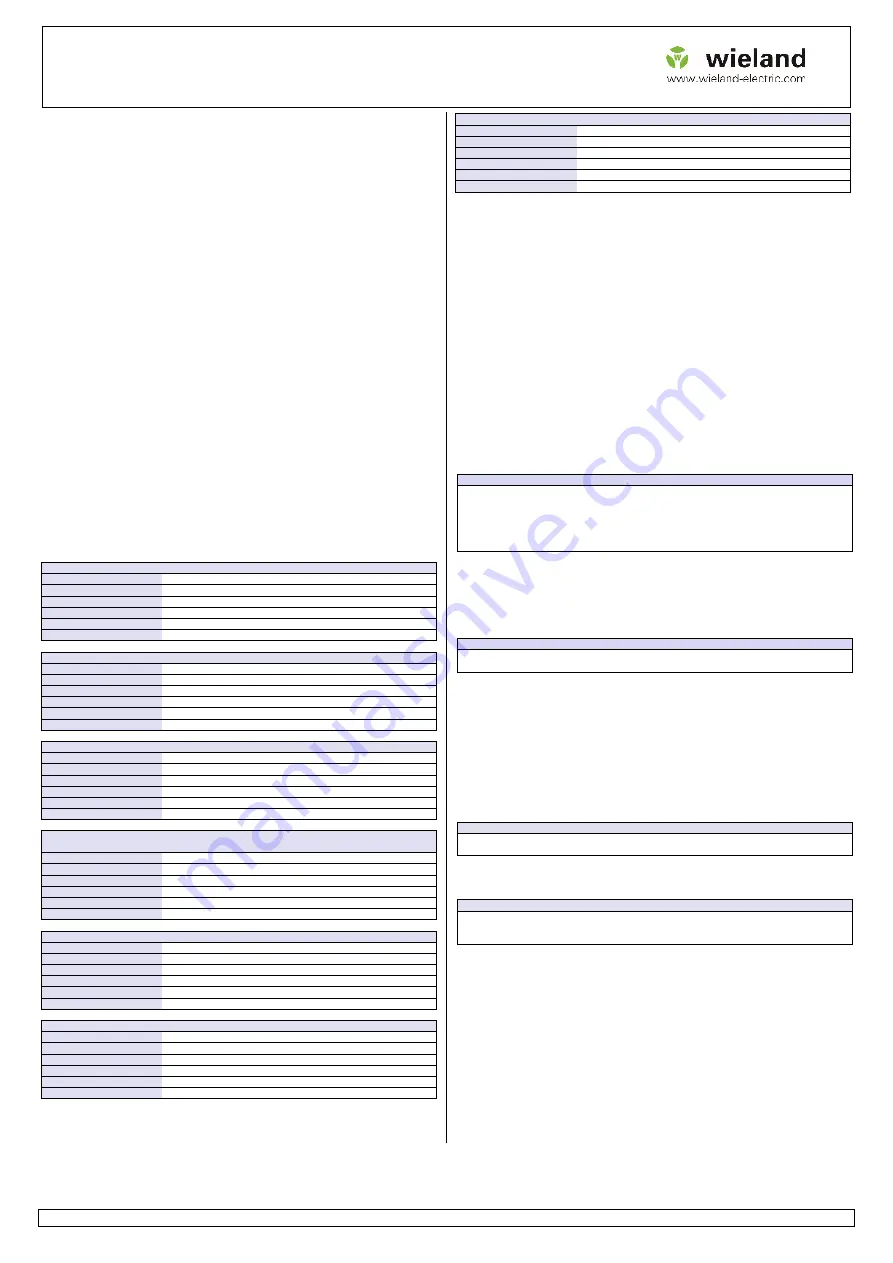
Installation instructions (translation from original)
sensor
PRO
STS
Art.Nr. R1.400.xxxx.0
Touchless safety sensor with coding
Wieland Electric GmbH
Brennerstrasse 10-14
96052 Bamberg
Tel.: +49 (951) 9324-0
Fax: +49 (951) 9324-198
Internet: www.wieland-electric.com
Email: [email protected]
Doc. #
BA001027
- 08/2017 (Rev.C)
sensor
PRO
STS
EN / 5
7.3 Safety inputs
The safety sensor has 2 safety inputs:
•
Connect the safety inputs of +24 V DC for single use of the sensor.
•
When using the sensor in a series circuit, the safety inputs of the first sensor can be
connected to +24 V DC. The safety inputs of the following sensors are connected to the
safety outputs of the previous sensor. Please also refer to chapter 10.1 "Series
connection".
•
Pulses with a duration of max. 900
μ
s are tolerated on the safety inputs.
Wiring examples can be found in chapter 17.4 "Connection Examples"
.
7.4 EDM-input
The EDM input can be configured as "automatic" or "monitored" (see number key). If the
EDM input is not required, the "automatic" variant must be selected and connected to +24 V
DC.
EDM-input: automatic
For contactor monitoring, the open contactors must be connected to the EDM input. For
series connection of multiple sensors all EDM inputs must be connected to +24 V DC. The
monitor for the contactors must be connected to the last sensor of the chain.
Wiring examples can be found in chapter 17.4 "Connection Examples"
.
EDM-input: monitors (start button)
Connect the EDM input to an external start button on your machine control. The EDM input is
only then recognized as set properly if after pressing the sensor and after setting the safety
inputs at least one valid start pulse is detected. The valid start pulse is detected when after a
rising edge, a falling edge within the allowable start pulse duration between 30 ms and 5 s is
detected.
Wiring examples can be found in chapter 17.4 "Connection Examples".
