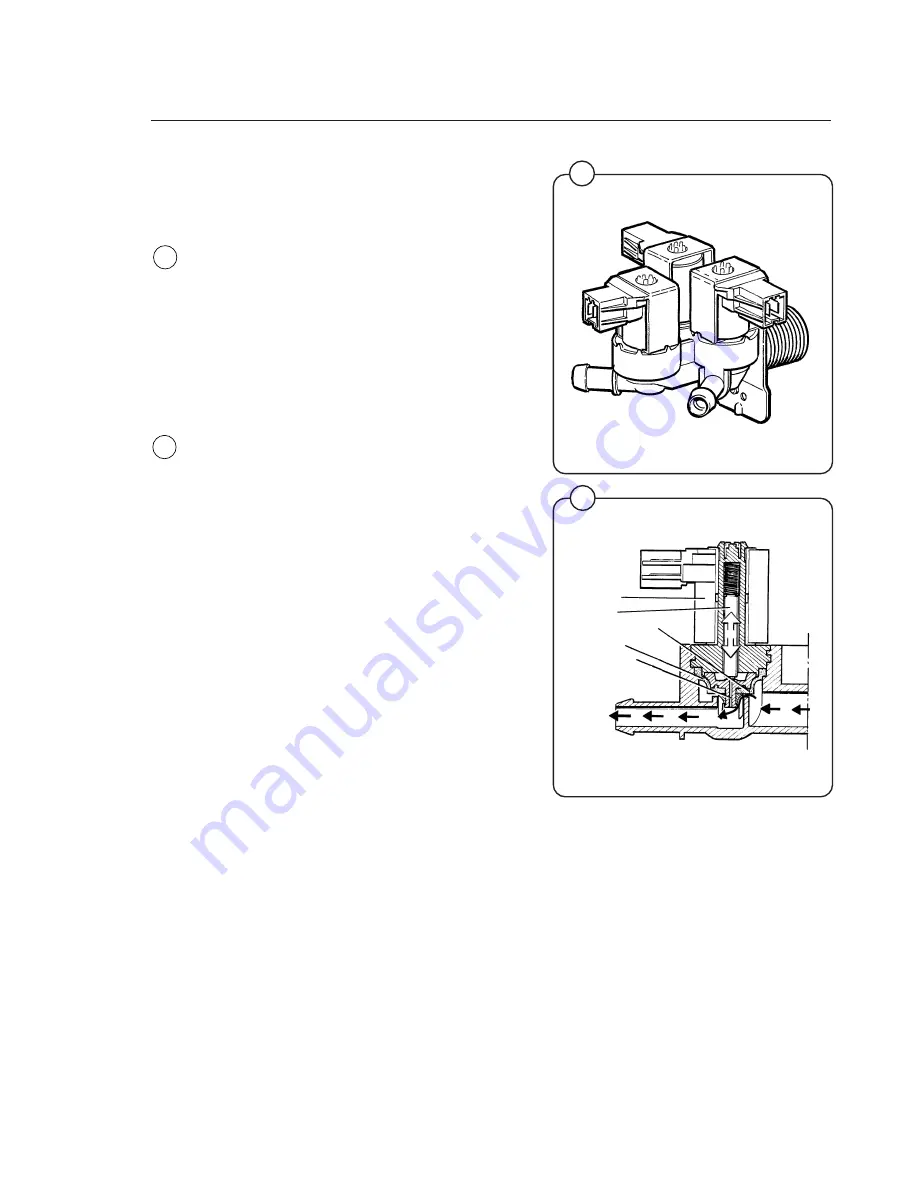
59
Mechanical and electrical design
Inlet valve, detergent
Construction
The valve has a single-inlet with either one, two
or three outlets, each with its own solenoid coil.
The body is made of heat-resistant polyamid
plastic and the solenoids encased in water-tight
plastic.
A filter screen on the inlet side prevents dirt from
entering the valve. Flow restrictors can be placed
at either the inlet or any of the outlets.
Operation
When the solenoid is energized, the spring-
loaded plunger is drawn up and the pilot valve in
the center of the diaphragm open. Because of
the difference in diameter between the pilot valve
opening and the ventilating hole in the diaph-
ragm, the pressure above the diaphragm drops
to a point where the admission pressure below
the diaphragm can lift the diaphragm, thus ope-
ning the valve.
When the current to the solenoid is cut off, the
plunger spring will press the plunger against the
pilot opening of the diaphragm. The pressure
above the diaphragm then rises to correspond to
the water inlet pressure and the pressure of the
spring will close the valve.
1161
1185
solenoid
plunger
ventilating hole
diaphragm
pilot valve
Fig.
68
Fig.
69
69
68