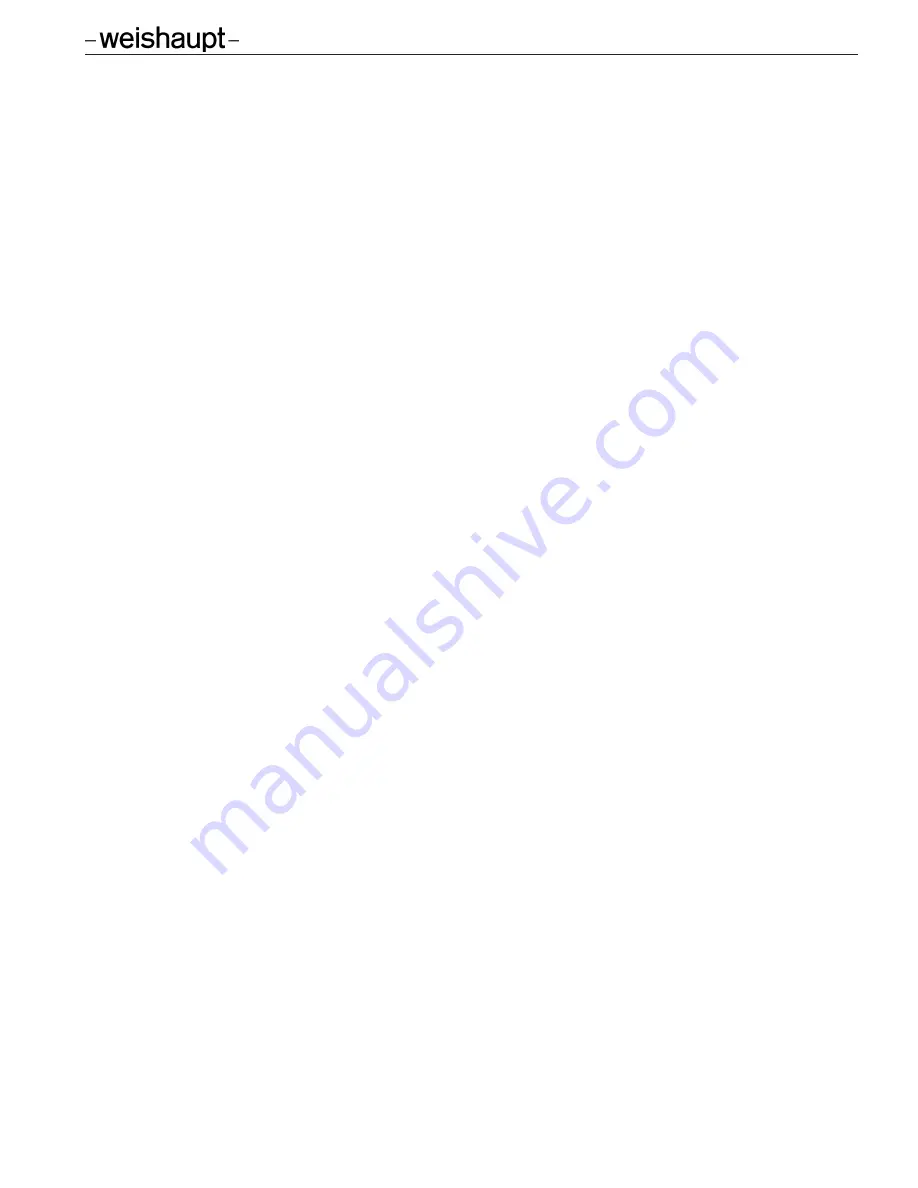
6
1 User instructions
1.2 General Instructions
Any work on the burner or applicable interfaced products (controls) must be complet-
ed within the guidelines of the manufacturer’s instructions and applicable local and
national codes. Such work must only be undertaken by fully qualified and trained per-
sonnel, familiar with the products.
The operation of all safety devices including limit circuits, monitoring equipment and
regulating equipment must be tested and correctly adjusted before the installation is
left unattended.
IMPORTANT
Burners must have at least one shutdown every 24 hours of operation; otherwise the
burner should be equipped with self-check flame sensing devices.
Installation
Standard Weishaupt burners are designed for indoor use only. For outdoor installa-
tions, contact your Weishaupt representative.
The installation of any Weishaupt product must be carried out by fully qualified and
licensed personnel.
The personnel performing the work must be familiar with, and operate within the appli-
cable local and national codes, such as CAN/CSA B149.1, 2, 3, CAN/CSA B139-00,
NFPA 54/58, NFPA30/31 and all other applicable codes and standards to the satis-
faction of the authority having jurisdiction. The installer is responsible for meeting all
these requirements and codes.
Attention must also be given to the minimum clearance of related appliance to permit
access for service and maintenance purposes and to the distance from combustible
material as required by all applicable codes to ensure safe operation.
General information for gas operation
An independent vent to outside of the building, sized in accordance with the regulator
manufacturer’s instructions, shall be provided. Where there is more than one regulator
at a location, each regulator shall have a separate vent to the outside.
Before being connected to the burner, the gas train shall be pressure tested using
either air or an inert gas as ruled by applicable codes.
The gas manifold pressures listed for each gas or combination gas/oil burner are
approximate figures obtained from tests on test boilers under ideal conditions.
Manifold pressures are only to be used as a guide during start up. The only accurate
method of determining the exact fuel throughput of the burner is by clocking the gas
meter and applying the respective correction factors for pressure and temperature.
Maintenance and Services
Burner components such as combustion manager, stepping motors, gas valves, nozzle
heads, etc are not user serviceable. Failure to heed this can cause property damage,
severe personal injury or loss of life.
We recommend regular plant maintenance of all combustion equipment. It saves fuel
and ensures good combustion. Excellent combustion quality is a pre-requisite for an
environment-friendly operation.
The annual maintenance and inspection program should include inspection of elec-
trodes, flame sensors, flame signal strength readings, inspection and testing of all
safeties including air pressure switch, flange switch, gas pressure switches, interlocks,
motor overloads, etc. Also the burner should be inspected for any mechanical damage.
The flame tube should be inspected for warpage, damage, holes, etc. The mixing head
and diffuser should be inspected for damage, missing bolts, etc. The head setting
should be checked and oil nozzles should be inspected and replaced as required.
Depending on the degree of contamination, the combustion air blower wheel, ignition
electrodes, flame sensor and air intake should be cleaned as required.
The moving/rotating burner parts require no lubrication. Motor bearings damage, which
is recognized and serviced quickly, prevents more extensive damage to the burner.
Development of noise in the motor bearings should be investigated immediately.
Installation and Operating Instructions
Gas burner WG20.../1-C ZM-LN (W-FM 25)
83055116 • 1/2016-05