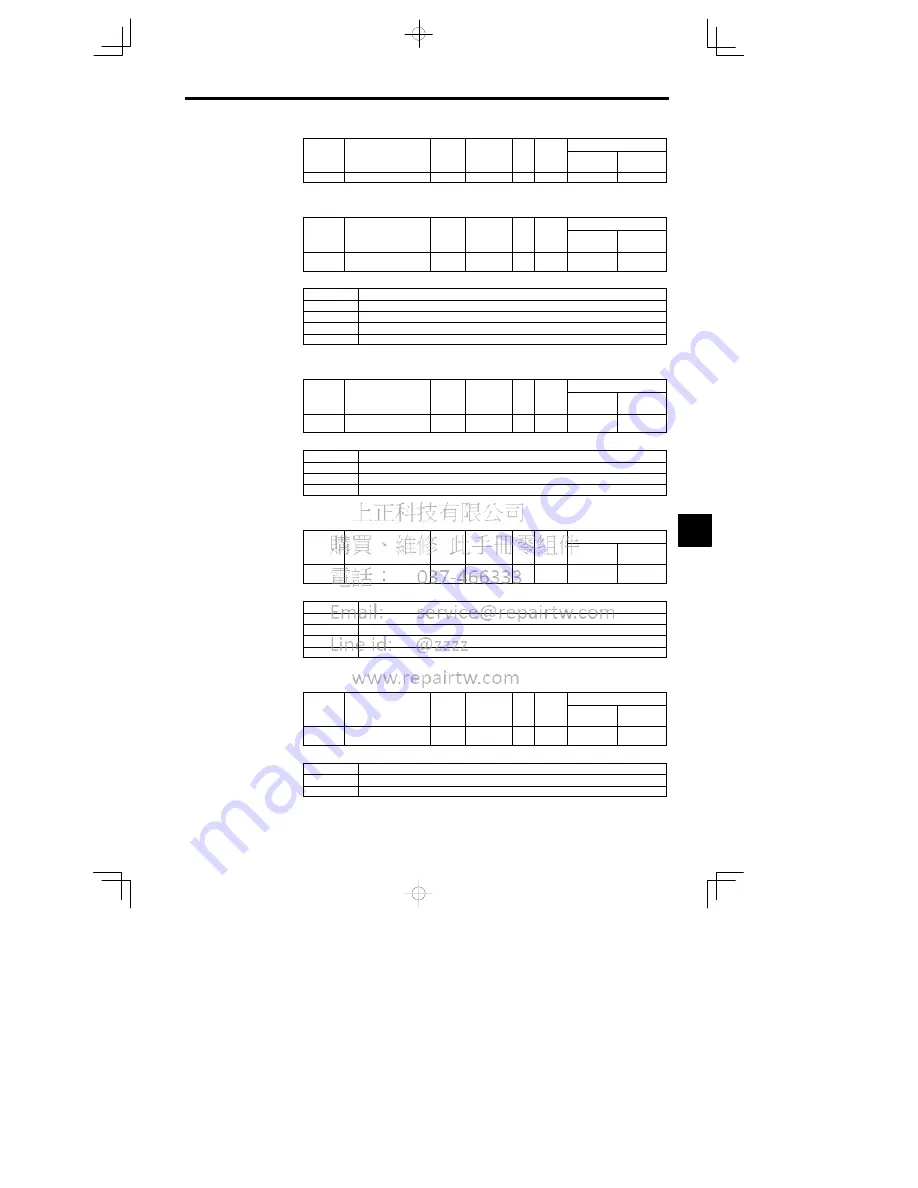
7.3
Common Functions
- 47
User
Change
during
Setting
Factory
Valid Access Levels
User
Constant
Number
Name
during
Opera-
tion
Setting
Range
Unit
Factory
Setting
Open Loop
Vector
Flux Vector
H5-01
Station address
0 to 20
--
1F
A
A
Baud Rate: H5-02
D
Set the baud rate for MEMOBUS communications.
User
Change
during
Setting
Factory
Valid Access Levels
User
Constant
Number
Name
during
Opera-
tion
Setting
Range
Unit
Factory
Setting
Open Loop
Vector
Flux Vector
H5-02
Communication speed
selection
0 to 3
--
3
A
A
D
Settings
Setting
Baud Rate
0
1200 bps
1
2400 bps;
2
4800 bps
3
9600 bps
Communication Parity: H5-03
D
Set the parity for MEMOBUS communications.
User
Change
during
Setting
Factory
Valid Access Levels
User
Constant
Number
Name
during
Opera-
tion
Setting
Range
Unit
Factory
Setting
Open Loop
Vector
Flux Vector
H5-03
Communication parity
selection
0 to 2
--
0
A
A
D
Settings
Setting
Function
0
No parity
1
Even parity
2
Odd parity
Stopping Method after Communications Error: H5-04
D
Set the stopping method to used after a communications error is detected.
User
Change
during
Setting
Factory
Valid Access Levels
User
Constant
Number
Name
during
Opera-
tion
Setting
Range
Unit
Factory
Setting
Open Loop
Vector
Flux Vector
H5-04
Stopping method after
communication error
0 to 3
--
3
A
A
D
Settings
Setting
Function
0
Deceleration to stop (deceleration time:C1-02)
1
Coast to stop
2
Emergency stop (deceleration time:C1-09)
3
Continue operation (display only)
Communications Error Detection: H5-05
D
Set whether or not to detect a communications timeout as a communications error.
User
Change
during
Setting
Factory
Valid Access Levels
User
Constant
Number
Name
during
Opera-
tion
Setting
Range
Unit
Factory
Setting
Open Loop
Vector
Flux Vector
H5-05
Communication error
detection selection
0 1
--
1
A
A
D
Settings
Setting
Function
0
Do not detect as communications error.
1
Detect as communications error.
7