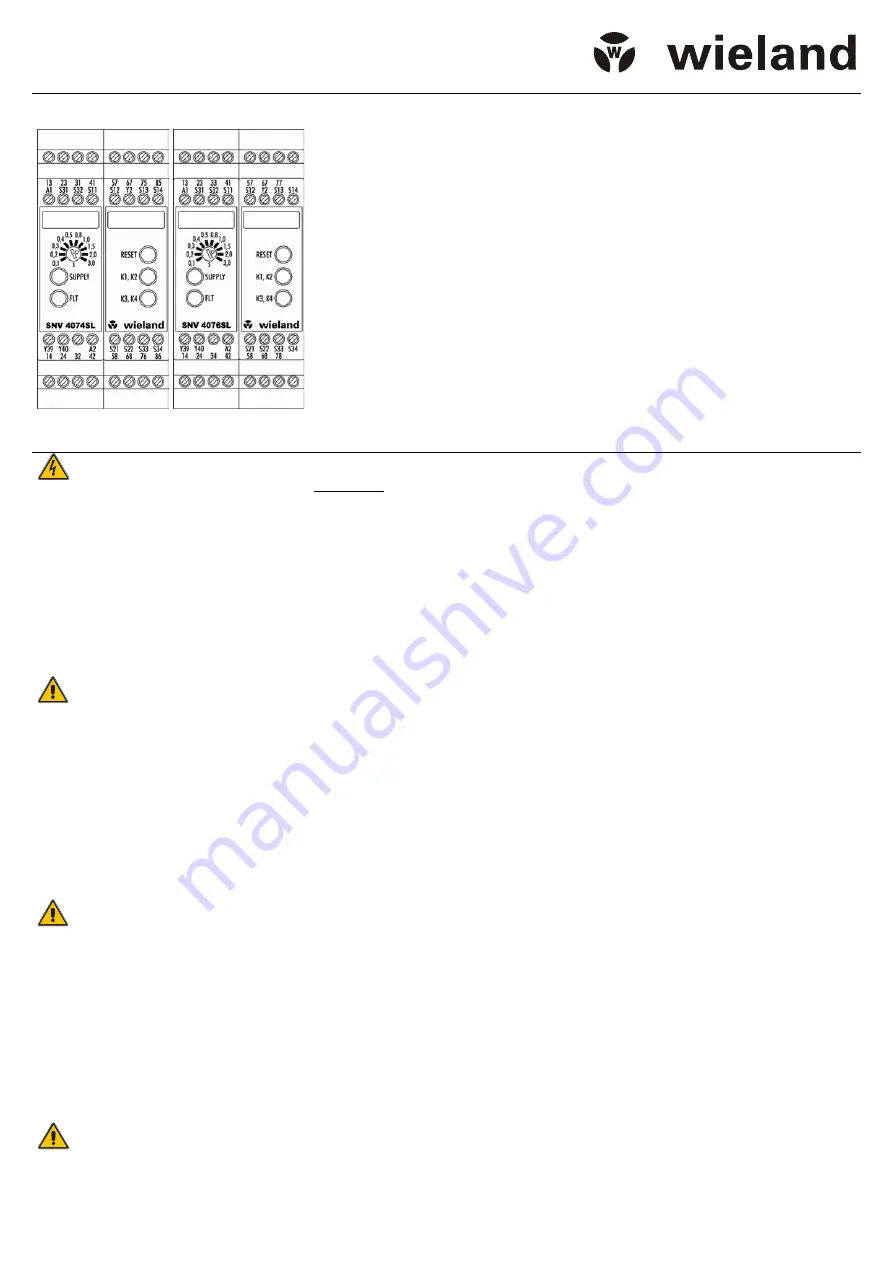
4
Translation of the original instructions
BA000527 - 09/2013 (Rev. H)
SNV 4074SL / -A / -C, SNV 4076SL / -A / -C
Basic device with release delay (OFF delay) for EMERGENCY STOP and safety door
applications
Basic device according to EN 60204-1:2005 and EN ISO 13849-1:2008 for single or two-
channel EMERGENCY STOP monitoring.
