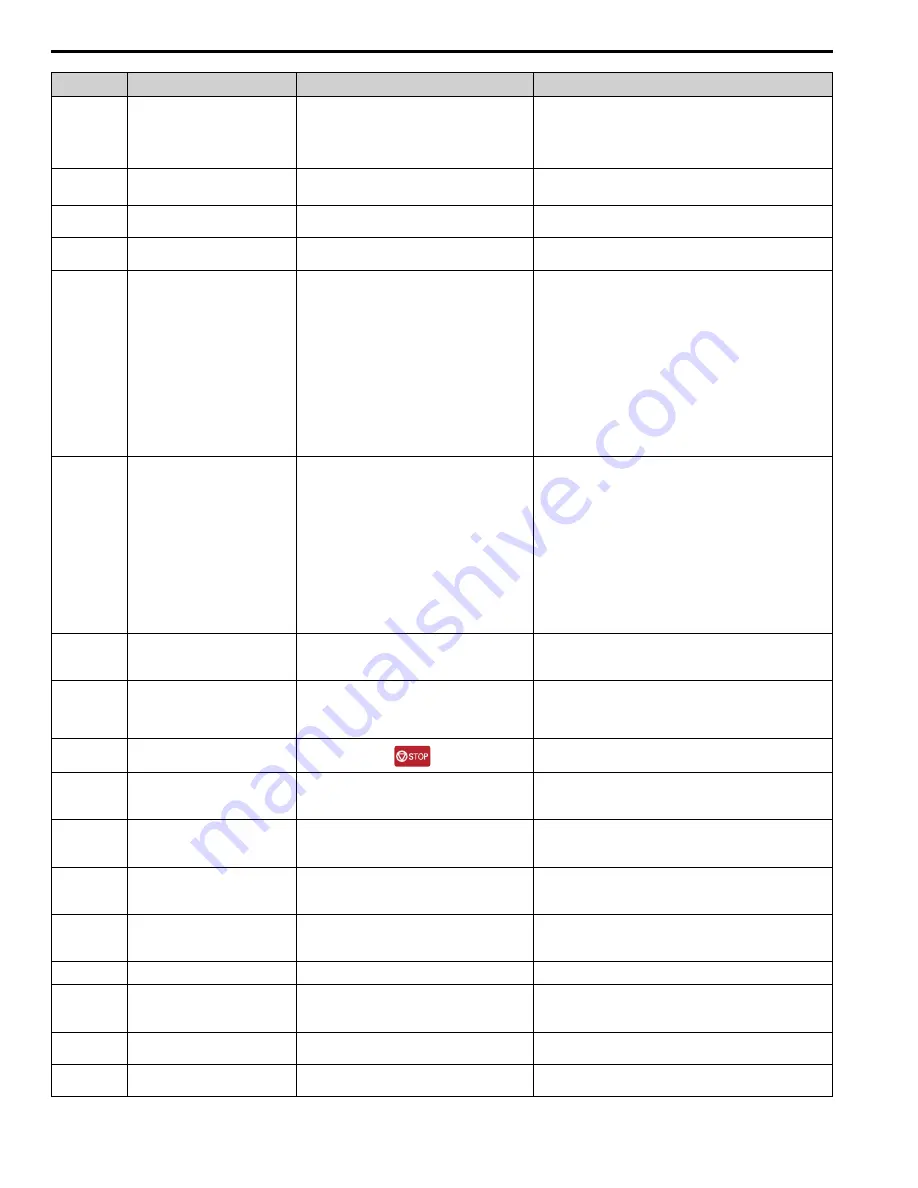
98
YASKAWA
TOEPC71061782C GA800 Drive Installation & Primary Operation
Code
Name
Causes
Possible Solutions
End4
Adjusted Slip Calculation Error
The Auto-Tuning results were not in the applicable
parameter setting range.
•
Make sure the input motor nameplate data is correct.
•
Do Rotational Auto-Tuning again and correctly set the motor
nameplate data.
•
If you cannot uncouple the motor and load, do Stationary Auto-
Tuning 2.
End5
Resistance Tuning Error
The Auto-Tuning results of the Line-to-Line
Resistance were not in the applicable range.
•
Make sure that the input motor nameplate data is correct.
•
Examine and repair damaged motor wiring.
End6
Leakage Inductance Alarm
The Auto-Tuning results were not in the applicable
parameter setting range.