7.5 Diagnostic output
The diagnostic output is positive switching, short-circuit protected and transmits the various
sensor states with different signals, for example, to a
sensor
PRO
STS
.The pulsed signals
corresponding to the respective timing of the LED. The various symbols are described in more
detail under chapter 7.6.
7.6 LED displays, flash codes and clocking diagnostic output
Sensor non-actuated
LED green
off
LED red
off
LED yellow
on
Diagnostic output
0 V
Safety outputs OSSD
0 V
Note
Voltage is applied
Actuator in the detection area (sensor activated), all inputs correctly set
LED green
on
LED red
off
LED yellow
off
Diagnostic output
24 V DC
Safety outputs OSSD
24 V
Note
Actuator in the detection area
Actuator in the detection area (sensor actuated), safety inputs not set (low level)
LED green
flashes
(1)
LED red
off
LED yellow
off
Diagnostic output
24 V DC
Safety outputs OSSD
0 V
Note
set safety inputs
Actuator in the detection area (sensor actuated), safety inputs set (high level), waits for
start pulse
LED green
Rapid flashing
(2)
LED red
off
LED yellow
off
Diagnostic output
24 V DC
Safety output OSSD
0 V
Note
press start button
Actuator in the boundary area
LED green
off
LED red
off
LED yellow
flashes
(1)
Diagnostic output
24 V DC clocked
Safety outputs OSSD
Previous state
Note
Readjust sensor
Teach-in process
LED green
off
LED red
off
LED yellow
Rapid flashing
(2)
Diagnostic output
24 V DC clocked
Safety outputs OSSD
0 V
Note
Disconnect voltage to complete teach-in
Fault condition
LED green
off
LED red
flashes
(1)
LED yellow
off
Diagnostic output
0 V
Safety outputs
0 V
Note
See chapter 13 "Troubleshooting"
(1)
Flashing: The pulse interval (1 s) of the LED ratio is 1:1.
(2)
Rapid flashing: The pulse interval (0,25 s) of the LED ratio is 1:5.
7.7 Boundary area monitoring
If the actuator is in the boundary area of the switching distances with corresponding offset
values of the sensor, it is transmitted to a
sensor
PRO
STS
or indicated by the LED (see
chapter 7.6 "LED displays, flash codes and clocking diagnostic output").
8
Assembly
•
Safety sensor and actuator
−
Do not use as a stopper
−
External fields can affect switching distances
•
Installation of the safety sensor and the associated actuator is allowed only when de-
energized.
•
Make sure that the markings on the sensor and actuator face each other congruently.
•
The mounting position is arbitrary. However, security sensor and actuator must be mounted
parallel and opposite each other.
•
Note the specified installation tolerances and the approved control options.
To ensure trouble-free operation and to avoid any impact on the operating distance, the
following points should be noted:
•
In order to guarantee the specified switching distance, the free zone (environment free of
electrically and magnetically conductive materials) must be adhered to.
N O T E
•
Matching space plates for mounting on metal parts are available under the order-Nb.
•
R1.100.4100.0 Quader 8 mm
•
R1.100.4101.0 Quader 10 mm
•
R1.100.4200.0 Rechteck 8 mm
•
R1.100.4201.0 Rechteck 10 mm
•
Available at Wieland Electric GmbH
•
The mounting distance between two systems of the safety sensor and actuator must be
min. 15 cm.
•
Attach safety sensor and actuator to the protective device so that they cannot be removed.
•
Use only M4 screws with flat head (e.g. M4 cheese head screws ISO 4762) for installation
of the safety sensor and actuator. Tightening torque max. 0,5
−
0.7 Nm. Use non-
ferromagnetic material (e.g. brass) screws.
N O T E
•
We recommend using the screw covers included to secure the mounting screws against
easy disassembly.
•
The safety sensor must be mounted on flat surfaces.
•
The connecting cable of the safety sensor must be protected against mechanical damage.
•
Consider the requirements of EN ISO 14119 during installation.
•
Also consider the requirements of EN 60204-1, in particular regarding the proper laying of
cable. It is recommended to lay the sensor cable so that it is covered.
9
Adjustment
The stated operating distances (see chapter 17 "Technical Specifications") are only valid for
mounting on non-metallic material if the safety sensor and actuator are mounted in parallel
opposite each other. Other arrangements may lead to different switching states.
10
Electrical Connection
C A U T I O N
•
The electrical connection may only be carried out with the power off and by authorized
personnel.
•
Connect the safety sensor according to the specified wire colors and pin assignment (see
chapter 17.1 "Circuit diagram and pin assignment").
C A U T I O N
•
Both safety outputs must always be evaluated to ensure safety.
•
Since the diagnostic output is not a safety output, it may not be used for safety-relevant
information and monitoring functions.
•
Make sure that the required minimum input voltage of the downstream safety evaluation
unit is not undershot. Observe the voltage drop at the safety sensor and the connecting
cable.
10.1 Series connection
The safety sensors enable a series circuit with up to 30 sensors while achieving PLe with
correct wiring. For a series circuit it must be noted that the time delay accumulates for each
additional sensor. The relevant technical specifications can be found in chapter 17 "Technical
Data". Configuration EDM input see chapter "7.4 EDM input".
10.2 Information about power supply
•
The sensor must be powered directly or indirectly with a SELV/PELV power supply.
•
For use and applications as per the requirements
1)
, the power supply must be classified "for
use in class 2 circuits".
1)
Notice regarding the scope of the UL approval: The devices have been tested in accordance with the
requirements of UL508 and CSA/C22.2 no. 14 (protection against electric shock and fire).