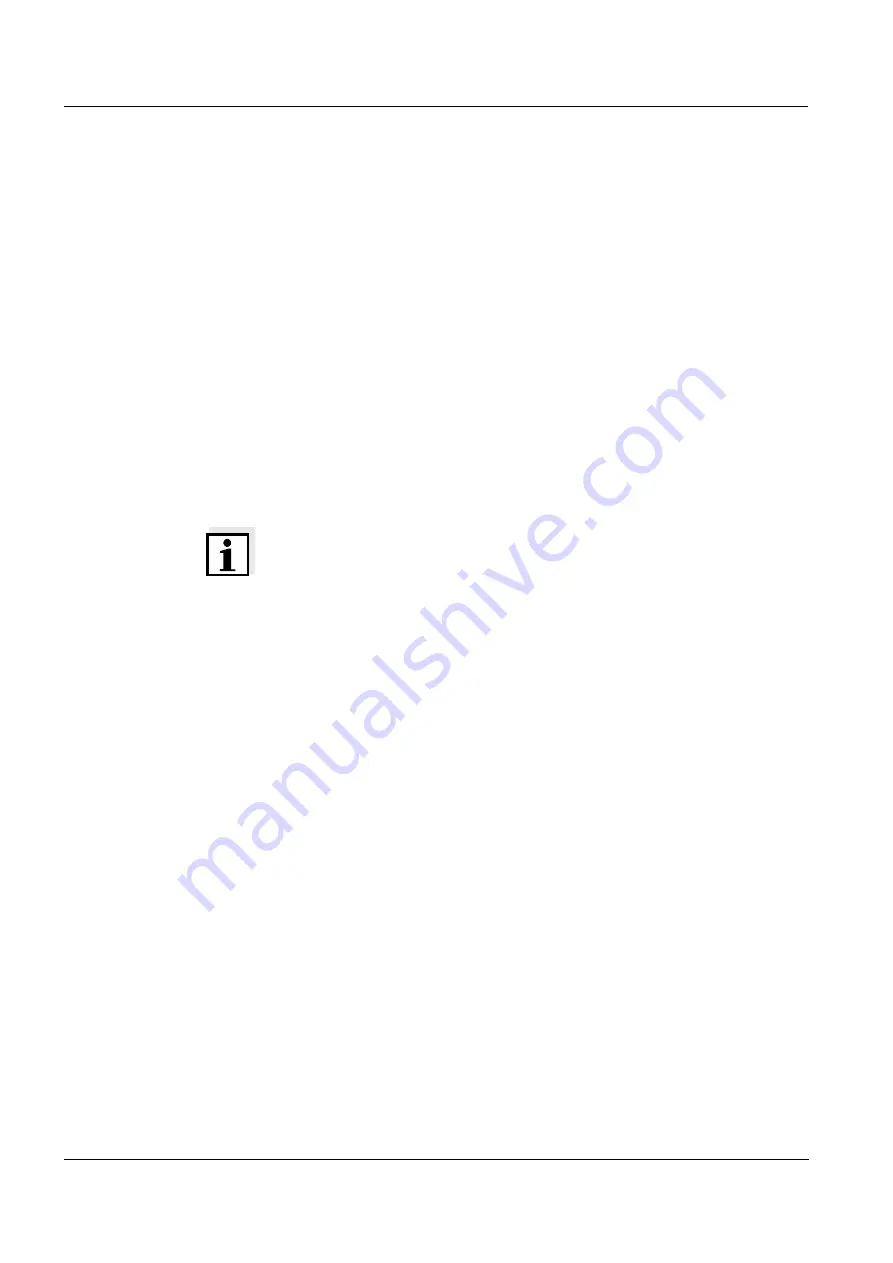
Measuring / Operation
TriOxmatic
®
700 (SW)
54
ba25307e06
07/2015
4.2
Calibration
4.2.1
General information on calibration
Why calibrate?
During the operation of a D.O. sensor, the slope of the D.O. sensor
changes with time. The calibration procedure determines the current
slope of the sensor.
When to calibrate?
Calibrate before measuring and at regular intervals (depending on the
application).
Calibration procedure,
Ideally, calibration takes place in water vapor-saturated air. To do so,
position the sensor approx. 2 cm above a water surface, for example in
a narrow bucket or similar container with water.
In the case of air temperatures under 5 °C we recommend to calibrate
not in air but in air-saturated water that has a higher temperature. You
obtain air-saturated water by pouring water several times in and out of
two vessels so that it sparkles.
Note
For calibration the membrane always has to be clean, for calibration in
air it has to be dry. Clean contaminated sensors before calibration (see
section 5.2 C