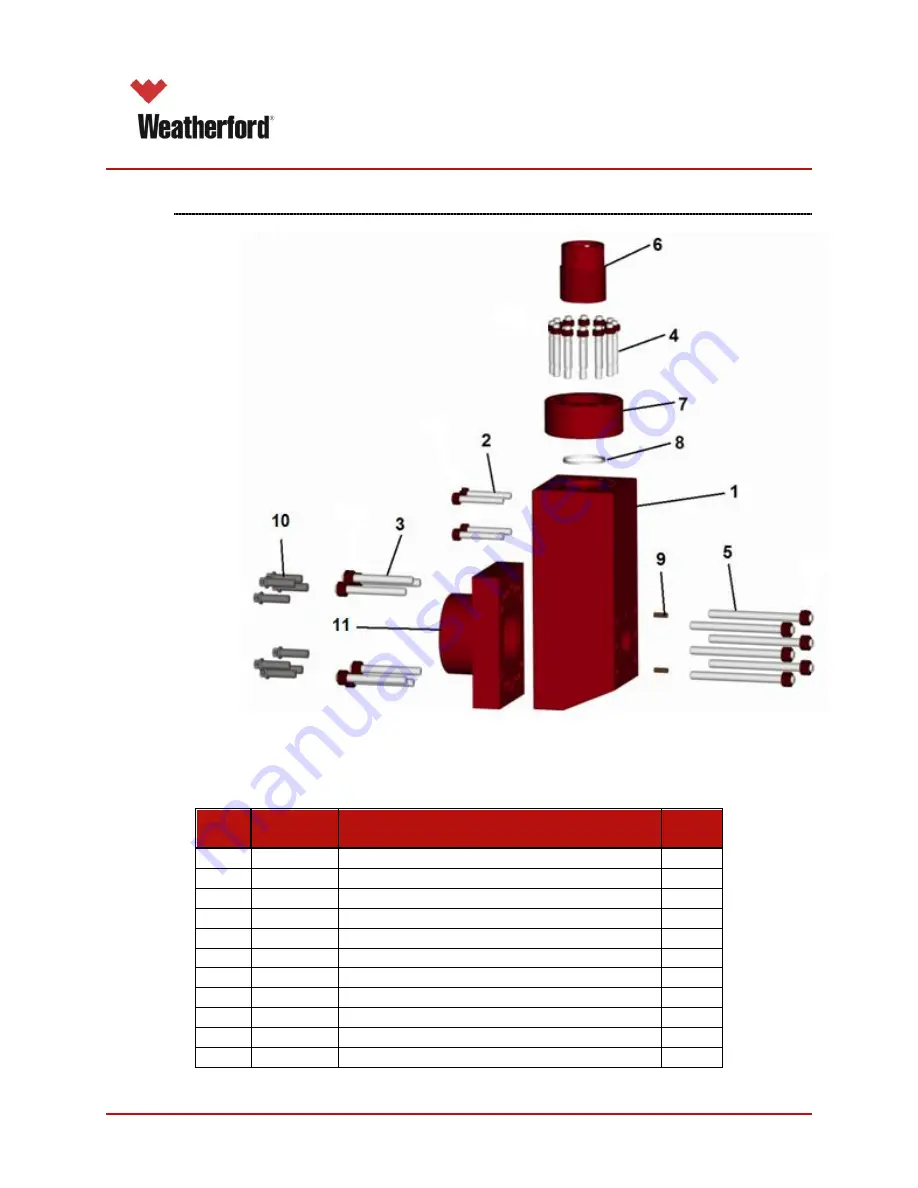
Pump and Fluid Systems
Chapter 7: Parts Lists
weatherford.com
110
MP-16 2-Piece 5000 psi January 2013
7.2.3
L-Style Discharge Module Assembly
Item
Part
Number
Description
Qty.
1316988
Module, Discharge
1
2
1738845
Stud, Discharge Manifold Mounting with Nut
6
3
1903638
Stud, Power End Mounting with Nut
10
4
1317854
Stud, , Flange Mounting with Nut
12
5
1418005
Stud, Suction Module Mounting with Nut
6
6
1317966
Gland, Valve Cover Screw
1
7
1317905
Flange, Valve Cover
1
8
1317766
Seal, Valve Cover
1
9
1418004
Locating Pins
2
10
1383132
Bolt, liner mounting plate
8
11
1317069
Flange, Liner Mounting MP-16
1