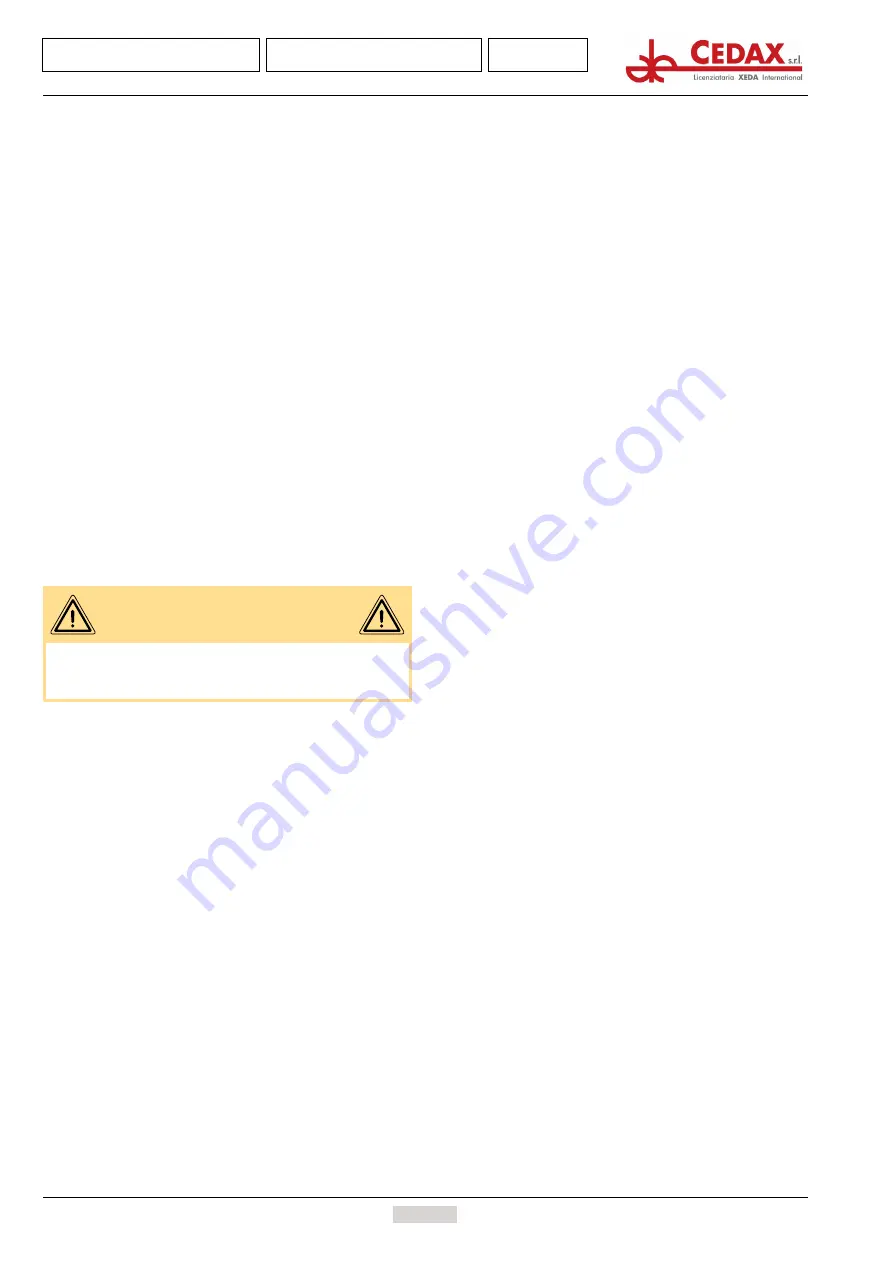
EWV
- 36 -
TRANSPORTATION AND
HANDLING
ELECTROFOG
4.3
STORAGE AND WAREHOUSING
METHODS
- Upon receipt of the material, the purchaser must
prepare a suitable area in which to store the
packages.
