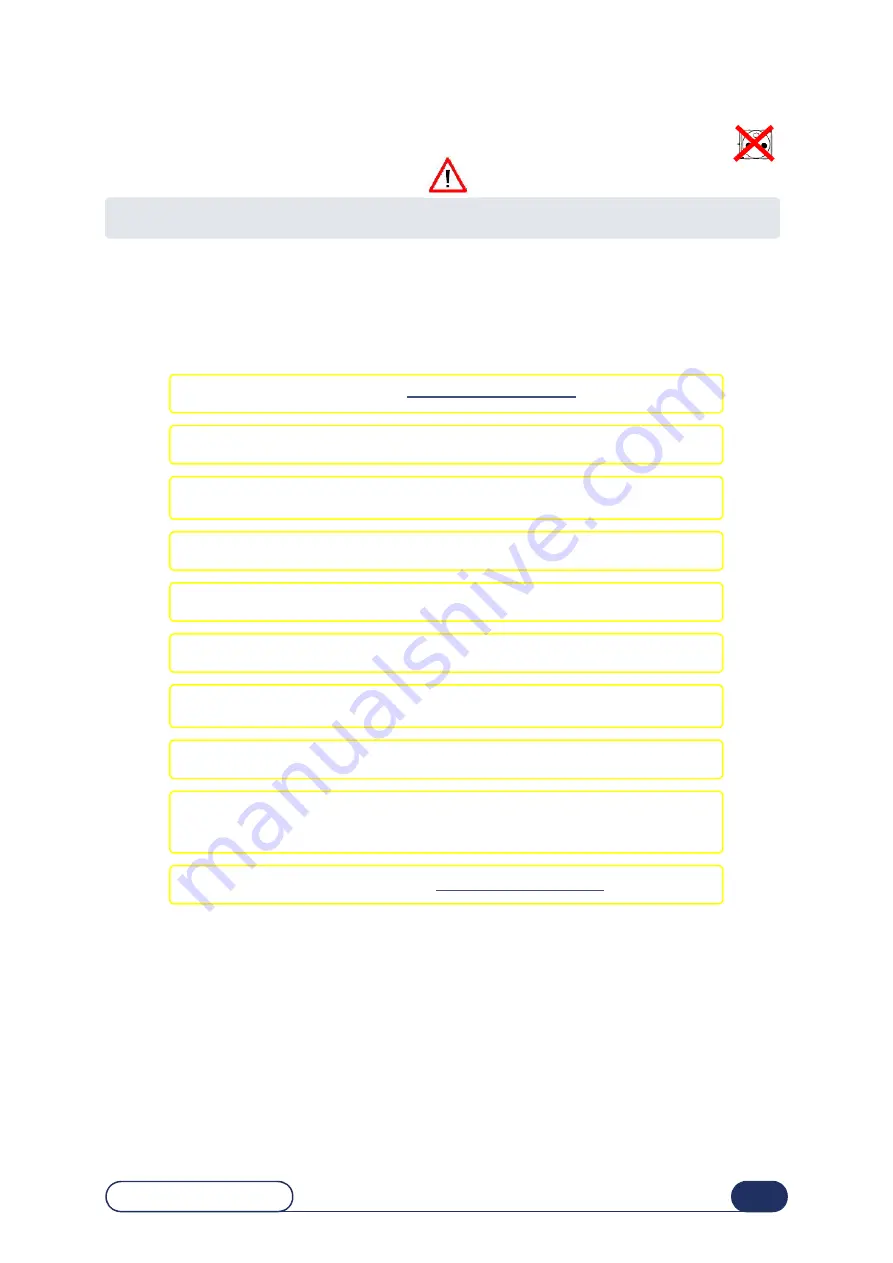
Edge 580 - Edge 550
1-19
=>
Installation
1.5 REMOVING THE INTERNAL CLAMPS
>
Before undertaking any operation, ensure that the machine is switched off : On/Off switch OFF
and mains plug disconnected.
1.5.1 R
EMOVING
THE
SET
SCREWS
>
The wheel unit, the carriage and the lens feeling system are immobilized by set screws which must be
removed before the machine is started.
To remove the set screws, follow the procedure below :
Flow chart 1-5 : Removal of the set screws
#1 Remove the machine covers : see Removing the covers.
#2 Unclip and remove the cover of the lens feeling system.
#3 Remove the headless nylon screws with a screwdriver and install them into
their nearby holes.
#4 Remove the cover of the lens feeling system.
#5 Go to the wheel unit clamping screw.
#6 Loosen and remove the clamping screw and the spacer.
