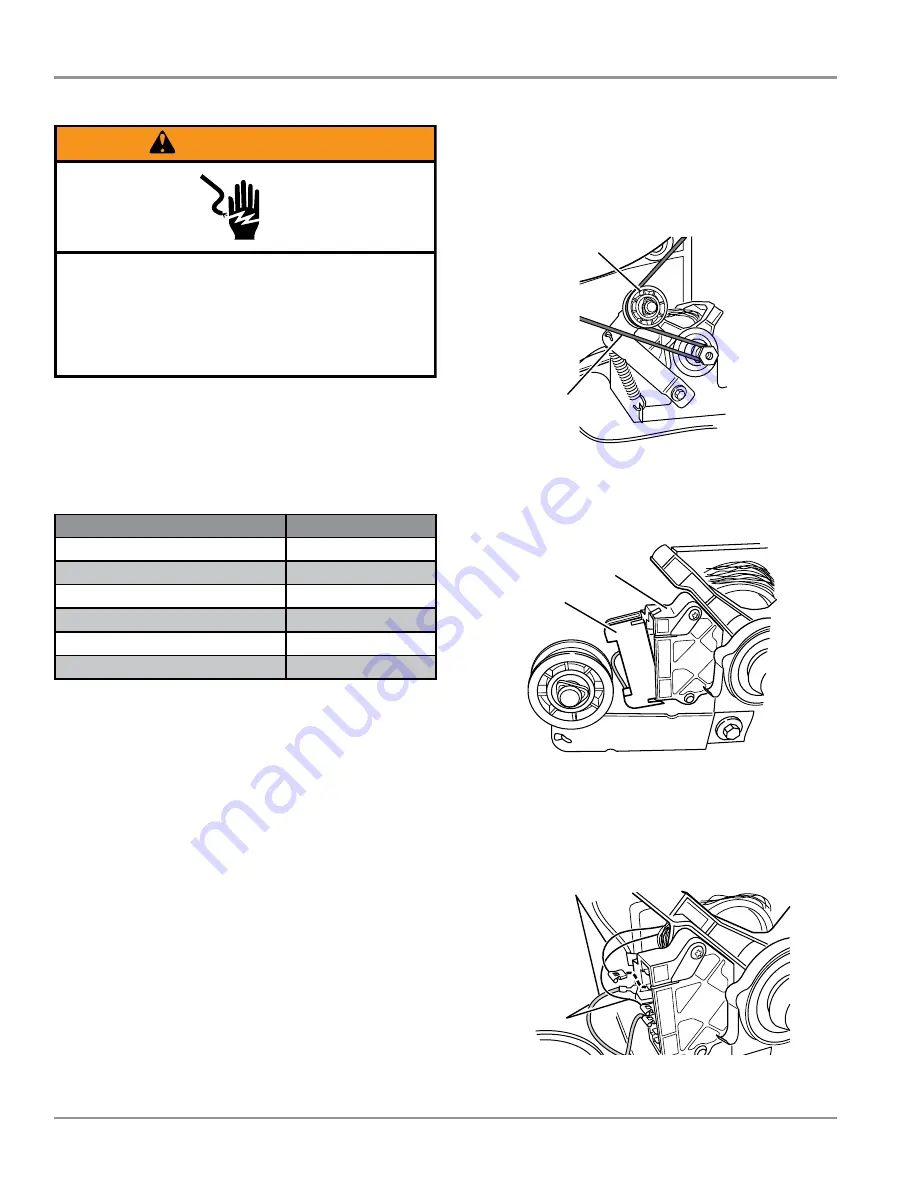
6-8
n
HybridCare™ Dryer with Heat Pump Technology
TESTING
6. Check the wiring and components in the path between
these measurement points by referring to the wiring
diagram on page 6-3.
7. Check the drive motor. Slowly remove the drum belt from
the spring-loaded pulley, gently letting the pulley down.
See figure 1
.
3$*(
FOR SERVICE TECHNICIAN’S USE ONLY
DO NOT REMOVE OR DESTROY
¾
If continuity exists for both connections,
go to step 6.
¾
If an open circuit is found, check the integrity
of the connections of the power cord to the
harness in the dryer; harness to the CCU;
and the integrity of the power cord itself.
5.
If it is necessary to replace the power
cord, remove the retaining clip that secures
the cord to the back panel. Disconnect the
cord from the main harness and the ground
wire from the rear panel, then pull out the
power cord.
