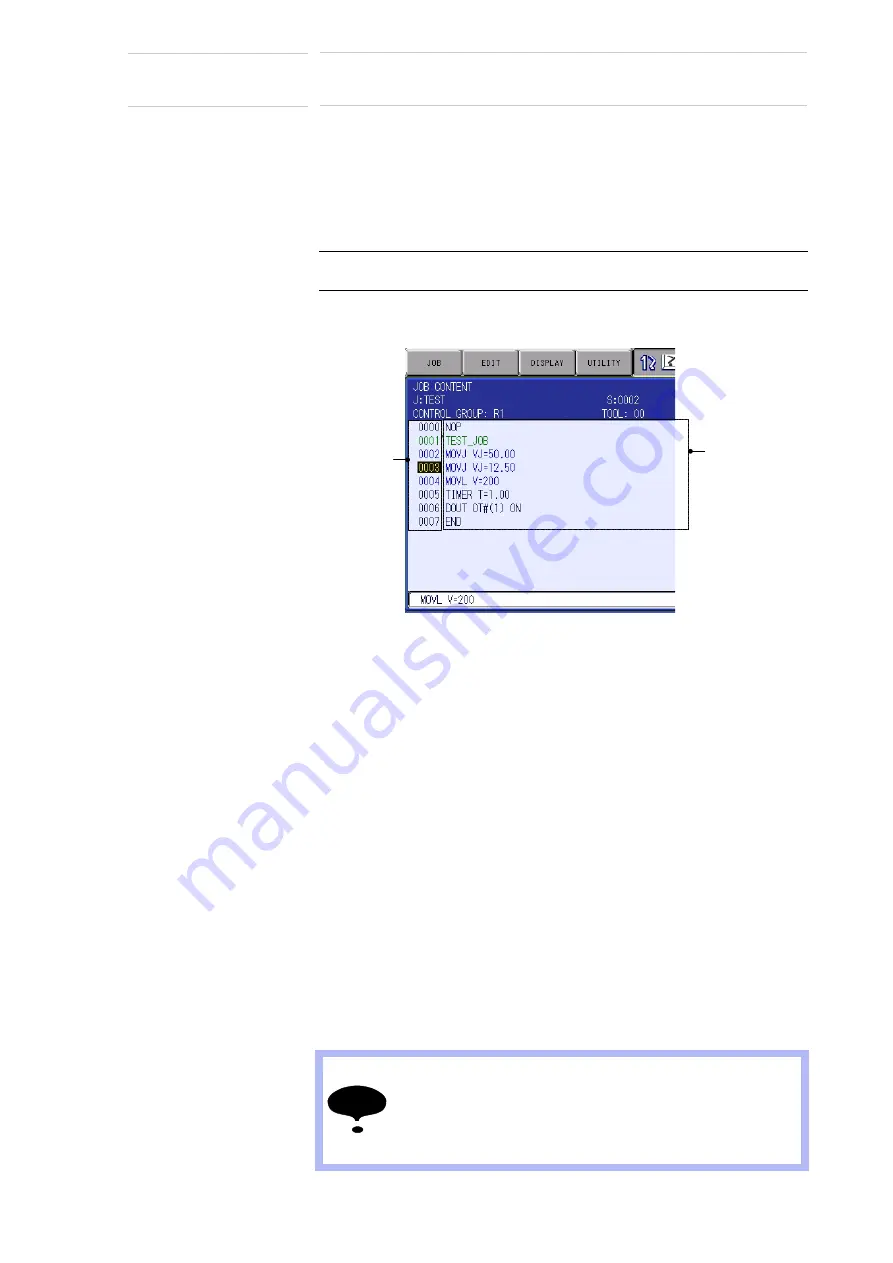
3-1
165553-1CD
HW1482183
3
Teaching
3.1 Registering Instructions
Conveyor Synchronized
Funciton with Shift
Functions
3
Teaching
3.1
Registering Instructions
The instructions can be registered when the cursor is in the address area
on the job content display in teach mode.
3.1.1 SYSTART Instruction
Function
The SYSTART instruction starts the conveyor synchronized control. The
manipulator starts follow-up motion by a move instruction after the
SYSTART instruction, or TIMER or WAIT instruction.
When this instruction is executed, the manipulator stops and waits until
the conveyor current position value exceeds the synchronization start
position value. When the conveyor current position value exceeds the
synchronization start position value, the manipulator starts the follow-up
motion.
When the conveyor current position value exceeds the synchronization
start position value within the tolerance (OL) at the moment the SYSTART
instruction is executed, the manipulator starts the follow-up motion from
the point the SYSTART instruction is executed.
When the conveyor current position value exceeds the synchronization
start position value beyond the tolerance (OL) at the moment the
SYSTART instruction is executed, the system variable $B008 is reset to
“0,” and the manipulator executes the proceeding instruction without the
synchronized motion. At the normal completion, “1” is set to the system
variable $B008.
Select {JOB} under the main menu
Select {JOB CONTENT}
Move
the cursor to the address area
Address area
Instruction area
NOTE
The system variable $B008 cannot be read directly. Copy
the system variable to Bxxx by using a GETS instruction
and read the value.
<Example> GETS B000 $B008
JUMP *NG IF B000<1
43 of 98