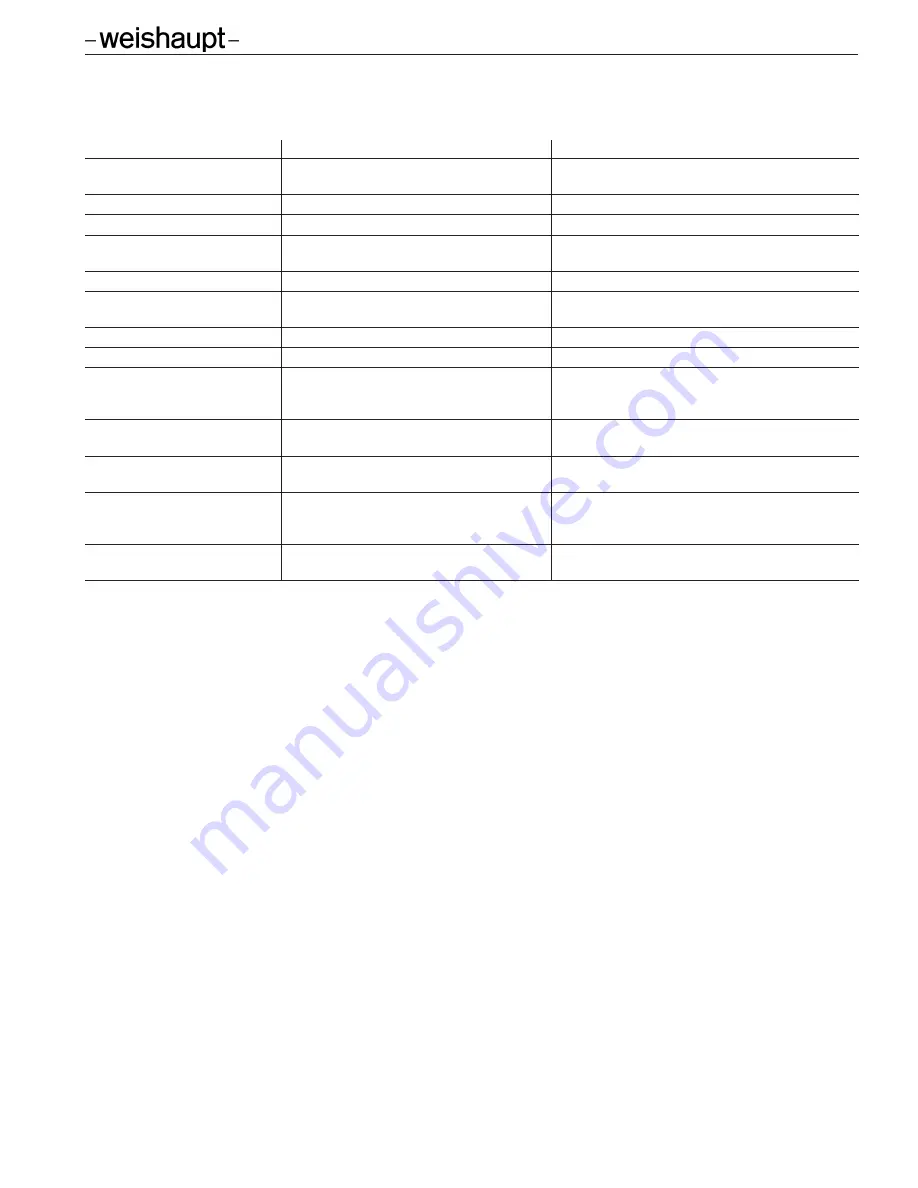
8 Maintenance and service
8.2 Service plan
Components
Criteria / design lifespan
(1
Maintenance or service procedure
Blower wheel
Soiling
Clean
Damage
Replace
Air duct
Soiling
Clean
Air damper
Soiling
Clean
Air pressure switch
Switch point
Check
250,000 burner starts or 10 years
(2
Replace
Ignition cable
Damage
Replace
Ignition electrode
Soiling
Clean
Damage / wear
Replace
Combustion manager
250,000 burner starts or 10 years
(2
Replacement recommended
Ionization cable
Damage
Replace
Ionization electrode
Soiling
Clean
Damage / wear
Replace
Recommendation: at least every 2 years
Flame tube / diffuser
Soiling
Clean
Damage
Replace
Gas valves
Fault identified
Replace
100,000 burner starts or 10 years
(2
Replace
Gas pressure regulator
Setting pressure
Check
Function / soundness
Replace
15 years
Replace
Gas pressure switch
Switch point
Check
50,000 burner starts or 10 years
(2
Replace
(1
The specified design lifespan applies for typical use in heating, hot water and steam
systems, as well for thermal process systems.
(2
If a criteria is met, perform the maintenance or service procedure.
48
Installation and Operating Instructions
Gas burner WG20.../1-C ZM-LN (W-FM 25)
83055116 • 1/2016-05
48
Installation and Operating Instructions
Gas burner WG20.../1-C ZM-LN (W-FM 25)
83055116 • 1/2016-05