6.
Visually check that ALL connectors are
fully inserted into the CCU.
7.
Visually check that ALL connectors are
fully inserted into the UI.
8.
Reassemble all parts and panels.
9.
Plug in dryer or reconnect power.
10.
Perform steps under “Install Diagnostics”,
page 6, to verify repair.
TEST #3: Motor Circuit
This test will check the wiring to the motor
and the motor itself. The following items are
part of this motor system:
NOTE:
Refer to strip circuit on page 20
to diagnose drive motor.
1.
Unplug dryer or disconnect power.
2.
Remove top panel to access the machine
electronics.
3.
Check for loose, worn, or damaged drum
belt—repair as necessary.
4.
Door Switch problems can be uncovered
by following procedure under TEST #7: Door
Switch, page 18; however, if this was not
done, the following can be performed without
applying power to the dryer. Connect an
ohmmeter across CCU P8-3 (neutral, white
wire) and P8-4 (door, tan wire).
¾
With the door properly closed, the ohmmeter
should indicate a closed circuit (0–2
1
).
¾
If not, check harnesses and connections
between CCU and door switch. If good,
replace the door switch assembly.
5.
Motor Circuit Check - Access the CCU and
measure the resistance across P8-4 and P9-1.
¾
If resistance across P8-4 and P9-1 is in
the range of 1 to 6
1
, the motor circuit is
acceptable. Replace the CCU.
¾
Otherwise, continue to step 6.
6.
Check the wiring and components in the
path between these measurement points by
referring to the wiring diagram on page 23.
7.
Check the drive motor. Slowly remove the
drum belt from the spring-loaded pulley, gently
letting the pulley down. See figure 5.
Part of Motor System
Electric
Dryer
Drum belt
ü
Door switch
ü
Harness/connection
ü
Drive motor
ü
Centrifugal switch
Machine control electronics
ü
ü
Figure 5 - Slowly remove drum belt.
Drum
Belt
Pulley
P9
1
5
1
P/N XXXXXX R
ev X
Date Code YDDD
-xx
XXXX
-XXX
MADE IN COO
L1
COM
P8
L1
N
Neu
N
Neu
Power Cord
Plug
CCU
Figure 4b - Plug-to-terminal connections
for electric dryer.
Figure 1 - Slowly remove drum belt.
8. Remove the white connector from the drive motor switch.
See figure 2.
3$*(
FOR SERVICE TECHNICIAN’S USE ONLY
DO NOT REMOVE OR DESTROY
1
5
3
4
6
2
Figure 6 - Remove white connector.
White
Connector
Drive Motor
Switch
8.
Remove the white connector from the drive
motor switch. See figure 6.
9.
Remove the bare copper wire terminal from
pin 5 of black drive motor switch. See figure 7.
10.
Using figure 7 and the strip circuit on
page 20, check for the resistance values of
the motor’s Main and Start winding coils as
shown in the following table.
NOTE:
Main and Start winding coils must be
checked at the motor.
1
5
3
4
6
2
Main Winding:
Lt. Blue Wire in Back
and Bare Copper Wire
Start
Winding:
Lt. Blue Wire
in Back and
Bare Copper
Wire
Figure 7 - Main and start winding measure points.
Winding
Resistance
in ohms
Contact Points
of Measurement
MAIN
3.3–3.6
Lt. blue wire in back at pin 4
and bare copper wire terminal
removed from pin 5 of black
drive motor switch
START
2.7–3.0
Lt. blue wire in back at pin 4
and bare copper wire terminal
on pin 3 of black drive
motor switch
¾
If the resistance at the motor is correct,
there is an open circuit between the motor
and CCU.
¾
If the Main or Start winding resistance is
much greater or less than the values listed
in the table above, replace the motor.
11.
Reassemble all parts and panels.
12.
Plug in dryer or reconnect power.
13.
Perform steps under “Install Diagnostics”,
page 6, to verify repair.
TEST #4: Heat System
This test is performed when either of the
following situations occurs:
✓
Dryer does not heat
✓
Heat will not shut off
This test checks the components making up
the heating circuit. The following items are
part of this system:
Part of Heating System
Electric
Dryer
Harness/connection
ü
Heater relay
ü
Heat element assembly
ü
Centrifugal switch
ü
Outlet thermistor
ü
Compressor thermistor
ü
Machine control electronics
ü
Console electronics and housing
assembly
ü
Figure 2 - Remove white connector
9. Remove the bare copper wire terminal from pin 5 of black
drive motor switch. See figure 3.
