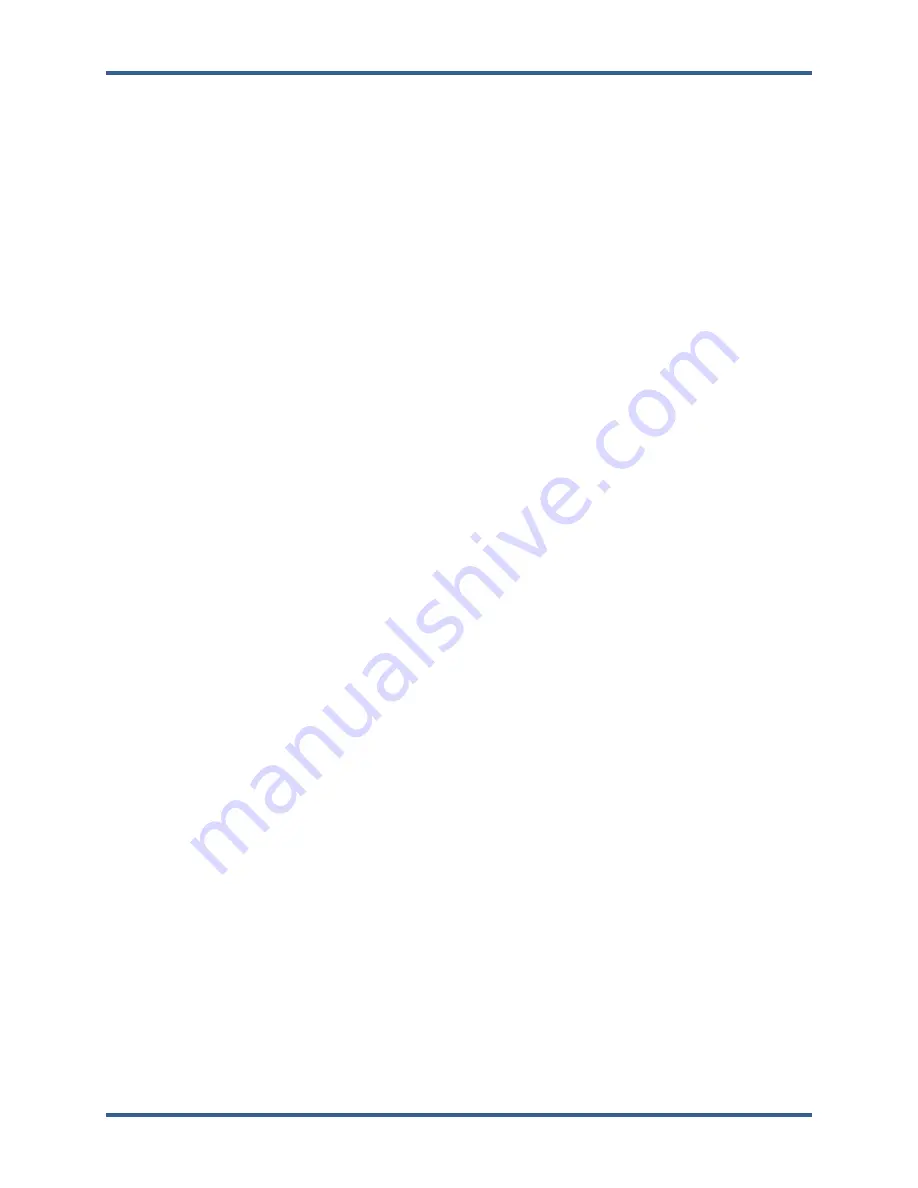
Manual 26694
2301E-ST
Woodward
82
13.
Process Control
Process Control
The process control can be configured to control any system process,
related to or affected by turbine speed or load. Typically this controller is
used as a turbine inlet or exhaust pressure controller. The process control
is a PID controller that compares a 4–20 mA process signal with the
process setpoint. The PID controller sets the speed controller setpoint until
the process signal and the setpoint match. The process setpoint is
adjustable with raise or lower contact inputs, or the communication links. In
addition, a remote process setpoint analog input can be programmed to
remotely position the cascade setpoint.
Process Control Example:
1.
Let’s take for example that we want to control the turbine exhaust
pressure with a transducer range of 0–100 psi (0–690 kPa).
2.
The generator is tied to the utility bus in droop, so as the process
changes, the load will change.
3.
Here are the variables that need to be set:
a) Under the Service menu P**ANALOG I/O SETTINGS**.
02 INPUT #1 MIN VALUE (UNITS) = 0 psi (0 kPa)
03 INPUT #1 MAX VALUE (UNITS) = 100 psi (690 kPa)
b) Under the Service menu H**PROCESS CONTROL**:
05 MIN PROC SETPNT (UNITS) = 0 psi (0 kPa)
06 MAX PROC SETPNT (UNITS) = 100 psi (690 kPa)
08 SETPT INIT VALUE (UNITS) = 60 psi (414 kPa)
09 SPEED SETPT LOW LIMIT = 3610 rpm
10 SPEED SETPT HIGH LIMIT = 3780 rpm
c) Under the Service menu F**REMOTE SPEED CONTROL **:
02 RMT/PROC CNTRL SLOW RATE (RPM/S) = 5
d) Under the Configure menu D**ANALOG INPUT OPTIONS**:
02 SEL AI#1 FUNCTION (1-7) = 7 (Process Signal)
03 SEL AI#1 TYPE (1-4) = 1 (4–20 mA)
08 USE INPUT #1 FAIL TRIP = Optional
e) Under the Configure menu C**DISCRETE INPUT OPTIONS**:
02 SEL DI F FUNCTION (1-6) = 6 (Process Enable)
4.
This is just a partial list of the variables needed to run the turbine, the
variable listed here pertain just to the Process Control.
5.
With the turbine running at synchronous speed and the breaker
closed to the utility bus in droop mode, enable the process control.
The load will change to control the exhaust pressure at 60 psi (414
kPa).
6.
Adjust the ramp rates, deadband, and PID Dynamic adjustments for
the proper operation and stability of the turbine and process.
14. Power
System
Management
Concepts
This section provides a summary review of droop, isochronous,
droop/isochronous, and isochronous load sharing operating concepts.
These concepts provide an understanding for power management.
Paralleling
There are two basic methods used for paralleling: droop, where speed
decreases with load increase and isochronous, where speed remains
constant with load increase. The paralleling system shown in Figure 4-6
consists of a load matching circuit and kW sensor circuitry.
Released
Summary of Contents for 2301E-ST
Page 15: ...Manual 26694 2301E ST Woodward 13 Figure 2 1a 2301E ST Outline Drawing 8273 1013 1014 Released...
Page 17: ...Manual 26694 2301E ST Woodward 15 Figure 2 2a 2301E ST Plant Wiring Diagram sheet 1 Released...
Page 18: ...Manual 26694 2301E ST Woodward 16 Figure 2 2b 2301E ST Plant Wiring Diagram sheet 2 Released...
Page 19: ...Manual 26694 2301E ST Woodward 17 Figure 2 2c 2301E ST Plant Wiring Diagram notes Released...
Page 125: ...Manual 26694 2301E ST Woodward 123 Declarations Released...