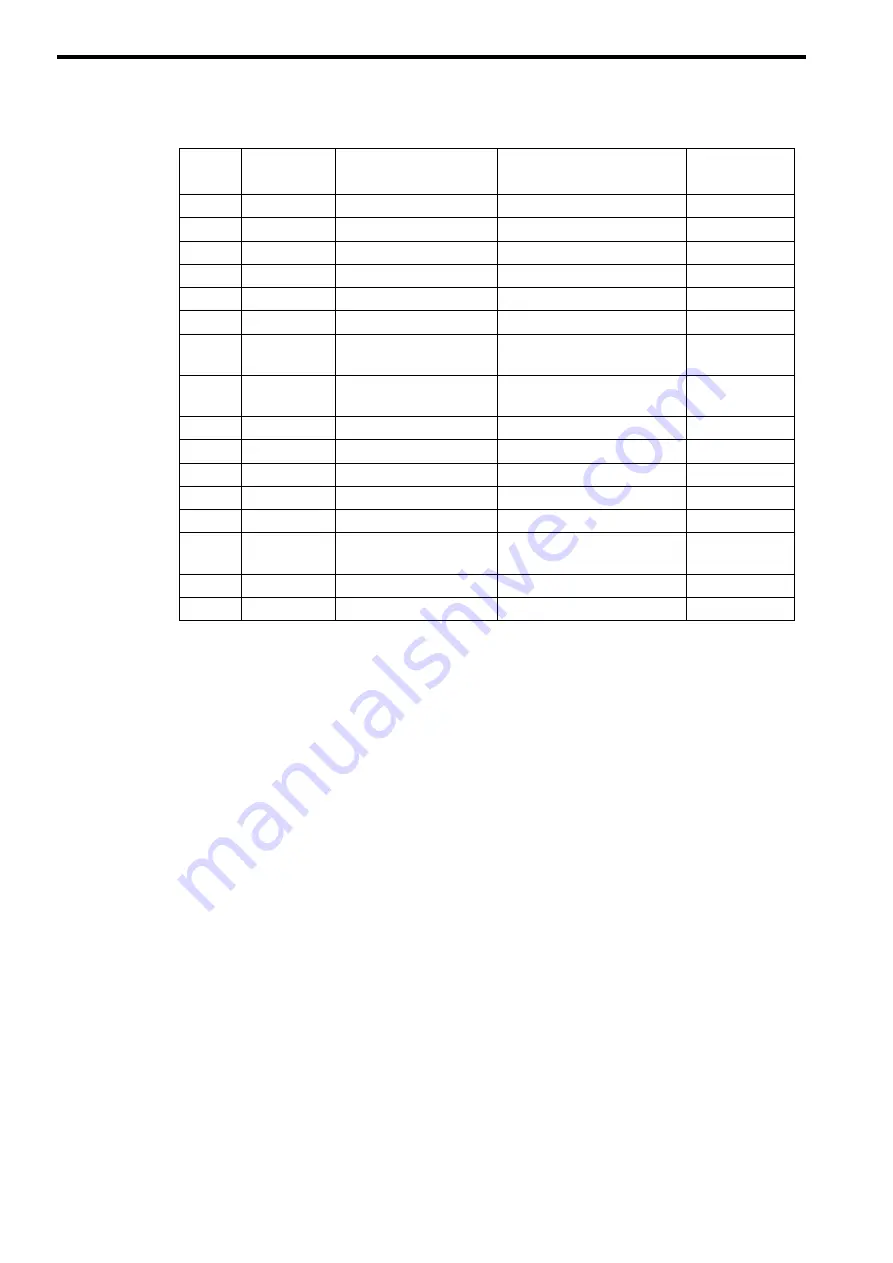
70
Table 15.6 List of YWE-T30D Service Components
Item
No.
Component
Code No.
Component Name
Drawing No. (Model No.)
Specifications
Q'ty per
Welder
021 895662
Printed board set (AC9)
68W9019638 to 640
…
A+B
−
023 T30A0023
Printed board set (IF)
68W3031013-B
…
B
1
024 T30A0024
Printed board set (MB2)
68W3031496
…
A
1
025 911956
Printed board set (DR5)
68W9018715
…
A+B
1
026 911960
Printed board set (MD5)
68W9018712 to 714
…
A+B
1
032 911640
Cicuit board spacer (1)
PCB-10L
20
033 895535
Relay (1)
G2R-2-S DC24V
0K1100034
2
036 895536
Relay (2)
G5V-2 DC24V
0K1110031
1
518 GP430518
Adjustable bushing
J876SG012 0.3m
1
553 T30A0553
Compartment barrier
68W3031324
…
A
1
554 GP430554
Tape No.570S-20
0J8940003
1
632 C-GB-22
Rubber bush
C-GB-22
3
650 DTB30650
Elliptic rubber bush
Grommet for DBC1
3
906 T30A0906
Printed board set (MX)
"68W3031227-B,228-A
…
C
68W3031421
…
A"
1
951 T30A0951
Printed board set (CL)
68W3031490-A
…
B
−
983 895552
Circuit board spacer
PCB-10S
6
Summary of Contents for MOTOWELD-T300D
Page 14: ...14 Fix the gas regulator to prevent it from falling Gas regulator Gas regulator stand...
Page 56: ...56 14 Connection Diagrams 14 1 Connection System Diagram...
Page 59: ...59 15 Lists of Service Components...
Page 60: ...60 Fig 15 1 YWE T30D Front Face Fig 15 2 YWE T30D Rear Face...
Page 63: ...63 Fig 15 3 YWE T30A D 0 Right Side Face Fig 15 3 YWE T30D Right Side Fade...
Page 65: ...65 Fig 15 4 YWE T30D Left Side Face...
Page 67: ...67 Fig 15 5 YWE T30D Base Section...
Page 69: ...69 Fig 15 6 YWE T30D Compartment Barrier Section...