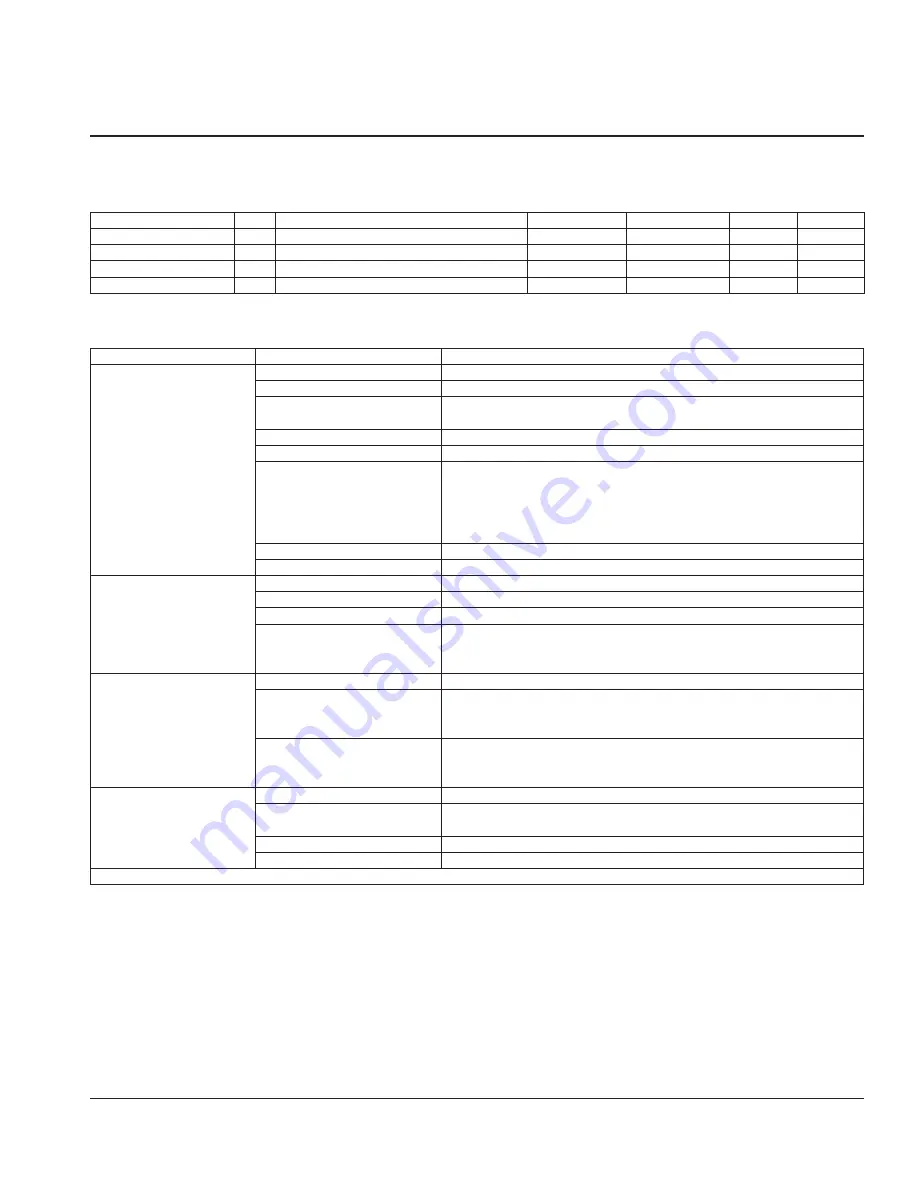
Document #: LIN_GO_SM_IMPLOPRO_S1600_INTL_4605727 – 9/20
Troubleshooting Guide – Gas Ovens
Serial Number L28563 and Above (Ovens with push button controls)
Old Model Number
→
New Model Number
Gas Type
Voltage
Hz
Phase
—
→
1631-xxx-E-Kxxxx
Natural
230 VAC
50 Hz
1
—
→
1632-xxx-E-Kxxxx
LP Gas
230 VAC
50 Hz
1
1633-000-EA
→
1633-00z-E-Kxxxx
Natural Gas
230 VAC
50 Hz
1
1634-000-EA
→
1634-00z-E-Kxxxx
LP Gas
230 VAC
50 Hz
1
NOTE: When checking components on left side of unit, be sure to check for proper connections in power connector (marked
P. C. on schematic diagram), located inside motor cover.
PROBLEM
CAUSE
CORRECTION
Oven fan will not run
Incoming power supply
Check breakers/reset if required. Call power company if needed.
Oven fan switch
Check continuity between switch terminals.
Hi-limit thermostat(s), control
box
Terminals are normally closed. If open, reset thermostat and test oven for
proper operation. If it will not reset, replace thermostat.
Fan fuse
Check, replace if necessary.
Fuseholder
Check, replace if necessary.
Oven fan relay
Check for power to coil of oven fan relay. If no voltage is present, trace
wiring back to hi-limit thermostat. Check for supply voltage at terminal
#6 of the relay. If no voltage is present, trace wiring back to fuse holder.
If voltage is present, at the relay coil, check to ensure the contacts are
closing.
Capacitor(s)
Check for opens, shorts, or grounds.
Motor(s), main fan
Check for opens, shorts, or grounds.
No control box cooling
Oven fan switch
(See “Oven fan will not run”.)
Hi-limit thermostat(s)
(See “Oven fan will not run”.)
Oven fan relay
(See “Oven fan will not run”.)
Cooling fan(s)
Supply voltage should now be at these motors. If voltage is present, check
motor for open, shorts, or grounds. WITH POWER OFF: Check for locked
rotor.
No automatic control box
cooling
Incoming power supply
Check circuit breakers, reset if needed. Call power company if needed.
Cooling fan thermostat(s)
Check the cooling fan thermostat (thermostat closes at 120°F and opens
at 100°F). With the cooling fan thermostat preheated, check for continuity.
If switch is open, replace.
Cooling fan(s)
Supply voltage should now be at these motors. If voltage is present, check
motor for opens, shorts or grounds. WITH POWER OFF: Check for locked
rotor.
Oven will not heat
Gas supply
Check for adequate gas supply to oven.
Manual gas shut off valve
Check to see that the manual gas shut off valve is open. Also check flexible
gas line connection for any damage.
Fan switch
Check to see that the fan switch is on.
Main oven fan
Check if main oven fan is operating. If not, refer to “Oven fan will not run”.
NOTE: These ovens utilize 2 complete burner/temperature control systems. Each system will follow the same troubleshooting sequence.
Section 5
Troubleshooting