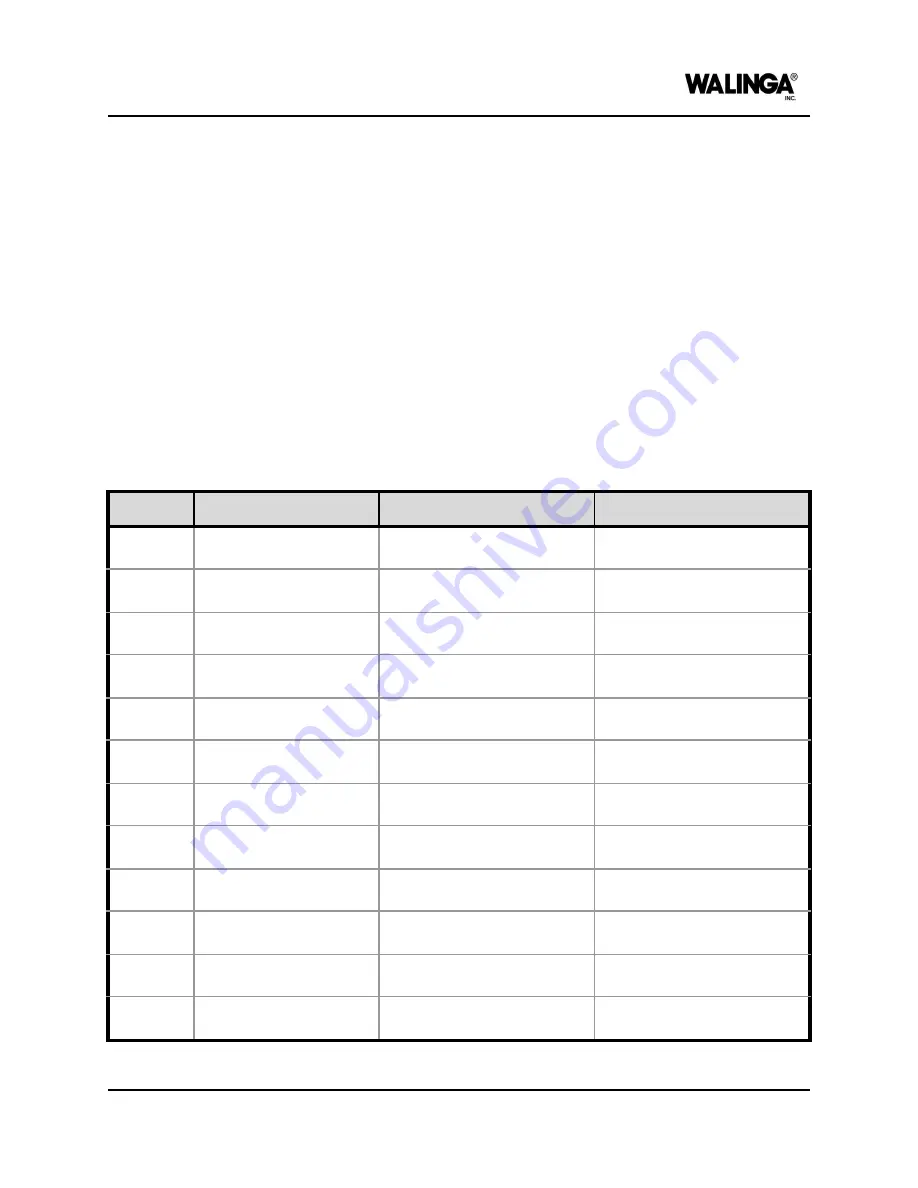
OPERATOR’S MANUAL
SAFETY TRAINING SIGN-OFF FORM
Walinga Inc. follows the general safety standards specified by the American Society of
Agricultural Engineers (ASAE) and the Occupational Safety and Health Administration (OSHA).
Anyone who will be operating and/or maintaining the airlock must read and clearly understand
all safety, operating and maintenance information presented in this manual.
Do not operate or allow any other individual to operate this equipment until such information has
been reviewed. Annually review this information with personnel.
Make periodic reviews of safety and operations a standard practice for all of your equipment. An
untrained operator is unqualified to operate an airlock.
The following sign-off sheet is provided for your record keeping to show that all personnel who
will be working with the equipment have read and understand the information in the operator’s
manual and have been instructed in the operation of the equipment.
DATE
EMPLOYEE’S NAME
EMPLOYEE’S SIGNATURE
EMPLOYER’S SIGNATURE
SAFETY
00-144474-0 A
4-11
Summary of Contents for Airlock 1008
Page 1: ...OPERATOR S MANUAL Airlock 1008 English 00 144471 0 A 2023 12 06...
Page 7: ...Identification of Machine AIRLOCK MODELS 1 1...
Page 9: ...Introduction AIRLOCK MODELS 2 1...
Page 15: ...Machine Configuration AIRLOCK MODELS 3 1...
Page 26: ...OPERATOR S MANUAL PAGE INTENTIONALLY LEFT BLANK 3 12 00 144473 0 A MACHINE CONFIGURATION...
Page 27: ...Safety AIRLOCK MODELS 4 1...
Page 39: ...Machine Life Cycle Procedures AIRLOCK MODELS 5 1...
Page 45: ...Operation AIRLOCK MODELS 6 1...
Page 54: ...OPERATOR S MANUAL PAGE INTENTIONALLY LEFT BLANK 6 10 00 144476 0 A OPERATION...
Page 55: ...Maintenance and Adjustments AIRLOCK MODELS 7 1...
Page 99: ...Specifications AIRLOCK MODELS 8 1...
Page 108: ...OPERATOR S MANUAL PAGE INTENTIONALLY LEFT BLANK 8 10 00 144478 0 A SPECIFICATIONS...
Page 109: ...Warranty AFTERMARKET PARTS AND SERVICE 9 1...
Page 113: ...Accessories and Attachments AIRLOCK MODELS 10 1...
Page 116: ...OPERATOR S MANUAL PAGE INTENTIONALLY LEFT BLANK 10 4 00 144480 0 A ACCESSORIES AND ATTACHMENTS...
Page 117: ...Parts List AIRLOCK 1008 MODEL 11 1...
Page 125: ...PAGE INTENTIONALLY LEFT BLANK...