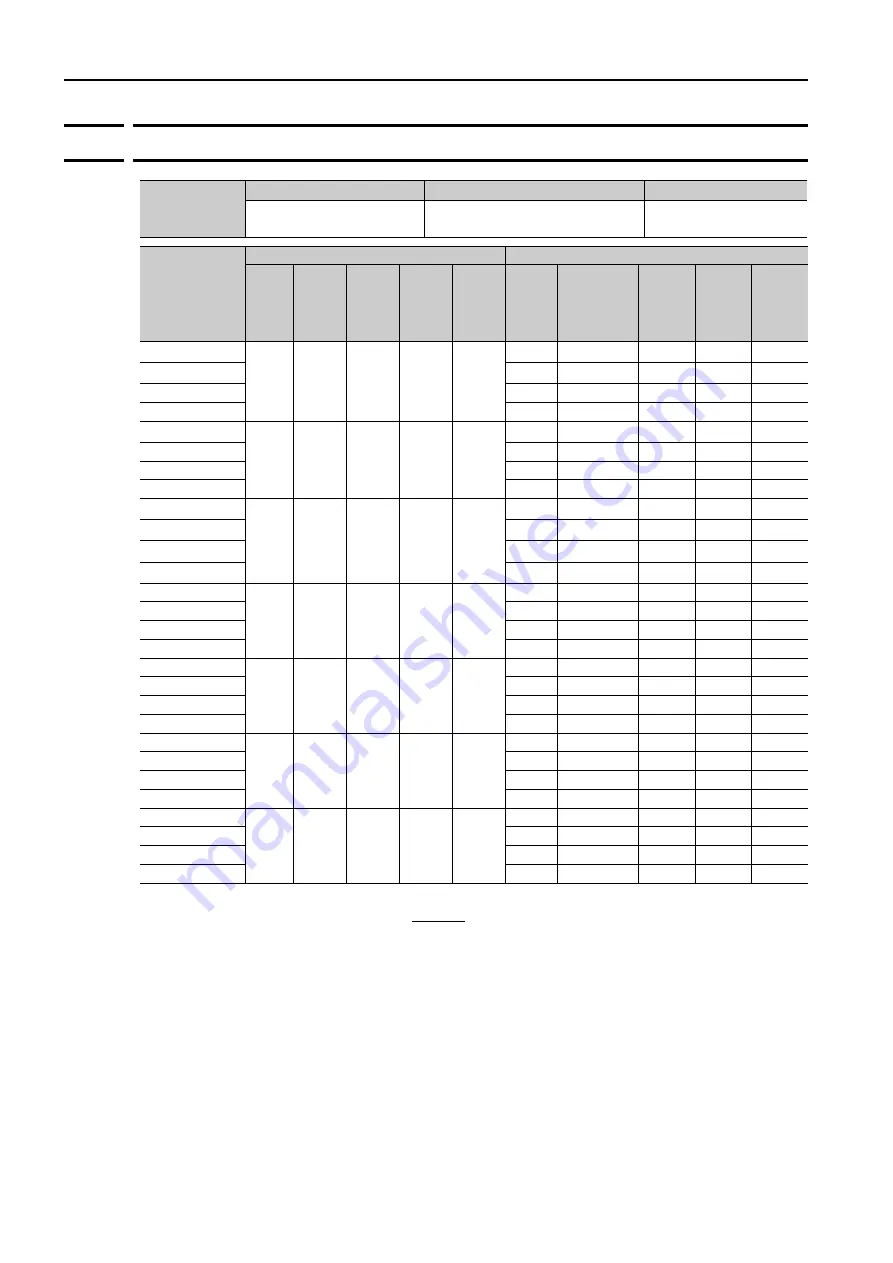
4.2 Specifications and Ratings
4.2.4 Ratings of Servomotors with Gears
4-6
4.2.4
Ratings of Servomotors with Gears
*1.
The gear output torque is expressed by the following formula.
The gear efficiency depends on operating conditions such as the output torque, motor speed, and temperature.
The values in the table are typical values for the rated torque, rated motor speed, and a surrounding air tem-
perature of 25
°
C. They are reference values only.
*2.