PL “e”/category 4 in accordance with EN ISO 13849-1:2008
SIL CL3 according to DIN EN 62061:2005
Stop Category 0 and 1 according to DIN EN 60204-1
Manual or automatic start with monitoring of the feedback loop of external contactors
With or without crossover detection
2 (3) not delayed and 2 (3) delayed enabling current paths
Discretely adjustable OFF delay with separate control input for the premature ending of the
OFF delay
For processing signals from output signal switching devices (OSSD) of a light grid according
to DIN EN 61496-1
Use in combustion plants according to EN 50156-1:2005 SNS 3
Power supply 24 V DC or 115-230 V AC
Device versions
SNV 4074SL: 0,1-3s / 0-30s / 0-300s
with fixed screw clamp terminals
SNV 4074SL-A: 0,1-3s / 0-30s / 0-300s
with pluggable screw clamp terminals
SNV 4074SL-C: 0,1-3s / 0-30s / 0-300s
with pluggable spring-loaded terminals
SNV 4076SL: 0,1-3s / 0-30s / 0-300s
with fixed screw clamp terminals
SNV 4076SL-A: 0,1-3s / 0-30s / 0-300s
with pluggable screw clamp terminals
SNV 4076SL-C: 0,1-3s / 0-30s / 0-300s
with pluggable spring-loaded terminals
Safety regulations
Device and function description
SNV 407xSL
The SNV 407xSL is an electronic, redundant and self-monitoring safety switching
device for EMERGENCY STOP equipment according to DIN EN 60204-1 with positively driven re-
lays.
Basic function:
After applying the supply voltage to the terminals A1/A2 and closed safety cir-
cuits, the enabling current paths are closed when a reset signal is established. The enabling cur-
rent paths are opened when the safety circuits are opened/de-energised.
Operating modes / System functions
Single or two-channel actuation
In the case of single-channel actuation, both the safety
circuits CH1 and CH2 are connected in parallel and are separated for two-channel actuation
(see Installation 1 to 4).
Without crossover detection
Both safety circuits are connected to positive potential (see
Installation 2).
With crossover detection
The safety circuit CH1 is connected to negative potential and the
safety circuit CH2 to positive potential (see Installation 3).
Reset function with starting lockout
The Reset button is connected between S33 and S34.
In order to activate the relay, the Reset button must be pressed and released again (trigger-
ing with falling edge). No enable is performed if the button is not released (see Installation
6).
Reset function without starting lockout
The reset input S14 is connected to S13. In the case
of closed feedback circuits, the relays activate with the closing of the safety circuits (see In-
stallation 5).
OSSD compatible
Output signal switching devices (OSSD) of a light barrier or other safety
sensors with semiconductor outputs can be processed. Test pulses which are < t
TP
do not in-
fluence the device functions. Test pulses > t
TP
can result in deactivation of the relays (see In-
stallation 4).
Release delay (OFF delay)
The OFF-delayed part (K3/K4) switches off after opening the safe-
ty circuits according to the specified delay time. Switching on again is not possible until after
expiry of the OFF delay.
Time-Clear
Premature ending of the OFF delay. If the connection Y39/Y40 is opened during
the time delay, the OFF delay is ended immediately and the relays K3/K4 switch off (see In-
stallation 7).
Feedback circuit
The feedback circuit of the not delayed and of the delayed part is connected
between S13/Y2 (see Installations 5 and 6).
Discrepancy time
Within this time, both the input signals of the safety circuits can have
different states without this resulting in the relays switching off.
Please also observe the information from your professional trade association!
The safety functions are not evaluated by UL. The approval is accomplished according to UL 508,
general use applications.
The installation, commissioning, modification
and retrofitting must only be performed by a
qualified electrician!
Disconnect the device / the system from the
power supply before starting work! In the case
of installation and system errors, mains voltage
can be present on the control circuit in the case
of non-galvanically isolated devices!
Observe the electrotechnical and professional
trade association safety regulations for the in-
stallation of the equipment.
Opening the case or other manipulation voids
any warranty.
Attention!
In the case of improper use or any use other
than for the intended purpose, the device must
no longer be used and any warranty claim is
void. Invalidating causes can be:
strong mechanical loading of the device such
as, e.g. in the case of falling or voltages, cur-
rents, temperatures, humidity outside the speci-
fication.
Please always check all safety functions in ac-
cordance with the applicable regulations during
initial commissioning of your machine / system
and observe the specified inspection cycles for
safety devices.
Attention!
Take the following safety precautions before
starting installation / assembly or dismantling:
1.
Disconnect the device / the system from
the power supply before starting work!
2.
Secure the machine / system against being
switched on again!
3.
Confirm that no voltage is present!
4.
Ground the phases and short to ground
briefly!
5.
Cover and shield neighbouring live parts!
6.
The devices must be installed in a switch
cabinet with a protection class of at least
IP 54.
Attention!
Limited contact protection! Degree of protection
according to DIN EN 60529.
Case/terminals: IP 40 / IP 20.
Finger-proof according to DIN VDE 0660 Part 514.