#7 Reassemble the clamping screw and the spacer in the hole below the initial
socket so as to keep them in a safe place.
#8 Go to the carriage clamping screw.
#9 Unscrew the carriage clamping screw and free it from the body until the
carriage moves freely. DO NOT REMOVE THE SCREW ! Leave it in place so as
to keep it safe.
#10 Reassemble the machine covers : see Replacing the covers.
Summary of Contents for Edge 550
Page 2: ...Edge 580 Edge 550...
Page 5: ...Edge 580 Edge 550 1 5...
Page 10: ...1 INSTALLATION...
Page 13: ...Installation Unpacking the machine Edge 580 Edge 550 1 12...
Page 15: ...Installation Removing external clamps Edge 580 Edge 550 1 14...
Page 17: ...Installation Removing the shipping rails Edge 580 Edge 550 1 16...
Page 21: ...Installation Removing the internal clamps Edge 580 Edge 550 1 20...
Page 27: ...Installation Water connections Edge 580 Edge 550 1 26...
Page 29: ...Installation Electrical connections Edge 580 Edge 550 1 28...
Page 32: ...2 SAFETY PRECAUTIONS...
Page 33: ...2 32 Edge 580 Edge 550...
Page 35: ...Safety precautions Safety Edge 580 Edge 550 2 34...
Page 37: ...2 36 Safety precautions Useful hints Edge 580 Edge 550...
Page 38: ...3 UTILIZATION...
Page 39: ...3 38 Edge 580 Edge 550...
Page 51: ...Utilization General principles of use Edge 580 Edge 550 3 50...
Page 79: ...Utilization Normal use Edge 580 Edge 550 3 78...
Page 97: ...Utilization Special cases Edge 580 Edge 550 3 96...
Page 104: ...4 CONFIGURATION...
Page 105: ...4 104 Edge 580 Edge 550...
Page 117: ...Configuration Adjustment of the setting values Edge 580 Edge 550 4 116...
Page 122: ...5 MAINTENANCE...
Page 123: ...Maintenance Edge 580 Edge 550 5 122...
Page 127: ...Maintenance Visualize the components Edge 580 Edge 550 5 126...
Page 129: ...Maintenance Task list Edge 580 Edge 550 5 128...
Page 134: ...Maintenance Regular maintenance of the edger Edge 580 Edge 550 5 133...
Page 138: ...Maintenance Regular maintenance of the edger Edge 580 Edge 550 5 137...
Page 141: ...5 140 Edge 580 Edge 550 Illustration 5 4 Cleaning and replacing the removable visor 3 4 5 6 7...
Page 149: ...5 148 Edge 580 Edge 550 Ecran 5 3 Working in partial mode To quit...
Page 151: ...Maintenance Regular maintenance of the edger Edge 580 Edge 550 5 150...
Page 155: ...5 154 Edge 580 Edge 550 Ecran 5 5 Lens feelers adjustment...
Page 157: ...5 156 Edge 580 Edge 550 Illustration 5 10 Size adjustment Screen 1...
Page 162: ...Maintenance Adjustments Edge 580 Edge 550 5 161...
Page 163: ...5 162 Edge 580 Edge 550 Ecran 5 6 Adjustment of the flush of the mill bit...
Page 165: ...5 164 Edge 580 Edge 550 Ecran 5 7 Adjustment of the axis setting with the Alta XL...
Page 168: ...Maintenance Adjustments Edge 580 Edge 550 5 167...
Page 169: ...5 168 Edge 580 Edge 550 Ecran 5 8 Adjustment of the axis with the tool...
Page 171: ...5 170 Edge 580 Edge 550 Ecran 5 9 Adjustment of the touch screen...
Page 175: ...Maintenance Adjustments Edge 580 Edge 550 5 174...
Page 199: ...Edge 580 Edge 550 5 198 Maintenance...
Page 200: ...6 TESTS...
Page 201: ...6 200 Edge 580 Edge 550...
Page 207: ...6 206 Tests Operating principle Edge 580 Edge 550...
Page 208: ...7 CHEMISTRIE...
Page 209: ...7 208 Edge 580 Edge 550...
Page 211: ...Chemistrie Presentation Edge 580 Edge 550 7 210...
Page 214: ...8 TECHNICAL SPECIFICATIONS...
Page 215: ...8 214 Edge 580 Edge 550...
Page 217: ...Technical Specifications Characteristics Edge 580 Edge 550 8 216...
Page 221: ...Technical Specifications Technical Specifications Edge 580 Edge 550 8 220...