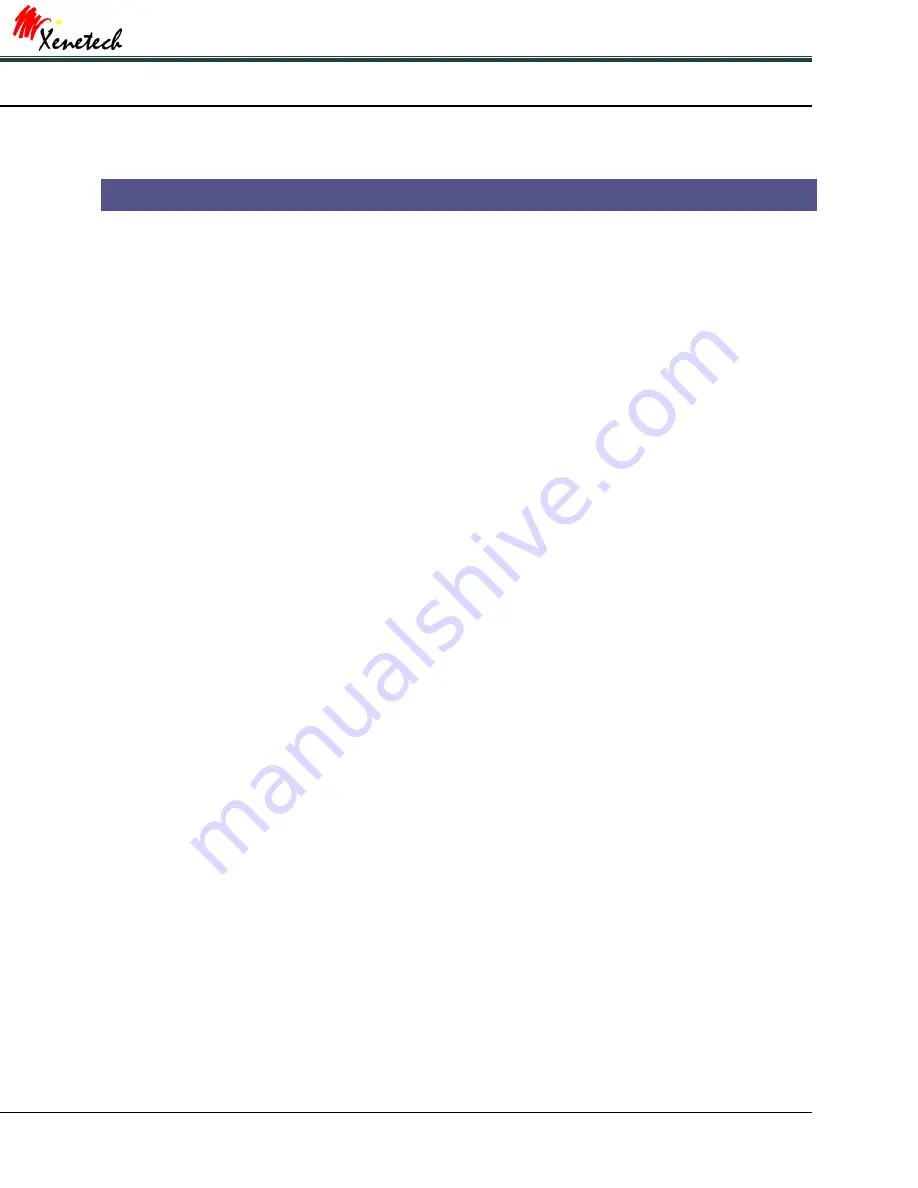
Xenetech Duo 1218 Installation & Table Manual
43
APPENDIX A
HIGH PRESSURE BELT - DRIVE BLOWERS
High pressure belt-drive blowers are outdoor mounted units that usually contain a radial blade fan driven by an
electric motor. They are intended to go outside and are supplied with a weatherproof cover. These industrial
grade units are designed to provide continuous high airflow at relatively high static pressures. This insures that
you will have sufficient airflow through the laser cabinet, and run of pipe, to the outdoors. The laser cabinet and
pipe restricts the flow of air through the blower. Therefore, the use of a blower that is rated to perform at
relatively high static pressures is critical. The system must include a scheme for piping to the outside that is
thought out, and sized properly. The efficiency of the system is based on several factors which HVAC professionals
will easily understand. The key points are as follows:
26.
The laser should ideally be positioned
as close to an outside wall as possible
thus reducing the
length of the pipe run, and the elbows (bends) that the pipe will make.
20.
Only
smooth wall tubing
(PVC or metal) should be used.
21.
All
joints
should be sufficiently
sealed
to minimize leakage.
22.
These blowers are loud (3/4 HP Motor unit = 86 dBA @ 5 ft.) so do not mount them under a window, or in
a location that may adversely effect a neighbor in close proximity to you. This is more of an issue when
the units are on the ground, and less so when units are mounted close to the center of a roof.
23.
Blowers may be mounted on a
roof, or pad mounted
on the ground.
24.
Mount the blower up on a
base
(pressure treated wood works great) to prevent quantities of ice, snow or
rainwater from affecting the blower. On the ground a cement pad is also suitable.
25.
The use of
vibration isolators
is recommended for roof mount installations in order to absorb noise and
minimize the transfer of vibration from the blower to the structure.
26.
Near the connection to the laser a
reducer
should be utilized to drop the pipe size (from the size used for
the run length, example 6-inch) to 4 inches necessary for connection to the laser.
27.
A
blast gate
(also called a shut off gate) should be utilized near the connection to the laser. This allows
you to close off airflow through the system.
28.
A
wire mesh screen
should be included in the system (some blast gates include this) to prevent small
objects from being pulled through the pipe to the blower. The screen should be located as close as
possible to the hose that connects the laser to the pipe system. In the unlikely event that a small object
is pulled through the system it will go no further than the screen allowing easy retrieval.
29.
A
flexible hose
(not PVC or metal) should be used to connect the blower to the run of pipe. This prevents
any vibration from transferring from the blower to the pipe run. This method of connecting to the rigid
pipe is also done at the connection to the laser.
30.
Blowers are connected to the Xenetech laser allowing for the automatic starting and stopping of the
blower through a relay. This relay is packaged inside the Xenetech auxiliary box. The blower will
automatically be energized whenever a job is sent to the laser, and de-energized when the current job
finishes. A user adjustable delay can be set in the laser menu which forces the blower to stay on for a set
time after a job is completed, guaranteeing that the cabinet is completely evacuated of smoke and
residue. For the electrician, the relay in the Xenetech auxiliary box is rated at 10 amperes. The electrician
should wire a
contactor
in line with the Aux. box that has the proper rating for use with the blower (15 or
20A @ 115V / 60 Hz). The wiring that runs from the contactor to the Xenetech aux. box will need to
terminate in a standard male 3-prong plug. This plug will in turn connect to the female 3-prong
receptacle at the aux. box provided by Xenetech. The
dedicated circuit supplying the blower
must include
a circuit breaker size consistent with the requirements for the blower's electric motor. These
specifications are included with the blower. The laser and the aux. box use a standard 3-prong male plug