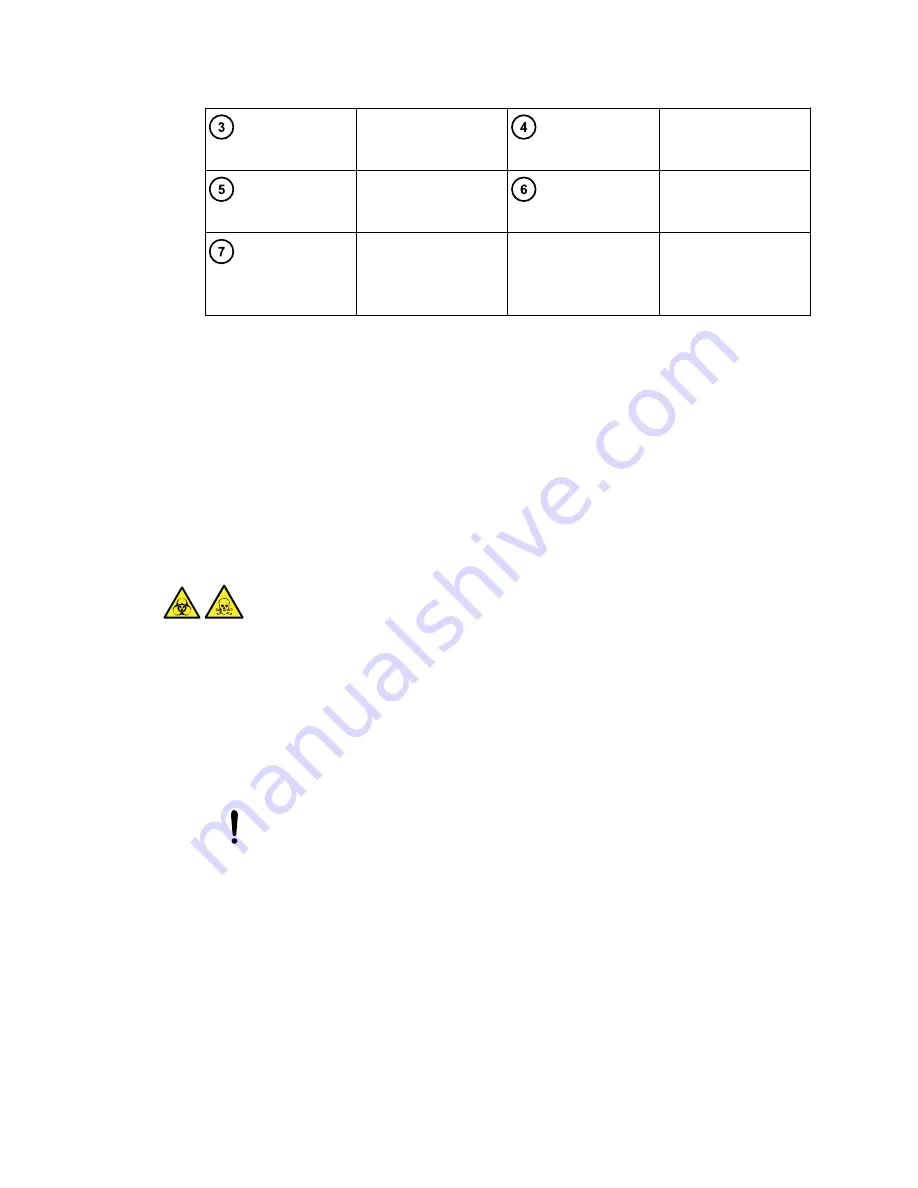
Electrical cable
Electrical cable
screws
Source enclosure
Source enclosure
thumbscrews
Probe capillary
connection at divert
valve
3. Disconnect the source enclosure's electrical cable from the front of the instrument by
loosening the screws, and pull the cable from the socket.
4. Loosen the two thumbscrews on the front of the source enclosure.
5. Remove the source enclosure by pulling it away from the instrument using both hands, and
place it on a flat surface.
3.6.2 Fitting the source enclosure to the instrument
Required tools and materials
• Chemical-resistant, powder-free gloves
Warning:
To avoid personal contamination with biologically hazardous or toxic compounds,
wear clean, chemical-resistant, powder-free gloves when performing this procedure.
To fit the source enclosure to the instrument:
1. Use both hands to slide the source enclosure onto the instrument's supporting rods.
2. To secure the enclosure against the instrument, tighten the two thumbscrews on the front
of the source enclosure.
Notice:
To avoid damage to the electrical connector's screws, do not
overtighten them.
3. Connect the electrical cable to the socket on the right-hand side of the instrument's front
panel and tighten the screws.
4. To avoid trapping and damaging the capillary in the instrument door, slide the capillary
beneath the retaining clips.
5. Close the instrument door.
6. In the UNIFI software, click
Operate
to put the instrument into Operate mode.
Notes:
August 20, 2021, 715005003 Ver. 04 (Previously released as Revision C)
Page 30