When using an SGM7J-A5A, SGM7J-01A, or SGM7J-C2A Servomotor with a gear ratio of 1/5 or an SGM7J-
C2A Servomotor with a gear ratio of 1/11, maintain an 85% maximum effective load ratio. For an SGM7J-C2A
Servomotor with a gear ratio of 1/21 or 1/33, maintain a 90% maximum effective load ratio. The values in the
table take the effective load ratio into consideration.
*3.
The instantaneous maximum torque is 300% of the rated torque.
Note: 1. The gears that are mounted to Yaskawa Servomotors have not been broken in.
Break in the Servomotor if necessary. First, operate the Servomotor at low speed with no load. If no prob-
lems occur, gradually increase the speed and load.
2. The no-load torque for a Servomotor with a Gear is high immediately after the Servomotor starts, and it
then decreases and becomes stable after a few minutes.
This is a common phenomenon caused by grease circulation in the gears and it does not indicate faulty
gears.
3. Other specifications are the same as those for Servomotors without Gears.
All Models
Gear Mechanism
Protective Structure
Lost Motion [arc-min]
Planetary gear mechanism
Totally enclosed, self-cooled, IP55
(except for shaft opening)
3 max.
Servomotor Model
SGM7J-
Servomotor
Gear Output
Rated
Output
[W]
Rated
Motor
Speed
[min
-1
]
Maxi-
mum
Motor
Speed
[min
-1
]
Rated
Torque
[N
⋅
m]
Instanta-
neous
Maxi-
mum
Torque
[N
⋅
m]
Gear
Ratio
Rated Torque/
Efficiency
*1
[N
⋅
m/%]
Instanta-
neous
Maxi-
mum
Torque
[N
⋅
m]
Rated
Motor
Speed
[min
-1
]
Maxi-
mum
Motor
Speed
[min
-1
]
A5A
AH1
50
3000
6000
0.159
0.557
1/5
0.433/64
*2
2.37
600
1200
A5A
AH2
1/9
1.12/78
3.78
*3
333
667
A5A
AHC
1/21
2.84/85
10.6
143
286
A5A
AH7
1/33
3.68/70
15.8
91
182
01A
AH1
100
3000
6000
0.318
1.11
1/5
1.06/78
*2
4.96
600
1200
01A
AHB
1/11
2.52/72
10.7
273
545
01A
AHC
1/21
5.35/80
20.8
143
286
01A
AH7
1/33
7.35/70
32.7
91
182
C2A
AH1
150
3000
6000
0.477
1.67
1/5
1.68/83
*2
7.80 600
1200
C2A
AHB
1/11
3.53/79
*2
16.9
273
545
C2A
AHC
1/21
6.30/70
*2
31.0 143
286
C2A
AH7
1/33
11.2/79
*2
49.7
91
182
02A
AH1
200
3000
6000
0.637
2.23
1/5
2.39/75
9.80 600
1200
02A
AHB
1/11
5.74/82
22.1
273
545
02A
AHC
1/21
10.2/76
42.1 143
286
02A
AH7
1/33
17.0/81
67.6
91
182
04A
AH1
400
3000
6000
1.27
4.46
1/5
5.35/84
20.1 600
1200
04A
AHB
1/11
11.5/82
45.1
273
545
04A
AHC
1/21
23.0/86
87.0 143
286
04A
AH7
1/33
34.0/81
135
91
182
06A
AH1
600
3000
6000
1.91
6.69
1/5
7.54/79
30.5 600
1200
06A
AHB
1/11
18.1/86
68.6
273
545
06A
AHC
1/21
32.1/80
129 143
286
06A
AH7
1/33
53.6/85
206
91
182
08A
AH1
750
3000
6000
2.39
8.36
1/5
10.0/84
38.4 600
1200
08A
AHB
1/11
23.1/88
86.4
273
545
08A
AHC
1/21
42.1/84
163 143
286
08A
AH7
1/33
69.3/88
259
91
182
1
Gear output torque = Servomotor output torque ×
× Efficiency
Gear ratio