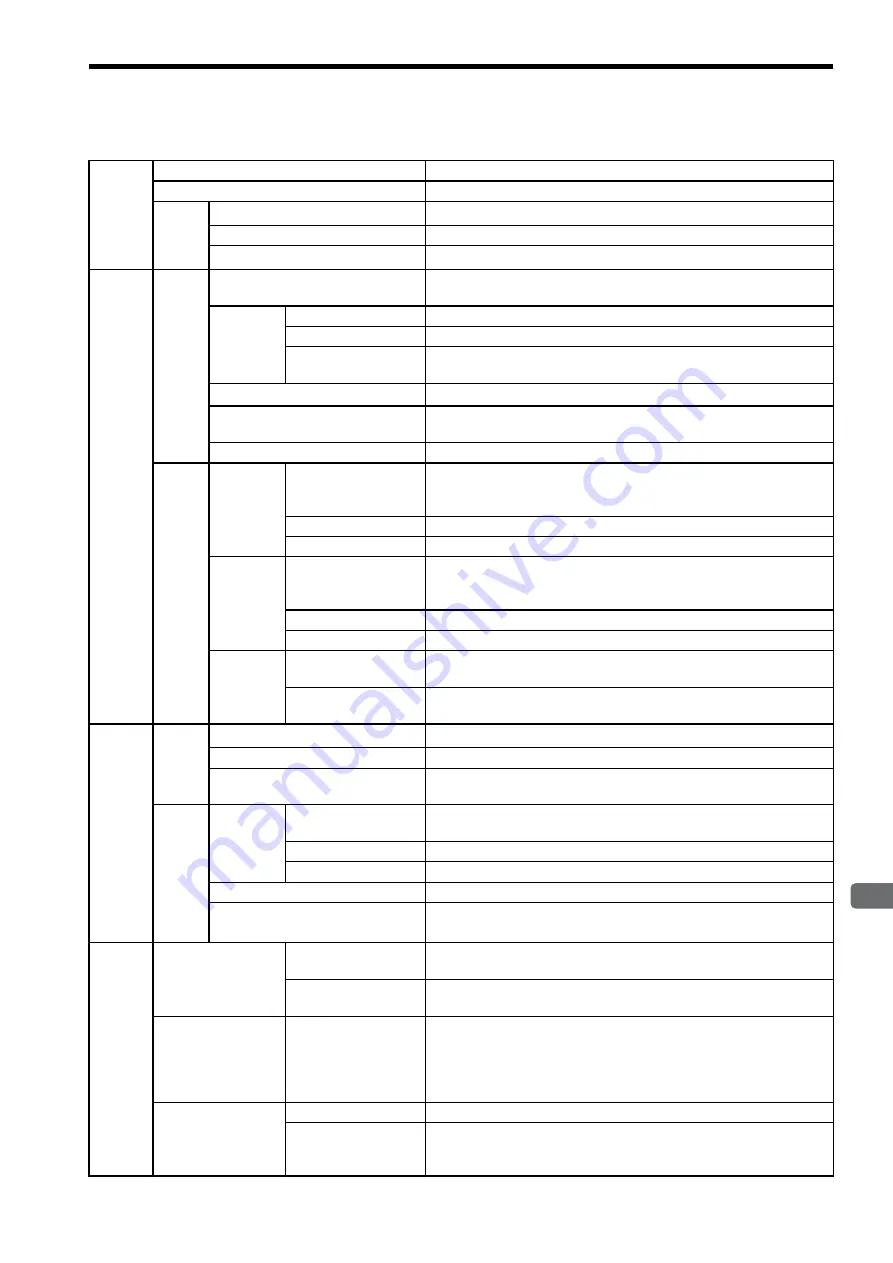
4.1 SERVOPACK Ratings and Specifications
4
SER
VOP
ACK Specifications and Dimensional Drawings
4-3
4.1.3 SERVOPACK Ratings and Specifications
Basic
Specifi-
cations
Control Method
Three-phase full-wave rectification IGBT-PWM (sine-wave driven)
Feedback
Serial encoder: 17-bit (incremental/absolute)
Condi-
tions
Ambient/Storage Temperature
∗
1
0 to +55
°
C/-20 to +85
°
C
Ambient/Storage Humidity
90
%
RH or less (with no condensation)
Vibration/Shock Resistance
4.9 m/s
2
/19.6 m/s
2
Speed
and
Torque
Control
Modes
Perfor-
mance
Speed Control Range
1:5000 (The lowest speed of the speed control range is the speed at which
the servomotor will not stop with a rated torque load.)
Speed
Regula-
tion
∗
2
Load Regulation
0 to 100
%
load:
±
0.01
%
or less (at rated speed)
Voltage Regulation
Rated voltage
±
10
%
: 0
%
(at rated speed)
Temperature Regula-
tion
25
±
25
°
C:
±
0.1
%
or less (at rated speed)
Frequency Characteristics
100 Hz (at J
L
= J
M
)
Torque Control Tolerance
(Repeatability)
±
2
%
Soft Start Time Setting
0 to 10 s (Can be set individually for acceleration and deceleration.)
Input
Signals
Speed
Reference
Input
Reference Voltage
∗
3
±
6 VDC (Variable setting range:
±
2 to
±
10 VDC) at rated speed, input
voltage: maximum
±
12 V (servomotor forward rotation with positive
reference)
Input Impedance
About 14 k
Ω
Circuit Time Constant
About 47
μ
s
Torque
Reference
Input
Reference Voltage
∗
3
±
3 VDC (Variable setting range:
±
1 to
±
10 VDC) at rated torque, input
voltage: maximum
±
12 V (positive torque reference with positive
reference)
Input Impedance
About 14 k
Ω
Circuit Time Constant
About 47
μ
s
Contact
Speed
Reference
Rotation Direction
Selection
With P control signal
Speed Selection
With forward/reverse external torque limit signal (speed 1 to 3 selection),
servomotor stops or another control method is used when both are OFF.
Position
Control
Modes
Perfor-
mance
Bias Setting
0 to 450 min
-1
(setting resolution: 1 min
-1
)
Feed Forward Compensation
0 to 100
%
(setting resolution: 1
%
)
Positioning Completed Width
Setting
0 to 250 reference units (setting resolution: 1 reference unit)
Input
Signals
Reference
Pulse
Type
Sign + pulse train, 90
°
phase difference 2-phase pulse train (phase A +
phase B), or CCW + CW pulse train
Form
Line driver (+5 V level), open collector (+5 V or +12 V level)
Frequency
Maximum 500/200 kpps (line driver/open collector)
Control Signal
Clear signal (input pulse form identical to reference pulse)
Built-in Open Collector Power
Supply
∗
4
+12 V (1k
Ω
resistor built in)
I/O
Signals
Position Output
Form
Phase-A, -B, -C line driver
Phase-S line driver (only with an absolute encoder)
Frequency Dividing
Ratio
Any
Sequence Input
Signal allocation can
be modified.
Servo ON, P control (or Control mode switching, forward/reverse motor
rotation by internal speed setting, zero clamping, reference pulse prohib-
ited), forward run prohibited (P-OT), reverse run prohibited (N-OT),
alarm reset, forward external torque limit, and reverse external torque
limit (or internal speed selection)
Sequence Output
Fixed Output
Servo alarm, 3-bit alarm codes
Signal allocation can
be modified.
Select three signals from the following: Positioning completed (speed
coincidence), servomotor rotation detection, servo ready, torque limit,
speed limit, brake interlock, warning, NEAR signal.
Artisan Technology Group - Quality Instrumentation ... Guaranteed | (888) 88-SOURCE | www.artisantg.com