3$*(
FOR SERVICE TECHNICIAN’S USE ONLY
DO NOT REMOVE OR DESTROY
1
5
3
4
6
2
Figure 6 - Remove white connector.
White
Connector
Drive Motor
Switch
8.
Remove the white connector from the drive
motor switch. See figure 6.
9.
Remove the bare copper wire terminal from
pin 5 of black drive motor switch. See figure 7.
10.
Using figure 7 and the strip circuit on
page 20, check for the resistance values of
the motor’s Main and Start winding coils as
shown in the following table.
NOTE:
Main and Start winding coils must be
checked at the motor.
1
5
3
4
6
2
Main Winding:
Lt. Blue Wire in Back
and Bare Copper Wire
Start
Winding:
Lt. Blue Wire
in Back and
Bare Copper
Wire
Figure 7 - Main and start winding measure points.
Winding
Resistance
in ohms
Contact Points
of Measurement
MAIN
3.3–3.6
Lt. blue wire in back at pin 4
and bare copper wire terminal
removed from pin 5 of black
drive motor switch
START
2.7–3.0
Lt. blue wire in back at pin 4
and bare copper wire terminal
on pin 3 of black drive
motor switch
¾
If the resistance at the motor is correct,
there is an open circuit between the motor
and CCU.
¾
If the Main or Start winding resistance is
much greater or less than the values listed
in the table above, replace the motor.
11.
Reassemble all parts and panels.
12.
Plug in dryer or reconnect power.
13.
Perform steps under “Install Diagnostics”,
page 6, to verify repair.
TEST #4: Heat System
This test is performed when either of the
following situations occurs:
✓
Dryer does not heat
✓
Heat will not shut off
This test checks the components making up
the heating circuit. The following items are
part of this system:
Part of Heating System
Electric
Dryer
Harness/connection
ü
Heater relay
ü
Heat element assembly
ü
Centrifugal switch
ü
Outlet thermistor
ü
Compressor thermistor
ü
Machine control electronics
ü
Console electronics and housing
assembly
ü
Figure 3 - Main and start winding measure points
TEST #3 Motor Circuit
This test will check the wiring to the motor and the motor
itself. The following items are part of this motor system:
Part of Motor System
Electric Dryer
Drum belt
ü
Door switch
ü
Harness/connection
ü
Drive motor
ü
Centrifugal switch
ü
Machine control electronics
ü
NOTE:
Refer to strip circuit on page 6-9 to diagnose the drive
motor.
1. Unplug dryer or disconnect power.
2. Remove top panel to access the machine electronics.
3. Check for loose, worn, or damaged drum belt—repair as
necessary.
4. Door Switch problems can be uncovered by following
procedure under TEST #7: Door Switch, page 6-18;
however, if this was not done, the following can be
performed without applying power to the dryer. Connect
an ohmmeter across CCU P8-3 (neutral, white wire) and
P8-4 (door, tan wire).
¾
With the door properly closed, the ohmmeter should
indicate a closed circuit (0–2 Ω).
¾
If not, check harnesses and connections between
CCU and door switch. If good, replace the door switch
assembly.
5. Motor Circuit Check - Access the CCU and measure the
resistance across P8-4 and P9-1.
¾
If resistance across P8-4 and P9-1 is in the range of 1 to
6 Ω, the motor circuit is acceptable. Replace the CCU.
¾
Otherwise, continue to step 6.
For Service Technician Use Only
WARNING
Electrical Shock Hazard
Disconnect power before servicing.
Failure to do so can result in death or
electrical shock.
Replace all parts and panels before operating.
Summary of Contents for WED99HEDC0
Page 12: ...1 8 n HybridCare Dryer with Heat Pump Technology GENERAL INFORMATION Notes ...
Page 26: ...2 14 n HybridCare Dryer with Heat Pump Technology OPERATION Notes ...
Page 48: ...3 22 n HybridCare Dryer with Heat Pump Technology INSTALLATION Notes ...
Page 68: ...4 20 n HybridCare Dryer with Heat Pump Technology COMPONENT ACCESS Notes ...
Page 98: ...6 22 n HybridCare Dryer with Heat Pump Technology TESTING Notes ...
Page 100: ...W10764068A HybridCare Duet Dryer with Heat Pump Technology ...