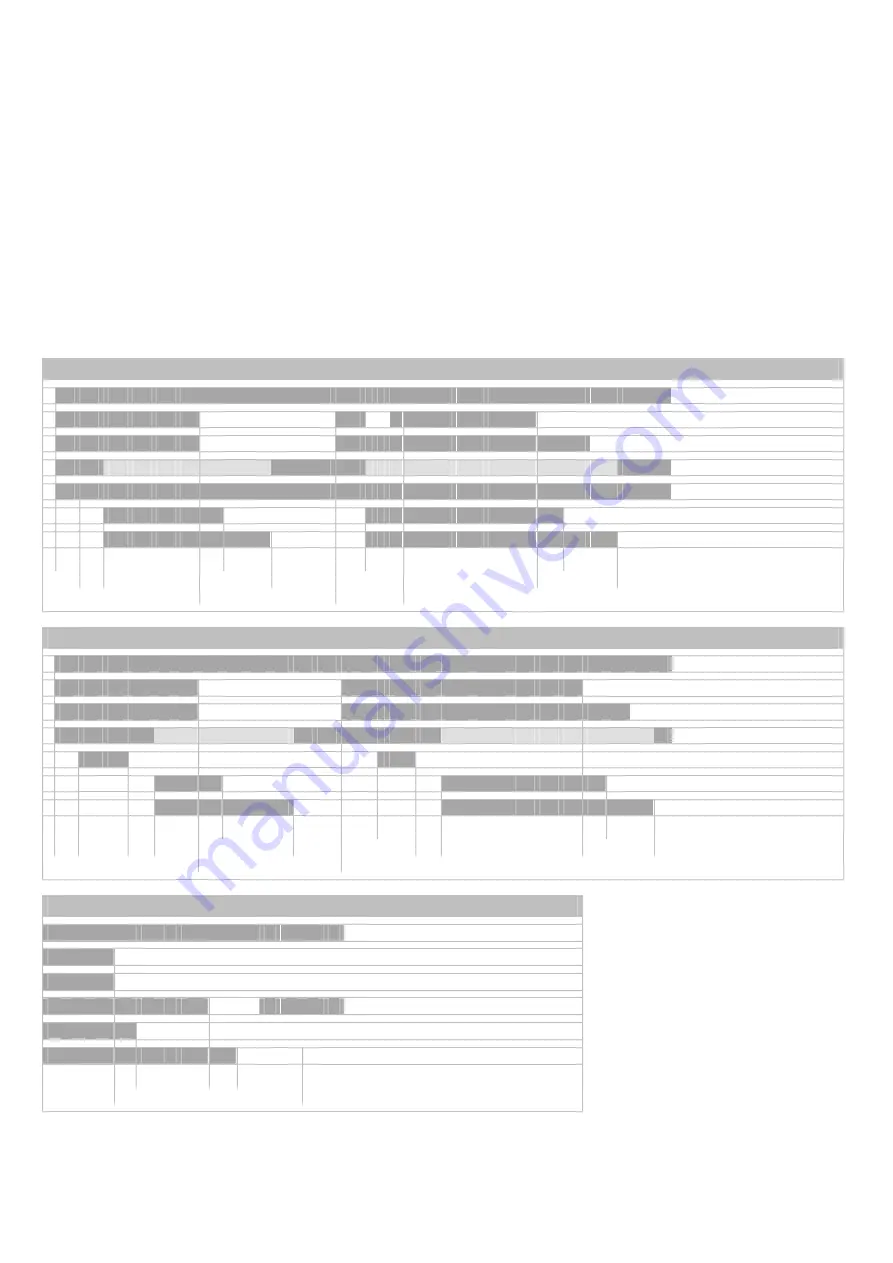
5
Proper Use
The devices are safety switching devices. They must only be used as components of safety equipment on machines intended to protect persons, material and
machines.
Note
The performance level (PL) and safety category according to EN ISO 13849-1 depends on the external wiring, the application case, the choice of control
devices and their location on the machine.
The user must carry out a risk assessment in accordance with ISO 14121-1.
The entire system/machine must undergo validation in accordance with the applicable standards on the basis of this.
Operating the device outside the specification can result in malfunctions or destruction of the device.
Comply with the specified maintenance and inspection intervals.
Checking the proper function must be performed before commissioning, after replacement of modules and in the case of changes to an accepted instal-
lation. Entry to the control cabinet has to be protected against access by unauthorized persons.
The highest voltage present is decisive for dimensioning the insulation of the lines to be connected.
The devices must be installed in a switch cabinet with a protection class of at least IP 54.
In the case of operation of the device in two-channel mode without crossover protection, actions must be taken which prevent a crossover short-circuit
such as, e.g. separated line laying of both the safety circuits.
The expansion units of the SNE series or external contactors with positively-driven contacts can be used for duplicating the enabling current paths
External loads have to be equipped with appropriate protective circuits (e.g. RC elements, varistors, suppressors) to reduce electromagnetic
interference and increase the life cycle of the original circuit elements.
The control inputs and outputs are only used for the connection of control devices according to the operating manual and not for the connection of
external consumers such as, e.g. lamps, relays or contactors.
Function diagram 1, automatic start (Installation 1, 2, 3, 4 and 5)
A1, A2
CH1, S12/S22
CH2,
S32
Y2
S14
K1/K2/K5
K3/K4
t
B
t
R
t
A
t
R
t
A
t
RV
t
RV
t
W
t
D
Function diagram 2, manual monitored start (Installation 1, 2, 3, 4 and 6)
A1, A2
CH1,
S12/S22
CH2,
S32
Y2
S34
K1/K2/K5
K3/K4
t
M
t
R
t
M
t
R
t
B
t
A
t
RV
t
A
t
RV
t
W
Function diagram 3, end delay time with Y40 (Installation 7)
A1, A2
t
B
= ready time
CH1, S12/S22
t
A
= response time
CH2, S32
t
M
= minimum actuation time
Y40
t
R
= release time
K1/K2/K5
t
RV
= release delay time
K3/K4
t
W
= recovery time
t
R
t
R
t
D
= discrepancy time
t
RV