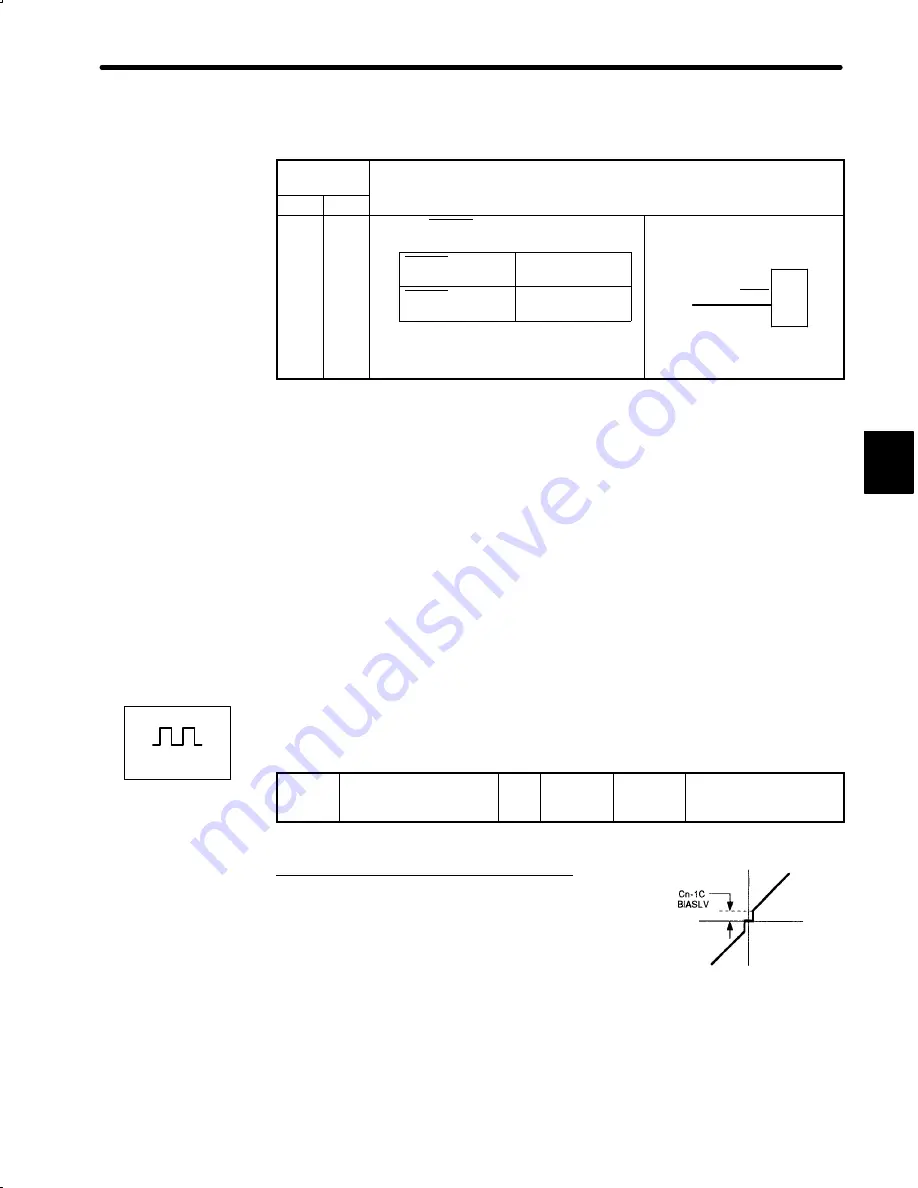
3.6
Minimizing Positioning Time
121
For speed/torque control only.
Cn-01
Setting
Control Mode
Bit B Bit A
Control Mode
D
Signal P-CON (1CN-41) is used to switch
between P control and PI control.
P-CON (1CN-41)
is open (OFF)
PI control
DR2 Servopack
P/PI
0
0
P-CON (1CN-41)
is closed (ON)
P control
P/PI
changeover
P-CON
(1CN-41)
(1CN 41)
D
Torque reference input T-REF (1CN-9)
cannot be used.
2) Proportional control can be used in the following two ways.
a) The host controller can selectively use P control mode for particular conditions only.
This method can prevent the occurrence of overshoot and also shorten settling time.
For particular conditions, refer to
3.6.6 Using Mode Switch
.
b) In the speed control mode, if PI control mode is used when the speed reference has a
reference offset, the motor may rotate at a very slow speed and fail to stop even if 0 is
specified as a speed reference. In this case, use P control mode to stop the motor.
3.6.5 Setting Speed Bias
The settling time for positioning can be reduced by assigning bias to the speed reference out-
put part in the Servopack. To assign bias, use the following constant.
Cn-1C
BIASLV
Bias
Unit:
r/min
Setting
Range: 0
to 450
Factory
Setting: 0
For Position Control
Only
This user constant is for position control only.
This user constant is set to assign an offset to a
speed reference in the DR2 Servopack.
Use this constant to shorten settling time.
Set this user constant according to machine conditions.
3
Positions
Internal speed
reference
Error pulse