- To prevent the packages from creating a hazard
or degrading, the storage area must be covered
(preferably a closed environment to avoid contact
with atmospheric agents) and accessible only to
operators.
- In addition to having a stable support surface and
adequate load-bearing capacity, the storage area
must be free from risk of fire and/or explosion,
must have adequate humidity and temperature
(between -25°C and +55°C) and sufficient lighting.
We recommend designating a storage area in the
immediate vicinity of the installation area to ensure
minimum movement during the installation phase of
the machine.
- For as long as the machine remains inactive after
unpacking, pending commissioning or due to
production interruptions, it must be protected with
tarpaulins to prevent dust from depositing on the
mechanisms.
ATTENTION
In the event of prolonged storage, periodically
check that there are no changes in the storage
conditions of the packages.
Summary of Contents for CEDAX ELECTROFOG EWV8
Page 14: ...EWV 12 INTRODUCTION ELECTROFOG Page intentionally left blank...
Page 18: ...EWV 16 GENERAL INFORMATION ELECTROFOG Page intentionally left blank...
Page 24: ...EWV 22 TECHNICAL INFORMATION ELECTROFOG Page intentionally left blank...
Page 36: ...EWV 34 SAFETY ELECTROFOG Page intentionally left blank...
Page 40: ...EWV 38 TRANSPORTATION AND HANDLING ELECTROFOG Page intentionally left blank...
Page 44: ...EWV 42 INSTALLATION ELECTROFOG 1 4 5 1 4 3 6...
Page 46: ...EWV 44 INSTALLATION ELECTROFOG Page intentionally left blank...
Page 52: ...EWV 50 USING THE MACHINE ELECTROFOG Page intentionally left blank...
Page 58: ...EWV 56 PROBLEMS CAUSES AND REMEDIES ELECTROFOG Page intentionally left blank...
Page 60: ...EWV 58 DEMOLITION AND DISPOSAL ELECTROFOG Page intentionally left blank...
Page 62: ...EWV 60 WARRANTY ELECTROFOG Page intentionally left blank...
Page 63: ...EWV 61 ANNEX 1 ELECTROFOG 11 ANNEX 1 List of usable products...
Page 64: ...EWV 62 ANNEX 1 ELECTROFOG Page intentionally left blank...
Page 65: ...EWV 63 ANNEX 2 ELECTROFOG 12 ANNEX 2 Authorised companies...
Page 66: ...EWV 64 ANNEX 2 ELECTROFOG Page intentionally left blank...
Page 67: ...EWV 65 ANNEX 3 ELECTROFOG 13 ANNEX 3 Wiring diagram...
Page 68: ...EWV 66 ANNEX 3 ELECTROFOG Page intentionally left blank...
Page 69: ...EWV 67 ANNEX 4 ELECTROFOG 14 ANNEX 4 Declaration of Conformity...
Page 70: ...EWV 68 ANNEX 4 ELECTROFOG Page intentionally left blank...
Page 71: ...EWV 69 NOTES ELECTROFOG...
Page 72: ...EWV 70 NOTES ELECTROFOG...
Page 73: ...Page intentionally left blank...
Page 74: ...Via F Guarini 15 I 47121 Forl FC Italy Tel 39 0543 780600 Fax 39 0543 473018...
Page 77: ...REV1 0 ALLEGATO 3 ANNEXE 3 ANNEX 3 CEDAX ELECTRIC DRAWING SCHEMA ELETTRICO SCHEMA ELECTRIQUE...
Page 78: ...REV1 0 CEDAX...
Page 79: ...REV1 0 CEDAX mm min...
Page 80: ...REV1 0 CEDAX...
Page 81: ...REV1 0 CEDAX...
Page 82: ...REV1 0 CEDAX...
Page 83: ...REV1 0 CEDAX...
Page 84: ......