Make sure that the input motor nameplate data is correct, and do
Auto-Tuning again.
End7
No-Load Current Alarm
The Auto-Tuning results of the motor no-load current
value were not in the applicable range.
Examine and repair damaged motor wiring.
End8
HFI Alarm
•
Inductance saliency ratio (
E5-07
/
E5-06
) is too
small.
•
The drive cannot find the
n8-36 [HFI Frequency
Level for L Tuning]
value.
•
Set the correct value on the motor nameplate
E5-xx [PM motor
parameters]
or do Stationary/Rotational Auto-Tuning, and then
do High Frequency Injection Tuning again.
•
When it is necessary to set
n8-35 = 1 [Initial Pole Detection
Method = High Frequency Injection]
or
n8-57 = 1 [HFI Overlap
Selection = Enabled]
, make sure that there is no unusual noise in
the low speed range (10% or less) and that the motor does not
rotate in reverse at start.
If there is unusual noise in the low speed range (10% or less),
increase
n8-41
in increments of 0.5. Set
n8-41 > 0.0
for IPM
motors.
Note:
If the drive detects
End8
, it will automatically set
n8-35 =0
[Pull-in]
and
n8-57 = 0 [Disabled]
. Do not change the settings
unless necessary.
End9
Initial Pole Detection Alarm
The drive cannot calculate the correct value for
n8-84
[Polarity Detection Current]
during High Frequency
Injection Tuning.
•
Set the correct value on the motor nameplate
E5-xx [PM motor
parameters]
or do Stationary/Rotational Auto-Tuning, and then
do High Frequency Injection Tuning again.
•
When
n8-35 = 1 [Initial Pole Detection Method = High
Frequency Injection]
or
n8-57 = 1 [HFI Overlap Selection =
Enabled]
, make sure that the motor does not rotate in reverse at
start.
If there is unusual noise in the low speed range (10% or less),
increase
n8-41
in increments of 0.5. Set
n8-41 > 0.0
for IPM
motors.
Note:
If the drive detects
End9
, it will automatically set
n8-35 =0
[Pull-in]
and
n8-57 = 0 [Disabled]
. Do not change the settings
unless necessary.
Er-01
Motor Data Error
The motor nameplate data entered during Auto-
Tuning is incorrect.
•
Make sure that the motor nameplate data is correct.
•
Do Auto-Tuning again and correctly set the motor nameplate
data.
Er-02
Drive in an Alarm State
The motor nameplate data entered during Auto-
Tuning is incorrect.
•
Make sure that the motor nameplate data entered in Auto-Tuning
is correct.
•
Do Auto-Tuning again and correctly set the motor nameplate
data.
Er-03
STOP Button was Pressed
During Auto-Tuning,
was pushed.
Auto-Tuning did not complete correctly. Do Auto-Tuning again.
Er-04
Line-to-Line Resistance Error
The Auto-Tuning results were not in the applicable
parameter setting range.
•
Examine and repair motor wiring.
•
Disconnect the machine from the motor and do Rotational Auto-
Tuning again.
Er-05
No-Load Current Error
The Auto-Tuning results were not in the applicable
parameter setting range.
•
Examine and repair motor wiring.
•
Disconnect the machine from the motor and do Rotational Auto-
Tuning again.
Er-08
Rated Slip Error
The motor nameplate data entered during Auto-
Tuning is incorrect.
•
Make sure that the input motor nameplate data is correct.
•
Do Auto-Tuning again and correctly set the motor nameplate
data.
Er-09
Acceleration Error
The motor did not accelerate for the specified
acceleration time.
1.
Increase the value set in
C1-01 [Acceleration Time 1]
.
2.
Disconnect the machine from the motor and do Rotational
Auto-Tuning again.
Er-10
Motor Direction Error
There is defective drive and motor wiring.
Examine and repair motor wiring.
Er-11
Motor Speed Error
The torque reference during acceleration is too high
(100%).
•
Increase the value set in
C1-01 [Acceleration Time 1]
.
•
Disconnect the machine from the motor and do Rotational Auto-
Tuning again.
Er-12
Current Detection Error
There is a phase loss in the drive input power. (U/T1,
V/T2, W/T3)
Examine and repair motor wiring.
Er-13
Leakage Inductance Alarm
The motor rated current value is incorrect.
Correctly set the rated current indicated on the motor nameplate and
perform Auto-Tuning again.