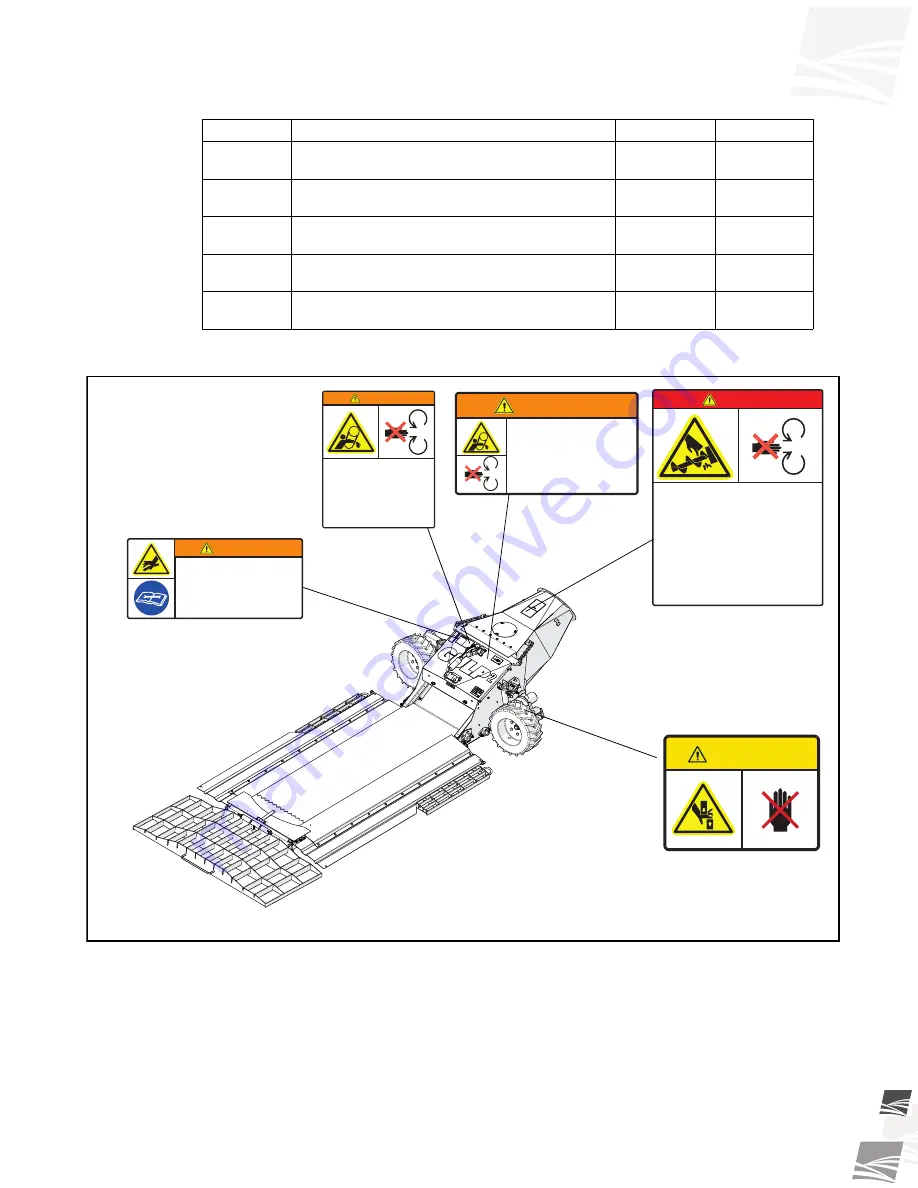
W
ESTFIELD
- GULP2 H
OPPER
2. S
AFETY
MKX130
AND
MKX160 M
ODELS
30962 R1
13
Figure 2.2 Safety Decal Locations
Table 2.1 Safety Decal Description, Detail, and Location Information
Number
Description
Location
Detail
20803
Missing guard hazard (Warning)
20804
Entanglement hazard (Warning)
20806
High pressure fluid hazard (Warning)
20813
Rotating flighting hazard (Danger)
21838
Pinch point (Caution)
DANGER
ROTATING FLIGHTING HAZARD
To prevent death or serious injury:
• KEEP AWAY from rotating auger flighting.
• DO NOT remove or modify auger flighting guards,
doors, or covers. Keep in good working order. Have
replaced if damaged.
• DO NOT operate the auger without all guards, doors,
and covers in place.
• NEVER touch the auger flighting. Use a stick or other
tool to remove an obstruction or clean out.
• Shut off and lock out power to adjust, service, or clean.
Made in Canada
20813
WARNING
HIGH PRESSURE FLUID HAZARD
Hydraulic fluid can cause serious injury if it
penetrates the skin. If it does, see a doctor
immediately.
• Relieve pressure before unhooking hydraulic line.
• Wear proper hand and eye protection, and use wood
or cardboard, not hands, when searching for leaks.
6
0
8
0
2
a
d
a
n
a
C
n
i
e
d
a
M
DECAL 20806
DECAL 20813
CAUTION
21838
Made in Canada
DECAL 21838
WARNING
MISSING GUARD HAZARD
To prevent serious injury or
death, shut off power and
reattach guard before operating
machine.
20803
Made in Canada
DECAL 20803
WARNING
ENTANGLEMENT HAZARD
To prevent serious injury or death:
• Keep body, hair, and clothing away from rotating
pulleys, belts, chains, and sprockets.
• Do not operate with any guard removed or
modified. Keep guards in good working order.
• Shut off and remove key or lock out power source
before inspecting or servicing machine.
Made in Canada
20804
DECAL 20804
Summary of Contents for GULP2 HOPPER MKX130
Page 6: ...1 INTRODUCTION WESTFIELD GULP2 HOPPER MKX130 AND MKX160 MODELS 6 30962 R1 ...
Page 16: ...2 SAFETY WESTFIELD GULP2 HOPPER MKX130 AND MKX160 MODELS 16 30962 R1 ...
Page 34: ...3 ASSEMBLY WESTFIELD GULP2 HOPPER MKX130 AND MKX160 MODELS 34 30962 R1 ...
Page 38: ...4 TRANSPORT WESTFIELD GULP2 HOPPER MKX130 AND MKX160 MODELS 38 30962 R1 ...
Page 40: ...5 PLACEMENT WESTFIELD GULP2 HOPPER MKX130 AND MKX160 MODELS 40 30962 R1 ...
Page 54: ...7 MAINTENANCE WESTFIELD GULP2 HOPPER MKX130 AND MKX160 MODELS 54 30962 R1 ...
Page 56: ...8 TROUBLESHOOTING WESTFIELD GULP2 HOPPER MKX130 AND MKX160 MODELS 56 30962 R1 ...
Page 60: ...9 APPENDIX WESTFIELD GULP2 HOPPER MKX130 AND MKX160 MODELS 60 30962 R1 ...